Using intelligent TOS plug-ins to increase terminal performance
As volumes have found their way up again, and additional terminal capacity is not easily realised, terminals return to seeking improvements in their internal processes. Based on our experience, which covers over 50 terminals where we assisted in performance improvement programs, it is possible to make substantial performance gains for internal processes. This is also recognised by the terminals themselves. A recent survey by Navis indicates that 76% of the respondents put process improvement as a ‘number one priority’ for terminal operations.
Process improvements may be seen through productivity increases, gains in service levels, for example, the reliability of port stay, capacity enhancement due to using space more effectively, and cost reductions. Without a doubt, double-digit improvements can be attained in the performance-cost index.
Performance improvement needs to be a data-driven process, which means that without in-depth knowledge of what is going on, any improvement measure is a wild guess. Lean Six Sigma theory, a methodology used to enhance productivity, provides a solid justification for such data-driven improvement, which implies extensive data collection for initial and continued performance measurement as improvements are implemented.
Luckily, terminals collect heaps of data through their TOSs, although this data is often quite underutilised. Turning data into information and information into knowledge regularly fails with the implementation of a Business Intelligence (BI) system, or with the focused use of the output of such a system. Terminals that structurally link past performance to an analysis of what went on, are still rare. Challenge yourself, dear Operations Director: how often is yesterday's performance analysed, and linked to the actual processes that occurred? How often is the planning beforehand analysed? So just implementing a BI system does not mean you are actually gaining knowledge, nor does it mean you are improving performance.
ROOM FOR IMPROVEMENT
In a time where Artificial Intelligence (AI) is moving from scientific magazines into our daily lives, one would expect a lot of it in container terminal operations. The nature of operations is repetitive, the data overwhelming, and the control tasks relatively simple. Well, reality is very different. Even the largest terminals in the world practise manual vessel planning, yard planning and equipment dispatching. Most control strategies are reactive, rather than proactive, and there is little being done to understand the patterns underlying the container trade. Terminal operators are relying heavily in the TOS for data storage and order management, but for terminal planning and control, they are relying on people. Even in the most-robotised terminals, there is still a high degree of manual control, going way beyond exception handling.
At the same time, there is a widely-spread understanding that these processes can be run more effectively, and even more so efficiently. The nature of these tasks is typically repetitive. At the same time, some of the tasks require quite some information to be executed efficiently. Two characteristics that make them quite suitable for automation.
In order to facilitate the automation of these repetitive tasks, we developed a toolkit to support terminals in this process. The toolkit consists of 3 main components:
- Analysis of what’s going on through detailed KPI analysis, using standardised tools linking into the TOS
- A set of automation tools (we call them intelligent apps or plug-ins), building on-top of existing TOS’s to automate and optimise today’s processes.
- An implementation approach to ensure the integration of these new tools into the operational organisation.
KPI measurement
What KPI’s should be monitored and on which basis? What does a weekly average STS productivity tell you? Barely anything! KPI measurement should reflect the effect of decisions taken. Such decisions range from the amount of equipment deployed, the locations in the yard used for stacking, the sequence of containers to be loaded, and many more. The level of detail here also means that the KPI’s need to be at micro level, which means disaggregation into individual hours or even less. We need to know how long prime movers are waiting for the yard crane to be served, while loading, and while discharging. Same at the STS. Often, this level of information is not available to the decision-makers, even not in real-time. KPI’s are aggregated, which make it hard to assess the quality of planning, dispatching, or equipment deployment strategies; those decision that eventually make or break the cost-efficiency of operations.
Intelligent plug-ins
In order not to require terminals to change their current TOS, the Intelligent plug-ins link into the TOS without any change to the TOS itself. They retrieve information, and push back actions, or updated information, merely in the background. Meanwhile, a number of these plug-ins are operation.
