Lean and mean terminal design benefits from advanced modelling
Introduction
As container volumes keep growing, as vessels and their call sizes are rapidly increasing, as land is getting scarcer, and as wages are rising, terminals are confronted with more challenging questions how to keep up with their competitors. In order to accommodate this growth, there are many terminals extensions and new terminals at the drawing boards or under construction.
Terminal design triggers questions concerning the layout, the attainable quay crane productivity, the yard operating strategy, the terminal operating system, and the equipment. One of the main questions is how to reduce the operating cost. In this article, we shall enlighten the potential of a simulation approach, we follow when answering these and many more questions with regard to terminal design, extension and improvement.
With this article we intend to show, how the cost, risk and performance of a new terminal design, terminal extension, or an existing terminal can be improved in an efficient way. We will illustrate our approach with a couple of real-life examples. But first, we will introduce simulation.
Simulation
Although simulation is increasingly used at container terminals, it is not as common as for example in the automotive industry, no investment above hundred fifty thousand euro is made without thorough prove by means of simulation. This is not strange at all when knowing that for every euro spent on simulation, ten are saved.
But what exactly is simulation? The essence of simulation is to make a model of the (future) reality within the scope of the objectives. With this model all kind of experiments can be performed. Usually, simulation is used to assess the effect of different alternatives, for instance an operation with straddle carriers versus an operation with RTGs and trucks. However, as we will discuss further on, simulation can be applied for many more uses.
In general, a simulation project exists of four steps:
- Specification and development of the model
- Validation of the model
- Experimentation with the model
- Analysis of the results.
By means of the animation, which visualizes the behaviour of the system, people involved are able to validate the working of the system.
The development of a new container terminal and the redesign of existing ones
Which lay-out, what kind of equipment and how many of that equipment do I have to purchase in order to have low costs per move, an acceptable investment level, and competitive performance? These are the main questions for the development team of a new container terminal. In the decision making process around these questions, simulation can play a supportive role with regard to the following aspects:
- Determine the dimensions of the terminal (e.g. quay length, stack size).
- Determine the type of handling system (equipment + operation + layout).
- Design of the terminal operating system (TOS).
The first step is to determine the main dimensions of the terminal. Here we apply an outside-in approach, taking the container flows that go through the terminal (vessel arrival pattern, rail pattern, truck pattern, dwell time) as starting point. Under these external conditions, the main dimensions are varied. This means that we analyze the service level (vessel service time, gross berth productivities, and crane density on vessels) under varying terminal configurations (quay length, number of quay cranes, gross quay crane productivity). Typically, per configuration, one year of operation is simulated, creating a picture of the service over the year. During the year, the variation in the stack (seasonal effects, peaks during the peak and even hourly peaks due to large discharge calls), the variation in berth occupancy (due to vessel delays, and variation in the call size), and the occupation of quay cranes can be observed, giving a rich picture of the service the terminal provide. As important input for the next step (determination of the handling system), the model creates a picture of the peaks in handling (waterside, but also rail side and truck side). These peaks are important to determine how much equipment is required to supply the quay cranes with enough boxes during these peak circumstances. Based on the outcome, decisions can be made concerning the quay length, the number of quay cranes, the gross productivity that quay have to achieve to accommodate a certain terminal throughput, the requirements for storage capacity, and the peak handling conditions.
Figure 1: Screenshot from the simulation model to determine the key terminal parameters
The second step is more comprehensive, in the sense that there are many variables involved. The design of the handling system determines layout, type of equipment for the various operations – think of the number of trucks and RTGs, the number of rail cranes, the number of gate lanes, and so forth, and the logistical concept (including for instance yard operating strategies). The latter is gaining importance in the case of automated terminal, since many tasks are taken over by computers or robots. But also at manually operated terminal, the emphasis is put on efficient operations – for instance the implementation of truck or straddle carrier pooling. In close relation (as mentioned in step three), the TOS should be considered, as only a TOS that has been configured for a specific operation will create a performing operation.
An example of this is a recent comparison we carried out between manual driven shuttle carriers (SHC), automated shuttle carriers (ALV) and Lift-AGV’s (as currently running at the 2 new terminals at Maasvlakte 2, Rotterdam). All in combination with an automated high density yard, operated by ARMGs. In terms of productivity, all three systems achieved the same performance level (40 net bx/h), but with different equipment numbers. In a peak operation the ratio between SHC, ALV, and L-AGV was 2.5 – 3.5 – 4 (per QC). The automated equipment is more sensitive to the density of the operation in terms of operating speed. Subsequently, one needs to compare the CAPEX required for each system, as well as the OPEX.
