An operations perspective on new twistlock handling in terminals
What would be the impact on the container terminal industry, if containers would be equipped with integrated twistlocks? A cost efficiency analysis demonstrates the significant cost savings to the industry and highlights safety, productivity and sustainability benefits. Potential implementation strategies are discussed.
Introduction
For a long time, the handling of twistlocks (or cones) and semi-automated twistlocks (SATL’s) has been a heavy burden for the container industry. The burden consists of the operational cost to place and remove these cones in every step of the container supply chain (on the vessel, on road trucks, on trains). Moreover, the handling (coning, deconing) typically takes place in areas where dense traffic takes place (e.g. apron of a container terminal), or where inherently unsafe situations take place (hold of the vessel, close to moving containers) hence causing being a source of injuries or casualties.
The introduction of the semi-automated twistlock already removed the locking and unlocking of the cones on the vessels, but still requires the manual placement and removal of the cones, as such only addressing some of the costs, and not addressing the safety issues.
Automated twistlock handling stations
There have been many efforts in developing automated twistlock handling stations (see also PT50-08), which could carry out this placement and removal of the twistlocks (see for instance www.kalp-gmbh.eu or www.ramspreaders.com). Although various tests have been carried out, it has not led to a large scale application. Here, various reasons can be identified, both technical and economical. To mention a few:
- Not all types of twistlocks can be handled
- When the twistlock station gets jammed, it is blocking a large area under the quay crane
- Ideally, the station is placed on a sill beam rather than on the ground. However, this adds a significant weight to the quay crane, which may have impact on the crane rail, and possibly reduces crane lifting capability
- The stations still have to be supplied with sufficient twistlocks
- The station needs to be replaced every time the quay crane moves, even when it moves only half a meter the station is not positioned correctly
- The investment required for a single station is quite high (>1M Euro), leading to a quite long return on investment
- Is not easily applicable to on dock and inland rail environments
- Requires skilled labour for maintenance
- Reduces productivity in bombcart environments.
Figure 1: Automated twistlock handling station (RAM, left; KALP, right)
UCLS: how it works
Another development, and the focal point of this paper, is the Universal Container Locking System UCLS, a system that is fitted into the corner castings of a container, and fulfills the container locking/unlocking without the need to place/remove it every time a container gets handled.
The UCLS was devised upon the premise that the container shipping industry needs a single, safe, easily adaptable and truly automated system for securing containers during transport, across the entire container supply chain. It is designed to improve safety, productivity, environmental sustainability and profitability for shipping companies, railroads and terminal operators.
The UCLS is in the final stages of development and early stages of field testing with gantry cranes, straddle carriers, top picks, side picks etc. The safety and economic opportunities are compelling and worthy of serious consideration by the maritime community (shipping companies and terminal operators), railroads and trucking community.
Figure 2.1 – 2.3: UCLS A brief description of the UCLS is provided where with numerous animations, videos answers to frequently asked questions and additional details provided at www.staffaipi.com
Figure 2.1 shows a UCLS locking unit mounted in the lower corner fitting of a standard ISO container. A UCLS actuating unit is housed in the upper corner fittings of containers (Figure 2.2). Simple, rugged linkage connects the actuating and locking units. The linkage is protected by existing container structure and does not reduce the cargo carrying capacity of the container. When the twistlock of a hoisting spreader locks to the container to hoist it, the twistlock engages the UCLS actuating unit which in turn causes the UCLS locking unit to rotate to the unlocked position. The container can then be hoisted clear from its base as shown in Figure 2.3. When the spreader twistlock unlocks from the container the UCLS locking unit returns to it natural, fully locked position. When a conventional twistlock (SATL or FAT) engages the upper corner fitting of a UCLS equipped container, the UCLS locking unit remains in its fully locked position allowing conventional containers to be stacked on UCLS containers onboard ships and in container yards exactly as they would to any other container. Other common container securing equipment such as lashing rods, bridge fittings etc. do not interfere with UCLS components.
UCLS: safety and savings
Safety First; the UCLS solution will improve safety in maritime and rail container handling operations. Additionally, the trucking community will realize safer working conditions at marine and rail container terminals.
- No men aloft on ships to unlock twistlocks
- No falling twistlocks
- No maritime twistlock handlers in congested areas under gantry cranes
- No rail twistlock handlers exposed in rail yards or climbing up and down double stack cars
- No truck drivers leaving the safety of their trucks to lock/unlock chassis twistlocks
Savings attributable to the UCLS solutions are:
- Safety – reduced costs of twistlock and twistlock handling injuries
- Reduced manning
- Increased productivity – crane lifts per hour
- Loose gear replenishment
- Improved operational expense per container
Fitting 18 million containers, for a global implementation, requires a large, one time, upfront investment. So what are those savings, and how quickly can they be earned back?