In this article, we would like to discuss several of the intelligent plug-ins. We also discuss how they are tested by means of emulation, to ensure their contribution to performance, and validity in live operations. After all, they are aimed at performance enhancement. The plug-ins that we will discuss here are the following:
- Yard Crane Scheduling
- Plan Verification
- Chimney stack detection and avoidance
Currently, the set of Plug-ins are only available for the TOS suite from NAVIS (SPARCS 3.7 or N4 2.x / 3.x). However, in principle they are built in a TOS agnostic way, allowing integration with other TOS’s as well.
Yard Crane Scheduling
One of the most under-utilised pieces of equipment in terminals is the RTG. Where 70% of terminals world-wide work with RTG’s, the real productivity typically hovers between 6 and 10 moves per hour. This implies idleness in the range of 40 – 60%. The root cause can be found in the merely static way they are deployed across the terminal: the machines are positioned in a yard block, and handle the moves that actually are occurring in these blocks. Without going into the potential of improving this by more dynamic yard strategies (see De Waal and Saanen, PTI31 and 32), the impact of dispatching the yard cranes in a more dynamic way can be huge. A recent deployment in a large RTG terminal showed very quickly an increase in RTG productivity by 10-15%. If we monetize this, cost saving is obvious. Assume an RTG is running 4,000 hours per year, costing some 60 US$ per running hour (labour (20$)+ fuel (20$) + maintenance (20$)), we are saving per RTG at least 24,000 US$ per year. A terminal handling 1M TEU easily has 20 RTG (or more), already generating a saving of close to 500K US$ per year. If we project this to a US Westcoast scenario, where the cost per RTG running hours are more like 200US$ per hour (due to the manning per RTG), the savings increase to 80,000 US$ per year per RTG.
Plan Verification
TBA's Plan Verification Tool brings unproductive moves to attention of the planner early on.
Planning might be the most undervalued activity at container terminals, at least when we assess how the quality of planning is measured and evaluated: in principle not at all. There is very little feedback to the planner, how the plan played out in live operations, not allowing the planner to learn in any way. For this purpose, we developed the plan verification tool, basically analysing the plan, identifying errors, and opportunities for efficiency improvement. Errors range from loading to occupied cells on-board, to wrong working patterns (e.g. discharging starting at the waterside of the vessel), to stacking 40’ containers onto 20’. Efficiency improvement is recognized for instance by missed twinning opportunities, optimised loading sequences (minimizing rehandling) to avoiding peaks inside the yard.
The tool runs quickly after the plan has been finalized, and then allows for fixing errors and utilizing the improvement potential.
Chimney stacks
Chimney stacks are an inevitable evil inside the container yard. However, by clever stacking strategies they can be minimised. As such improving safety, and avoiding containers to be blown in case of windy conditions.
TBA's Chimney app is used to prevent undesired situations, such as the above, from occuring in the yard.
The Chimney App avoiding chimney stacks to be guilt (affecting the grounding decision in real-time) and allows remaining chimneys (as a result of load out, stacks can be leftover) to be re-organised to remove the chimneys.
Applications or plug-ins may address terminals’ wish to improve cost-efficiency and performance. When implemented well, the tools provide a ROI within a few months, and increase a terminal’s competitiveness.