These questions are relevant not only with the development of a new terminal, but also when extending an existing terminal or changing the handling system or layout. Many terminal, for instance, are reconsidering their yard handling system to increase the stack density and therefore increase the throughput capacity of the terminal.
As shipping lines are requesting higher service levels, terminal systems need to be designed striving for various – mostly contra dictionary – objectives. Quay crane productivity has to go up, stack density has to increase, operating costs have to go down, and the landside service has to be improved. In order to create handling systems that comply with those requirements, the use of a simulation approach can be beneficial to separate good from bad solutions, to prioritise improvement measures, as not all features can always be implemented, and – last but not least – create a relatively inexpensive and safe trial and error environment for both prototyping and testing new solutions for hardware and software.
But not only for test purposes, simulation is useful; it also separates feasible solutions for not feasible ones; it assesses the contribution of solutions to the overall goals, always putting the entire system performance – rather than the individual performance of components – as key indicator. Moreover, it provides an environment where one can evaluate under varying, but manageable, conditions, e.g. busy and quiet operations, break-downs, and so forth. In the end, this will result in less start-up problems, solutions that are better thought through, increased software robustness, all leading to a reduction of risk.
Figure 2: Simulation model of new facility at Maasvlakte 2
The key to support these decisions by means of simulation is to model the equipment and operational procedures at a rather detailed level. Many attempts fail to link with reality, because the details that make an operation complicated – for instance the container loading sequence, the grounding rules, and the equipment assignment rules – are left away. We adhere an approach where those aspects are considered, so that the results from the simulation are close to the operational data. Essential here is a close cooperation between modelling team and terminal operator to arrive at a valid model.
The output of these kinds of models typically consists of:
- Productivity numbers of all the equipment (QC, RTG, and so on).
- Service times (e.g. of hauliers and trains).
- Occupancy rates of equipment, but also from the stack.
- Operating hours of equipment.
Optimise the day to day operation
Every day’s operation is different from that of the day before. Still, it is worthwhile to explore the possibilities to use models to improve day to day operations. With the models getting more comprehensive, able to capture real operational procedures, able to handle real operational data, able to depict process at the level of individual container moves around the terminal, and able to represent decision-making around grounding containers based on the container’s profile, we see a great opportunity to apply these models in the analysis and replay of past operations and in the pre-planning of upcoming operations.
- Questions around the manning and equipment usage given a certain operation at quay, rail and gate could be answered.
- Decisions concerning the in-advance preparation of the yard – so-called housekeeping – could be assessed on cost and contribution to productivity.
- Changes regarding operational procedures, such as equipment pooling, sharing part of the equipment, real-time re-allocation of equipment, and sizing the gangs could be quantified.
- Strategies and patterns of strategies for yard operations can be defined, assessed, and tweaked, in order to increase yard density, and reduce travel distance and false moves (shuffles).
The outcome of these analyses can be fed back into the TOS, and into the minds of the managers, planners, dispatchers, and operators, running the terminal. It can overcome the often contra dictionary perceptions about the bottlenecks in the current operation, and prioritize improvement measures. By using real data, and using real, past, operations, the value of these exercises heavily increases, because it becomes much easier to translate the result back into the consequences for coming operations. Examples of recent findings comprise the effect of equipment pooling (15% increase of equipment productivity and therefore a potential of reducing operating cost), and the effect of an improved RTG assignment and yard grounding strategy (20% less equipment required on average with a productivity level remaining at the same level).
The essence of arriving at models that can accomplish this added value is a good understanding of the operation, including the rules in the terminal operating system. An alternative to overcome cumbersome modelling of TOS functionality is to link the simulation environment directly to the TOS. In this set-up, the simulation represents all the physical processes, the TOS uses the real container data to control the operation. By doing so, the TOS can be configured much faster to accomplish a smooth and performing operation under various conditions.
Concluding remarks
Operations at container terminals are highly complex. Automation makes them even more complex. Optimisation tools treating the operation as a deterministic process are difficult to apply because in real-time the operation differs highly from the planned situation. Therefore, tools that explicitly consider the dynamics of a life operation should be favoured over others. Simulation is such a tool, able to represent and visualise container terminal operations – both the physical processes and the rules in the terminal operating system.
