Technologies providing value to make ports and terminals more effective, efficient, and safe
Some say the technological revolution is going ever-faster. Although we have to realize that in the last 100 years, the amount of technological innovations has been enormous, we have to maintain a helicopter view on the world. In recent years, we have seen the latest hypes follow each other quite rapidly, with the Internet of Things (IoT), big data, blockchain, and artificial intelligence (AI) as buzzwords. The latest addition to this grouping is ‘the digital twin’. Although all of these technologies seem to offer great opportunities to the industry, and certainly to the logistics industry, the amount of clear success stories or largescale implementations is lacking. Some may point to the conservatism in the logistics business, but others may also question the true business case of these technologies.
Moreover, some of these hypes are repetitions from the past, the digital twin not in the least. After all, a digital twin is a model of the physical reality, albeit with a great level of detail. But it will always remain a model, leaving away irrelevant details.
What is clear from each of these trends is that technology has become an enabler in developing innovative, value adding solutions that actually address reallife problems. The technology is readily available, affordable, and delivered in mass-production. There are many suppliers who can also assist in deploying these technologies. Does this mean we are not facing any challenges anymore? On the contrary, to make use of them such that they actually serve the objectives of ports and terminals, there is a lot of work ahead of us.
In this paper, I have tried to identify where these technologies can provide value to make ports and terminals more effective, efficient, and safe.
1. CONNECTED TO THE OUTER WORLD
Terminals are a key component of the supply chain. One would expect that all information that is sent to terminals, is delivered in standardized digital formats. Reality is far from that. Timely data availability, data quality, and digitization are all problematic, leading to large inefficiencies in terminal operations, affecting the service that terminals provide. Such errors range from BAPLIE files, to inaccurate vessel ETA’s, to changing modes of transportation after arrival at the terminal, to random truck arrivals at the gate.
This is in a world where all the necessary information is available in digital form. However, such information is not made available to all stakeholders in the supply chain. In many ports around the world, initiatives are taken to make the information accessible to all parties, however it takes great effort, as there is resistance with certain stakeholders, as their position may be weakened or even disappear if information freely flows. It is our expectation though that it will be just a matter of time.
2. CONNECTED TO ALL ASSETS
Terminals are a collection of highvalue assets, yet the real-time available information about the assets (location, status, technical state, et cetera) is not readily available to enable intelligent control. Control for asset deployment, but also for maintenance purposes. In most cases, there is already information locally available, but not centrally, and certainly not across the entire fleet, in one fleet management system, or in the TOS. It is scattered, has no standard structure, and is often incorrect.
The technology to enable this is there, and a large portion of equipment is already available, including sensors of various kinds, location devices, and machinebound PLC’s. However, this all comes with a limited degree of standardisation. Further, basic mechanisms such as remote updating, version management, and health checking is rarely present.
Besides this, the maintenance of all the on-board technology is typically a problem. Regular calibration of sensors (e.g. weighing sensors) is required to make sure the information coming from the machine is accurate and reliable. Yet, this is not yet standard (maintenance) practice because the actual use of the information is limited, defying the purpose of proper maintenance.
3. CONNECTED TO ALL STAFF
As important as connectivity to the physical assets is connectivity to the human assets in the field, as well as real-time access of operators to central information. Both to ensure people are kept out of harm’s way (think of location detection, or proximity sensors), as well as information in real-time to perform actions efficiently (updated loading list, reefer (un)plugging list, etcetera) is rarely installed. Instead people are sent around with information on paper, and record information on paper to be processed later. This in a time when almost everything can be accessed through smartphones.
Here, we could even think one step further into augmented reality (eventually through technology like the Google Glass), so that operators get immediate visual information while keeping their hands free. One could for instance think of twistlock information: should the container in the spreader be equipped with cones or not?
4. REAL-TIME, HOLISTIC PLANNING, CONTROL AND OPTIMIZATION
A terminal consists of a series of interlinked, highly variable processes, hence dynamic, real-time planning and control is essential to be efficient. There are all kind of planning, scheduling and dispatching tools in the market to assist and provide decision-making support, or even automation. But there is great resistance – especially from operators – to use these tools. On the one hand there is a degree of job protection behind this, but also lack of insight in the benefits. The efficiency gain does not come from some reductions in planning and dispatching staff, but by operating in a better way outside. Here the real expense is being spent in machines, fuel and labour.