The savings associated with reduced manning consists of the complete elimination of the twistlock handling on shore, i.e. under the crane, as well some of the twistlock handling at the ship. Heavy lift drivers for shifting cone bins in some environments are not considered here. We assumed to save 95% of 3 men per quay crane running hour. For a terminal of 1 million TEU, 6 quay cranes this amounts to approximately a saving of 50 - 55,000 man hours annually. In Table 1, we have listed the typical direct savings per container for a terminal of that size. Obviously, the higher the labour cost, the higher the possible savings.
Table 1: manhour cost vs. direct savings in OPEX per container
The payback period for the terminal’s share in the overall investment ranges from 7.7 years in a low cost environment (20 USD / man hour) to 1.5 years in a high cost environment (100 USD / man hour); which are both fully acceptable for the entire industry. The estimated average global labour rate of 50 USD / man hour suggests an average industry payback in the range of 3 years.
In addition to the direct savings, we could expect that for instance at a straddle carrier terminal, the quay crane productivity increases approximately 10% because UCLS containers convert indirect lifts (those lifts that must stop in mid-hoist for twistlock handling purposes) into direct lifts (those lifts that go directly from the quay to the ship and vice versa).. These savings will also be realized at terminals that load / discharge directly to street chassis. For terminals that only utilize bomb carts, the quay crane productivity would not increase substantially, as the impact on tractor-trailer cycle time is less than 1%. UCLS related savings attributable to increased productivity (direct lifts) is approximately 1 USD per lift when applied globally.
Safety related savings and loose gear replenishment costs are not considered here however the upside potential should be recognized.
UCLS: how to get it implemented world-wide
Worldwide, there are approximately 18 million containers. How can our industry implement the UCLS as it offers such profound impact in terms of handling costs, and operational safety?
Here we elaborate on one of the possibilities, departing from the idea that the key stakeholders are the terminal operators. As we showed in the previous section the cost reductions can make a difference of xxx per container handled. Probably more important, the number of injuries and LTIF will drop significantly, as one of the most dangerous jobs is eliminated from the process. As with all automation efforts, the reduction of jobs in a highly unionized environment will be a challenge however, given the potential improvement in safety for members unions should embrace the UCLS solution. Do we as society accept that we hang-on to old-fashioned, dangerous practices? Trains and ships also do not have a stoker to put coal in the steam engines? At that time, probably a big loss of jobs as well.
So, how can the joint terminal operators get this system implemented, overcoming the chicken and the egg problem. After all, the savings in cost and safety can only achieved when all containers are foreseen of the UCLS.
Let’s first look at upgrading the existing fleet of containers. Existing containers can be upgraded with UCLS components in approximately one hour in a workshop (could be the container repair shop, or the MT depot). New build containers can be manufactured today with UCLS linkage access holes in anticipation of a UCLS rollout which reduces container upgrade time by 50+%. Following UCLS implementation it is expected that installation of UCLS components will be fully incorporated into the new build process. A container visits approximately 18 times per year a marine container handling facility. Obvious locations are low cost ports where many containers are transshipped, such as Shanghai, Hong Kong, Singapore, Los Angeles/Long Beach. Shanghai sees approx. 13 million containers passing through, Singapore 8 million (here Singapore is further behind Shanghai due to the much higher transshipment ratio, which means that most containers are handled twice), and LA/LB approx. 7 million.
Besides introducing these dedicated locations, large repair shops could be supplied with the UCLS, so that every container passing there will also be equipped.
Of course, there will be containers that only move within a limited region, as they are owned by lines that are not global operators. For these containers, a more detailed strategy has to be developed.
Although UCLS equipped containers can be landed directly on the terminal surface (UCLS components and corner fittings have been compression tested and withstand the compressive force of 8 fully loaded containers when placed on a flat surface), it is anticipated that terminal operators will make use of Terminal Deck Sockets (TDS) to eliminate damage to the terminal surface.
Figure 3: 3 types of pads for storing UCLS equipped containers (type 1 – type 3 from left to right)
Type 1 TDS are flexible in that they can be put into position and picked up quickly. It is anticipated that Type 1 TDS will be used in early stages of a UCLS rollout or in areas of terminals that store containers on a temporary basis. Type 2 TDS are easily picked up and put down with lifts or other container handling equipment and have a means of semi-permanently securing them to the underlying terminal surface.