Applying simulation makes the decisions concerning the investment in quay and quay cranes, the choice of handling system, and the configuration of a terminal’s control system better founded, better to understand, and more transparent to follow. Summarising it enable a terminal operator to reduce the risk of the development of a new terminal and the improvement of an existing one. If simulation is applied, one should make sure that the specific characteristics of an operation are validly represented in the model. Otherwise, the risk of nice pictures over sound results lies just around the corner.
This article has been published in Terminal Operator in June 2015.
Share this
You May Also Like
These Related Stories
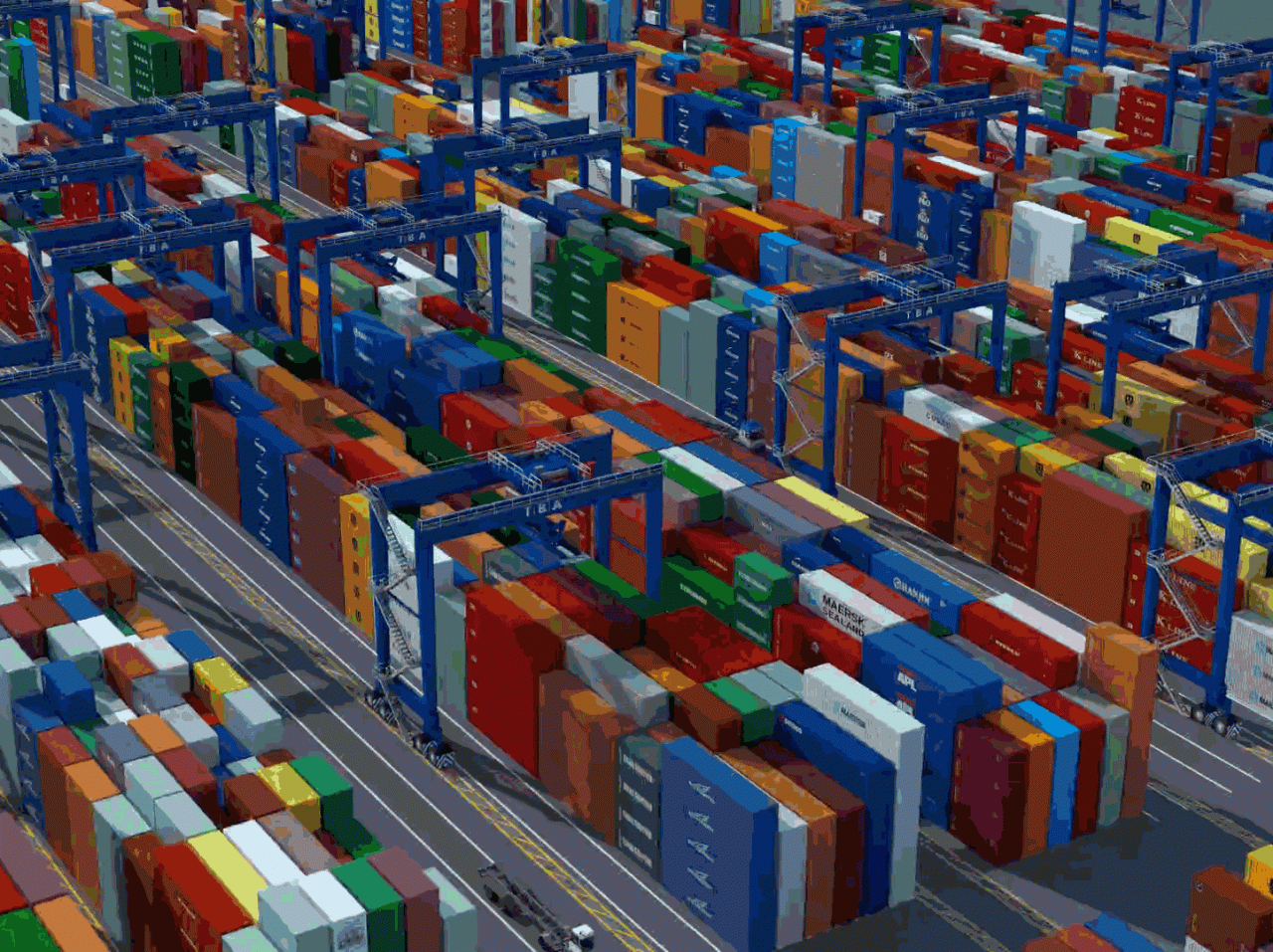
Optimisation as mantra for operational excellence
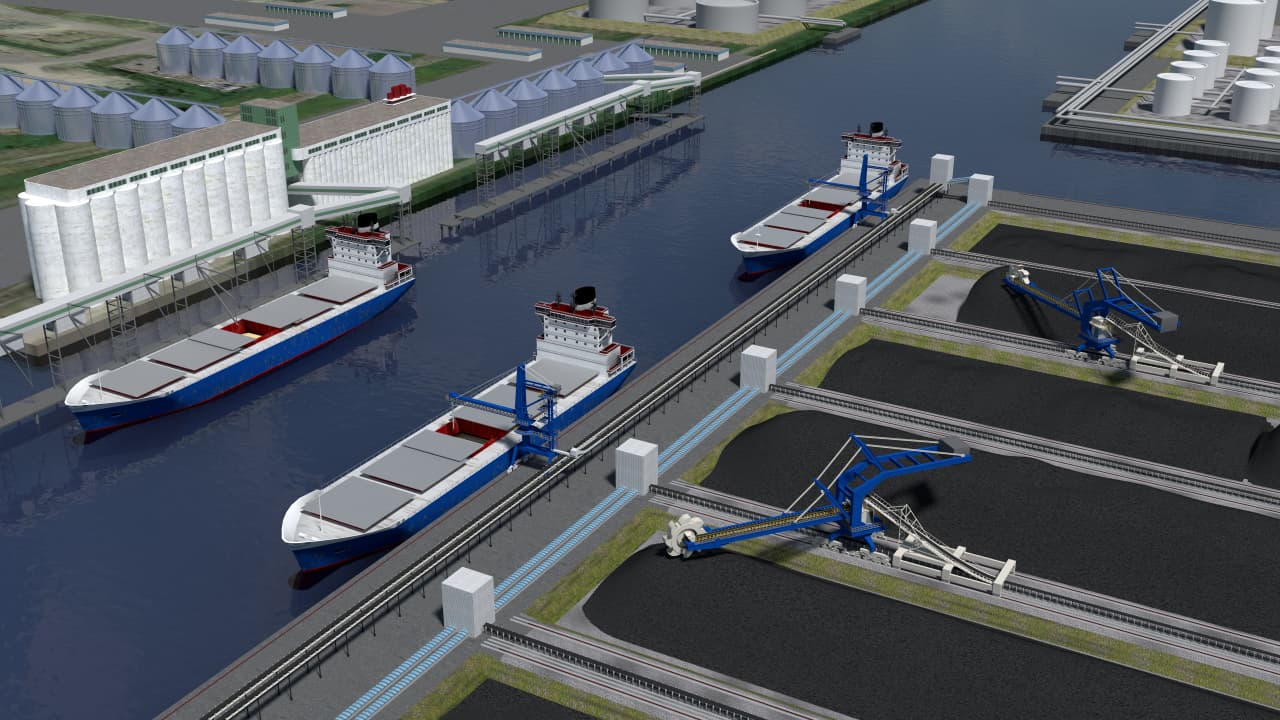
Making the transition to digital
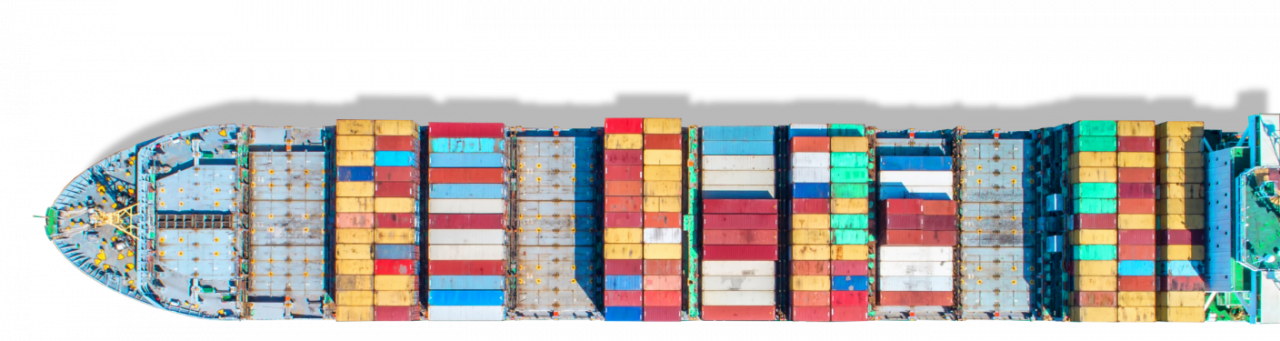