Share this
You May Also Like
These Related Stories
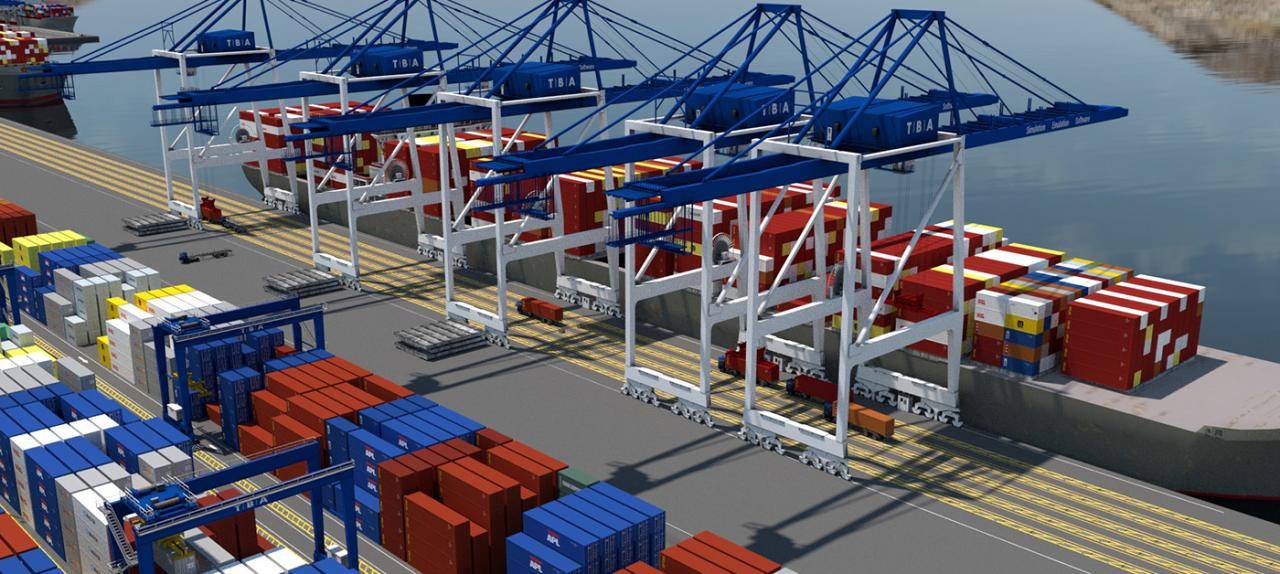
Using emulation to improve the performance of your TOS