5. REAL-TIME MEASURING OF KPI’S
In order to improve, one needs to know what’s going on. Hence, the performance of the operation should be measured continuously, and to a great level of detail. Only then, can one really determine what explains the peaks and troughs of performance. Simply measuring STS productivity, for instance, does not provide sufficient insight. Also, the circumstances affecting the performance must be gathered so that a complete picture results. Factors such as yard occupancy, gate volume, driving distances, and the number of unproductive moves should be monitored.
The measurement should preferably take place in an automated way. Therefore, not MS-Excel spreadsheets filled in during or after the operation, but gathering at the source. The key questions are: What are the assets doing, how fast are they moving, how far are they driving? Finally, all information related to operational disturbances needs to be gathered, as this is the third explaining factor for performance.
6. CONTINUOUS ANALYSIS OF PERFORMANCE (KPI’S)
When all this measurement is in order, there is a solid basis for analysis, and, most vitally, acting upon said analysis. Just gathering data serves no purpose. The data needs to be turned into insight, and insight into knowledge, so that the actual control improves. Equipment deployment, yard strategy and vessel planning are key ‘customers’ of proper operational analysis.
This means that the lessons learned need to be fed back to the staff planning and controlling the operation. This will have substantial effect on the variable cost. The cycle of measuring, analysis, and action should always be continuous so that the learning cycle also reacts to changes. Changes in volume, dwell times, truck patterns, or just the arrival of a new vessel service are likely to require adjusting operational strategies.
In this process, it is also key to make record of implemented changes. Most changes in strategy will only have effect over a longer period of time (typically more weeks than days). At the same time, there will be cyclic, independent influencing factors such as the seasonal patterns. These effects must be taken into account when analysing the result of change.
7. TRAINING AND CERTIFICATION OF STAFF
In prior articles in The Journal of Ports and Terminals, we have written about the importance of training. We have seen very significant effects in improved planning capabilities after training. Having a serious training programme, first for on-boarding, and later to further enhance operating skills is a key factor in operational performance.
Where most operators are having or setting up training programmes, certification of the control room staff is still rare. Which is surprising given the large impact this staff has on operational success. Our findings across more than 25 terminals (>250 planners) show the difference between worst and best planners by up to 50% (measured in resulting berth productivity).
Testing planners against a calibrated scenario – for instance, in a near-to-live virtual terminal (see REF) – is one possible way to get people in the right position.
8. CAPABILITY TO LEARN FROM THE PAST
One of the hype words often mentioned is artificial intelligence. Fundamentally, the ideas behind it are really new, but the combination of large amounts of data being available, and cheap (cloud-based) computing power, brings the ability to quickly recognize patters, rendering it much more useful. Still, computers have a tough time recognising context in data, but with help of experienced operational analysists, this gap can be bridged.
The potential is large, as the container supply chain is highly repetitive, hence predictable. Where today, the terminal has almost zero information to use to allocate the right spot in the yard, learning about dwell time patterns, pick-up patterns, and roll-over patterns, may reduce the amount of unproductive moves by factors. Many terminals move a container more than four times, where an ‘ideal’ operation would do it with just two moves. One can imagine how many cost savings would be achieved.
9. TERMINAL DEVELOPMENT BASED ON ‘MASTER PLAN’
When we look at how terminals have come about, we recognize many look like patchwork. Every expansion is planned when required, without looking at the bigger picture. Buildings in the most inconvenient places, height differences, light poles, roads with illogical routing and so forth, are quite common situations.
Of course, not everything can be taken into account, but we can go significantly further in looking ahead and making a robust masterplan, that withstands a change of circumstances to a large extent. Cargo flows, ship sizes, hinterland transportation patters, and dwell times are all subject to change, yet these can be addressed during the master planning. This means expansions become consecutive steps of the execution of a grand plan, rather than the isolated exercises typically leading to unwanted situations.
Modelling can greatly help in these assessments, and also act as a source of reference for future decision-making. Even the consequences of changing parameters can be easily analysed and quantified (see
REF).
10. A SOLID CYBERSECURITY LAYER IN PLACE
Last but not least, a terminal today needs to have its cybersecurity in order. There is a large degree of data exchange with many third parties. Such a scenario means the risk of receiving malware, viruses or alike, or spreading it to others, is quite large. Besides, the fact that containers contain high-value goods makes them a highly desirable target for cybercriminals. Finding the right container, filled with expensive electronics or cigarettes, by hacking in the system, and setting up an illegal delivery, is not a hypothetical scenario.