Type 3 TDS are more substantial, with additional support and “anchoring” qualities under the terminal surface. Type 3 TDS may allow high density terminals to more safely expand vertically if necessary. Long term, this would be the way forward when UCLS gets implemented.
The higher the stacking, the lesser TDS will be required for a certain volume.
Equipping the yard with TDS will be a considerable, one time exercise. However, as the following example indicates, investment in TDS is in the best interest of the terminal operator. Given the variety of TDS and the even greater variation of terminal operations and configurations it is challenging, within the scope of this article, to quantify the cost / reward of terminal deck sockets on a global scale. However an analysis at the terminal level can shed some light. An analysis of a straddle carrier terminal showed that the terminal recently handled approximately 1.3 million vessel lifts annually. The terminal has approximately 13,800 decked 20’ container slots. Given the estimated UCLS related savings at this terminal, the operator could expect savings per 20’ slot in the range of $3,000 annually. TDS are expected to last 20 years or more. Given that RTG/ASC environments generally have fewer grounded slots the savings per slot in those environment is expected to be slightly greater.
Of course, as the percentage of containers with will grow steadily, the installment of these pads can also be gradual, across 1 – 2 years. Additionally, today’s TOS can be used to code UCLS containers and plan them to be stacked on the second tier or higher. In a 1 over 3 straddle carrier environment the use of TDS could be postponed until the transition to UCLS containers is approximately 50% complete. In RTG/ASC environments, TDS can be added to terminal “bays” overtime as UCLS container become more and more common as demonstrated in Figure 4. The TDS are able to be used for containers without UCLS, so storage capacity should not be affected
Figure 4: Using the TOS to stack UCLS in designated areas, where the groundslots have been equipped with TDS
Figure 5: Impact of container grounding on pavement
A secondary advantage of TDS is that they can reduce damage to terminal surfaces and the associated costs of occasional resurfacing projects caused by conventional containers (see Figure 5). Applying TDS reduces pavement maintenance significantly, also improving the availability of yard space over time.
Furthermore, equipment upgrades for some hinterland transportation equipment (train wagons and truck chassis) will be necessary. Equipment that has fixed male chassis pins require upgrades to female ISO sockets. All upgraded equipment can handle conventional and UCLS containers during a transition period to the UCLS solution. Additionally, the rail community will realize UCLS related savings similar to the maritime community and the trucking community can likely realize indirect benefits beyond the scope of this article.
All in all, a large investment in infrastructure, but not significant compared to the cost of fitting 18 million containers with UCLS (approx. 5 billion USD).
Furthermore, logistically, we consider it achievable in a short period if it’s made a mandatory requirement by the top 10 of terminal operators (as others have to follow).
Business models for implementation
Another challenge to consider is how to equitably share investment and reward of UCLS related savings.
The general view of terminal operators is the UCLS solution will help operators achieve safety, productivity and economic goals. However, since the equipment (containers) belong to the shipping companies, they can do nothing until shipping companies drive implementation of the UCLS.
The general view of shipping companies is the UCLS solution will help lines achieve safety, productivity and economic goals. However, lines are generally of the opinion that terminal operators will retain all of the economic benefits.
To overcome the chicken and the egg dilemma, what is needed is open constructive dialogue between leading shipping companies and leading terminal operators dedicated to improving safety and efficiency in the container handling industry; potentially via conference and industry work groups.
Several high level models may be considered to spark discussion:
- Shipping lines drive implementation and demand reduced terminal handling charges (traditional)
- Terminal operators offer reduced terminal handling charges if shipping lines use UCLS upgraded containers (for example, discharge of 20’ standard containers = $200, discharge of a 20’ UCLS container = $185 if stowed so as to allow productivity savings) UCLS savings to be negotiated and distributed to shipping line and terminal operator individually)
- Terminal operators jointly invest in a mutual association, fund UCLS implementation and retain 100% of the ensuing savings.
- Terminal operators and shipping lines jointly invest in a mutual association dedicated to UCLS implementation. A per lift license fee is collected by said organization, savings are redistributed to investors (i.e. terminal operators / shipping lines).
In order to have a few pivotal terminals mount all the UCLS devices, they need to be paid by all the terminals world-wide, to share the benefits. For this we deem that an intermediary organization of united terminal operators (they would be the joint venture partners) raise the money needed. Every terminal would pay its share based on the waterside moves it performs. The terminals executing the retrofitting process, get paid from the jointly collected funds. Each terminal would need to raise approximately 10 USD per container handled over the quay (1 time). In addition, they would need to equip the yard with the required pads in some form. However, these costs are small compared to the contribution to the container retrofit.