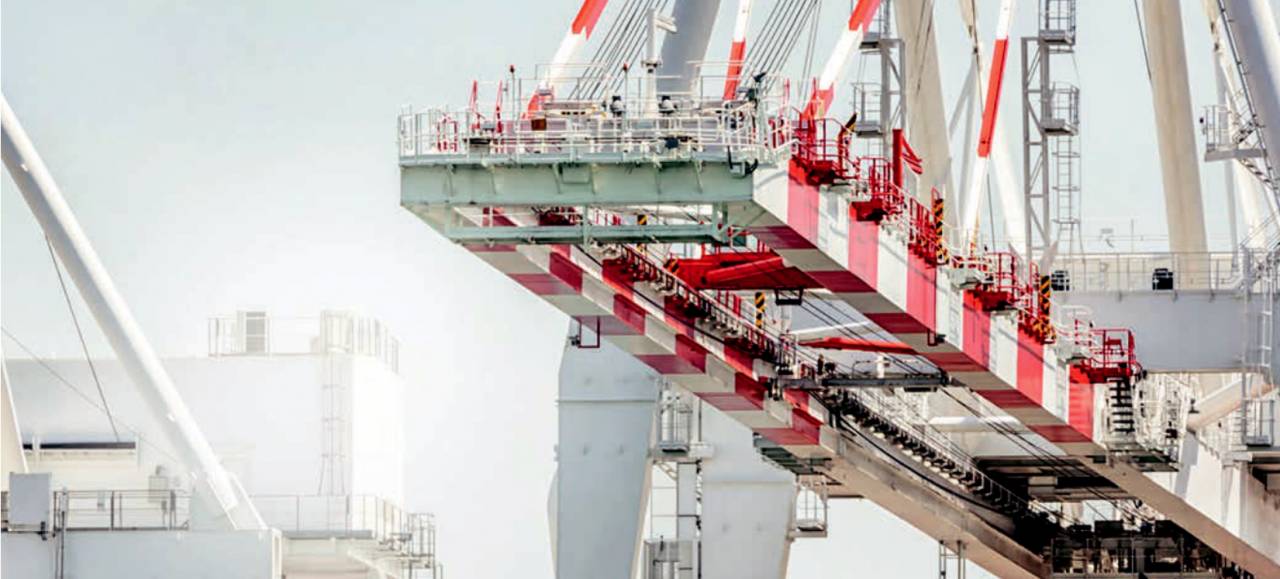
20 years of high-definition simulation in the port industry
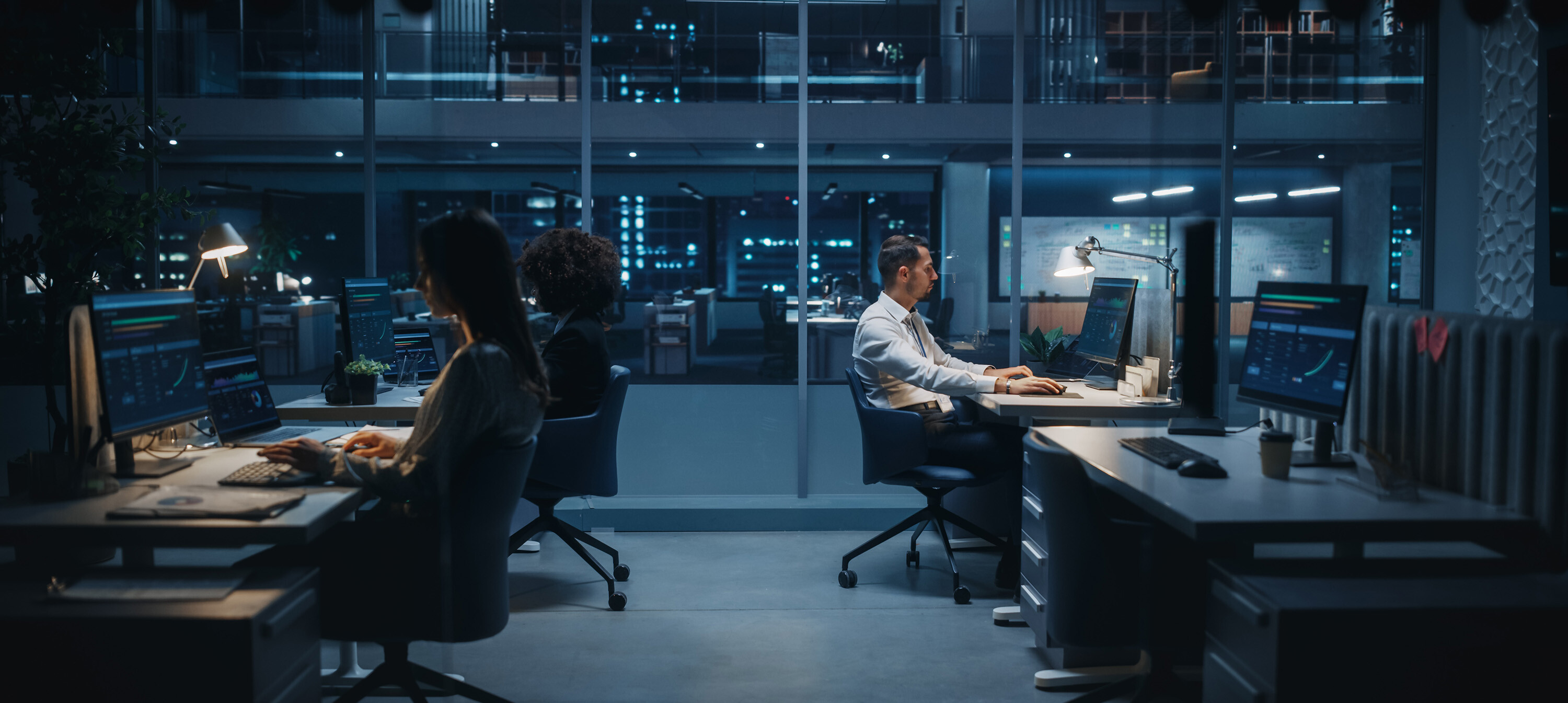