This means that cyber security must be part of the daily IT process. Making sure that all protection layers are up-to-date, and making sure that staff is aware of the risks. As people are always the weakest link, continuous back-ups are essential, so that recovery in case of an attack is quickly feasible.
CONCLUSION
A quick inventory we undertook at a range of terminals in two months in late 2018 revealed that from the ten prerequisites above, most terminals have not fulfilled most of the ten, and if they have they are to a limited extent. These are results in a time where the technology to help is available. None of the points mentioned will require large investments, nor be too complex to implement. However, it requires ability and willingness to change. In many cases, this only arises when there is a serious problem (for instance after a cyberattack causing substantial damage, people are willing to implement strict security procedures), or pressure from the outside (e.g. from local authorities) to implement these productivity, and efficiency enhancing measures.
So, in closing, we still have a long way to go.
Find the technical paper "10 Pre-requisites for smart terminals " - published in PTI magazine edition 81 - here
Share this
You May Also Like
These Related Stories
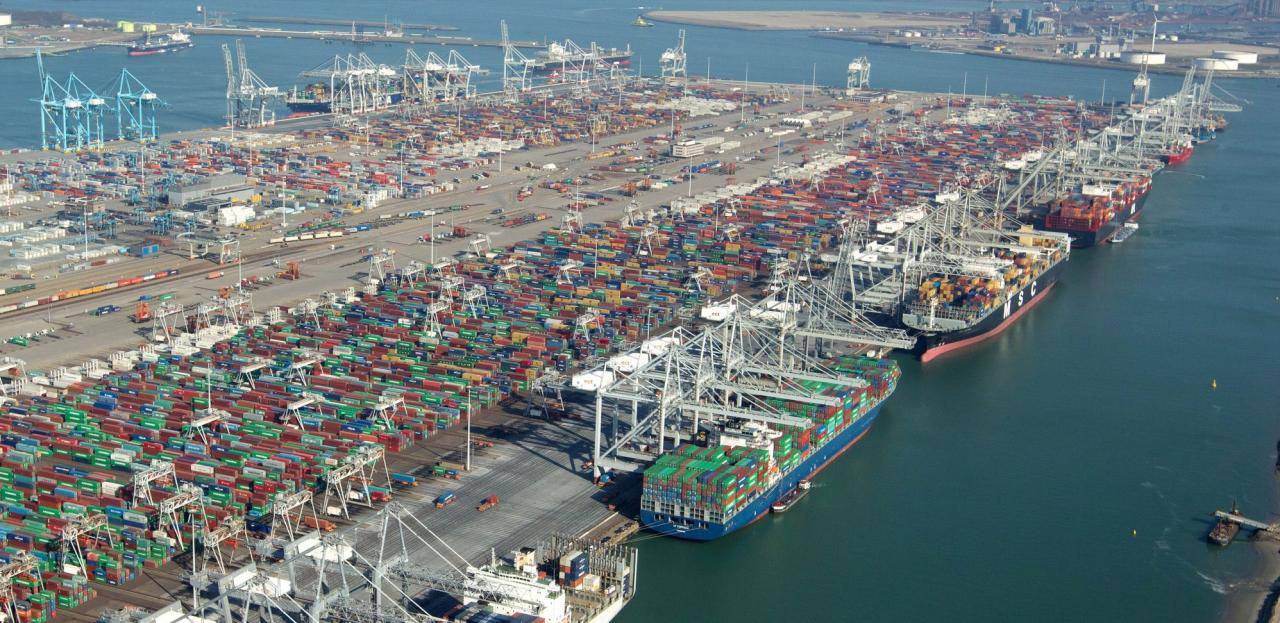
Applying new technologies in an existing automated terminal
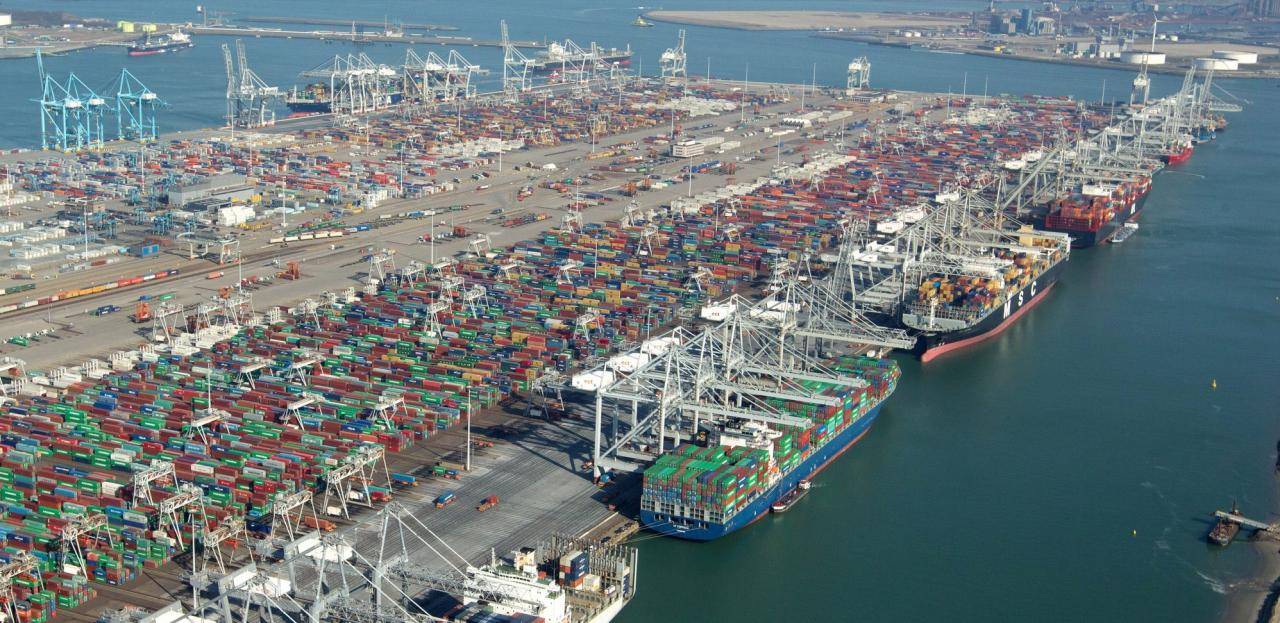
Lean and mean terminal design benefits from advanced modelling
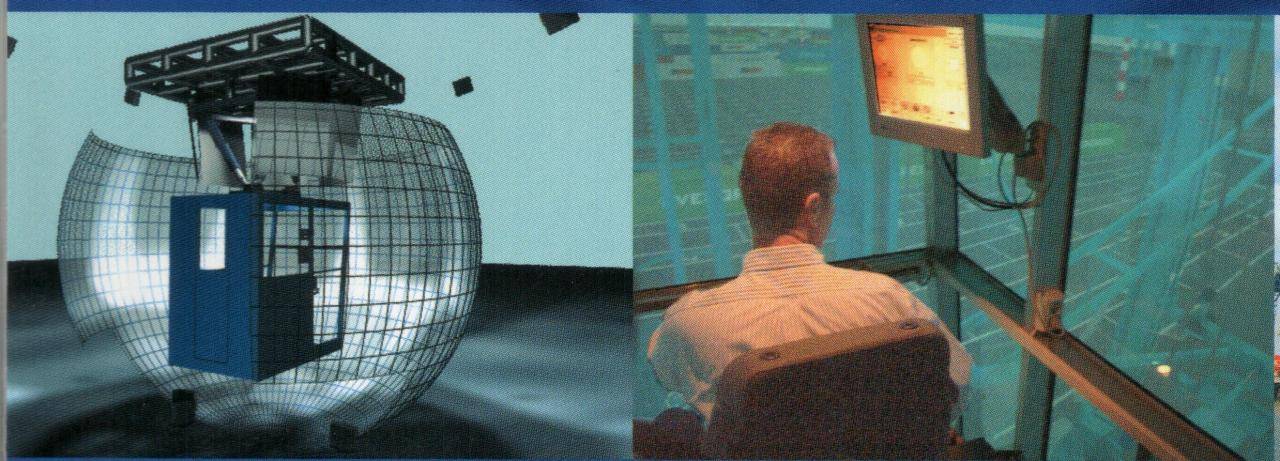