Conclusion
The safety benefits of the UCLS solution are clear. Economic analysis suggests a managed, timely global UCLS implementation is achievable and an attractive investment for the container shipping community as a whole. To achieve the safety and economic benefits of the UCLS requires buy in and guidance from industry leading shipping companies and terminal operators. UCLS work groups at upcoming conferences and industry organization events should be created to spark discussion about funding approaches and implementation strategies for the mutual benefit of all industry stakeholders.
Share this
You May Also Like
These Related Stories
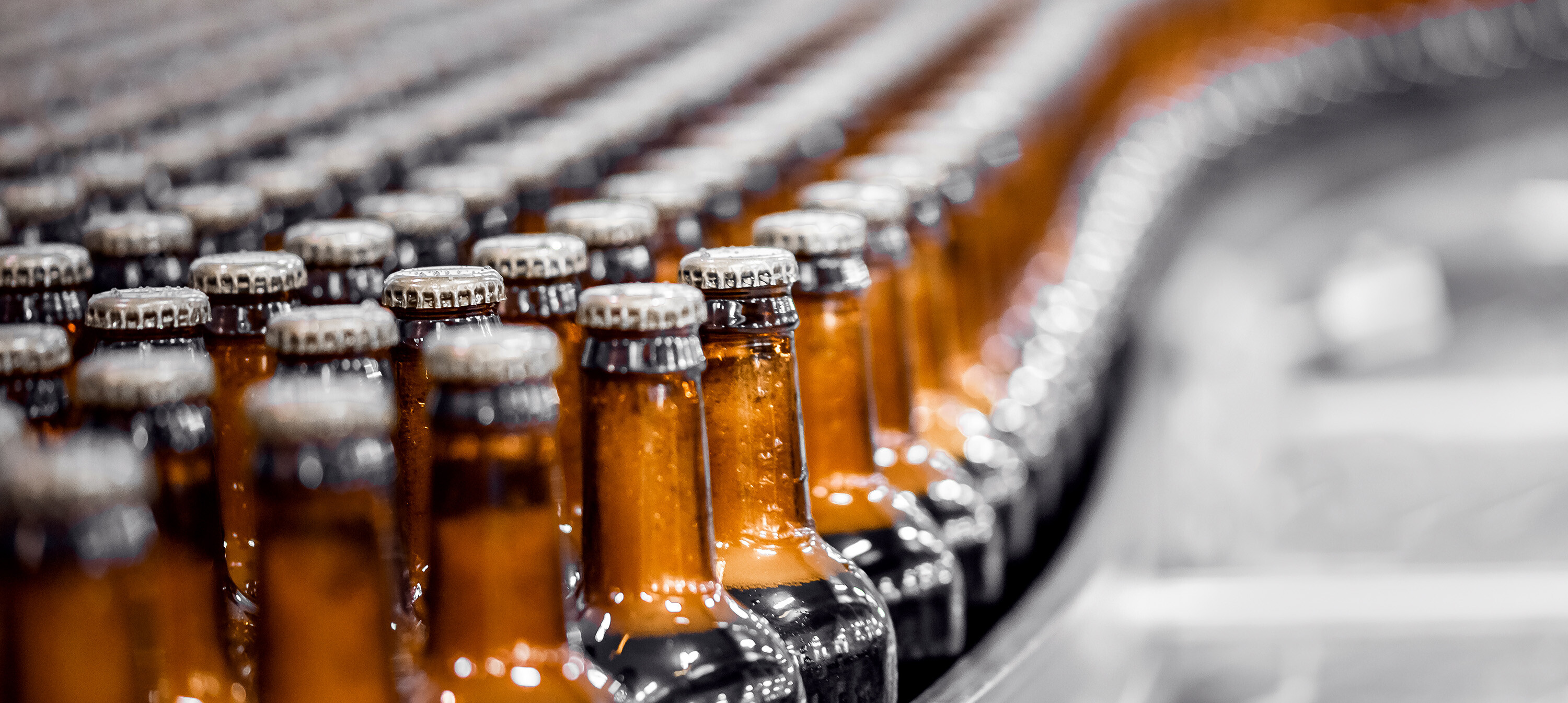
Successful roll-out of Autostore WMS update to address HMRC excise duty changes
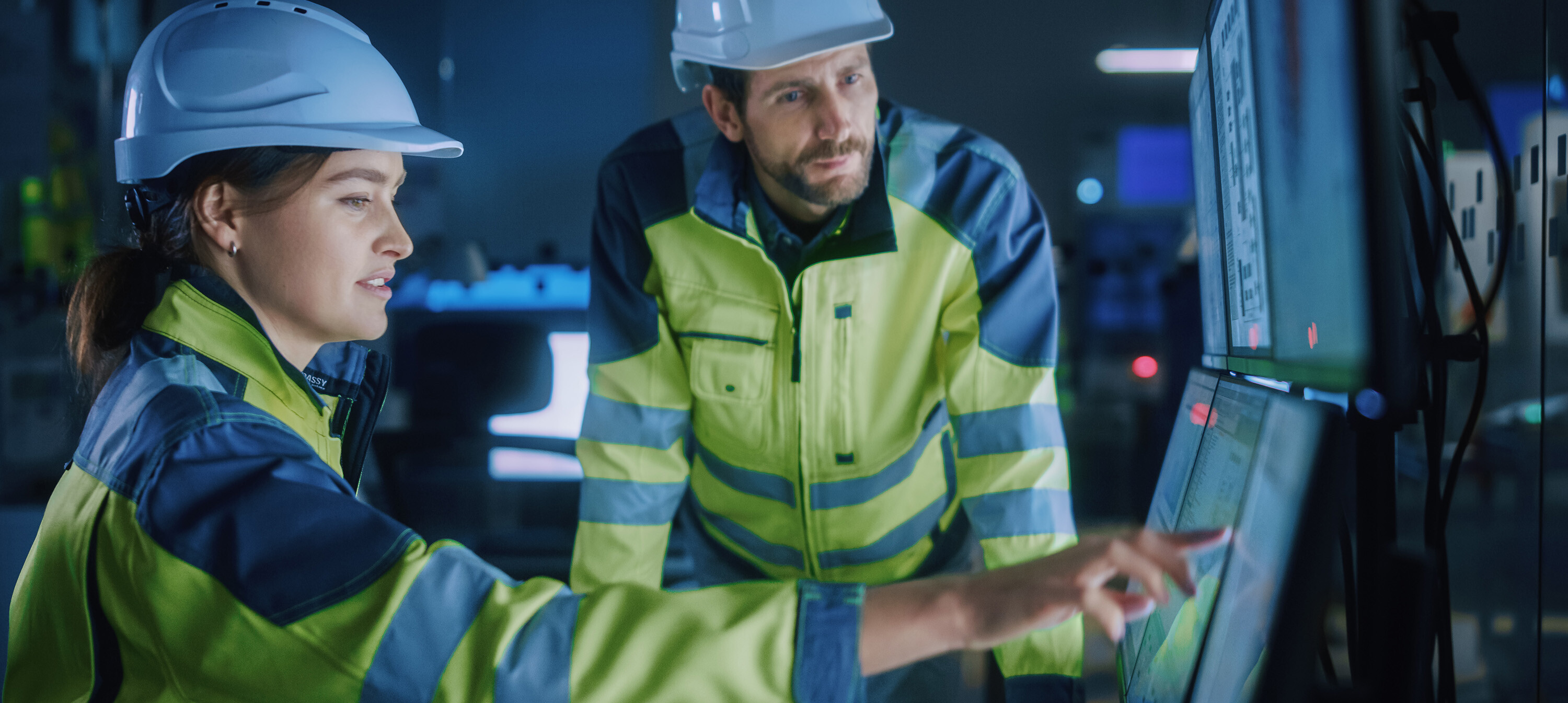
CommTrac shortlisted for prestigious IBJ Award
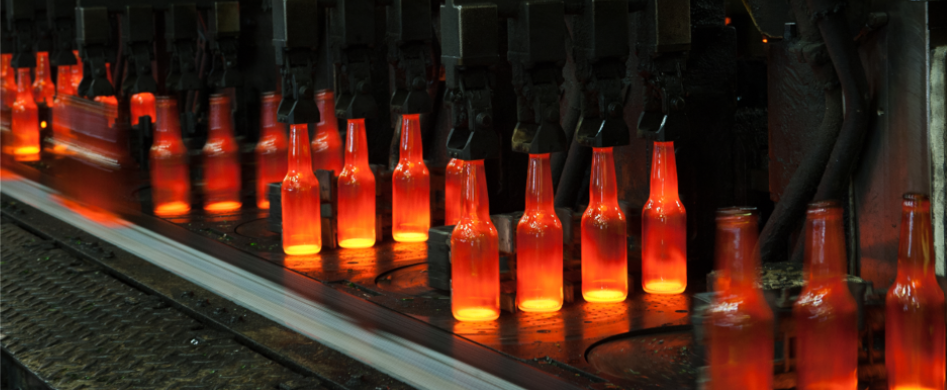