AGV Versus Lift AGV Versus ALV: A qualitative and quantative comparison
It is a recurring question in the planning of automated terminals: what is the ‘best’ mode of horizontal transportation? For many, horizontal transportation is seen as one of the most complex components of terminal robotisation, and this is right in my view. The horizontal transportation system connects two (more expensive) pieces of equipment (the stacking system and the quay cranes), and therefore always fulfils the role as a buffer. Furthermore, it consists of many vehicles which are dynamically interacting in a space that is kept as tight as possible. After all, apron space is expensive real estate. The question we aim to answer in this article is:
What is the most cost effective automated transportation system, with the today available technology?
Before we do that, we need to discuss the accusation of a possible professional bias we at TBA may have. It is true that since the late nineties, we have carried out many studies with the emphasis on automated guided vehicles (AGVs) of various kinds. This work led to the implementation of the Lift-AGV at the new terminals in Rotterdam. In those studies, however, it was always the Automated Lift Vehicle (ALV) – also addressed as the automated shuttle carrier, or automated sprinter - was part of the comparison. The information with regard to the AGVs mostly came from former Gottwald, nowadays Terex Port Solutions (TPS), whereas most information with regard to the ALV came from Kalmar (Cargotec).
The analyses were based on detailed time and motion studies of existing automated systems, for instance at CTA (Hamburg), and later at Patrick’s in Brisbane and Euromax in Rotterdam. In the study carried out for APMT Maasvlakte 2, an extensive peer review and validation of our simulation work has been done by an expert third party. This validation study did not reveal any irregularities or bias towards any of the systems.
Finally, during the implementation process of the terminals in Rotterdam, a performance comparison between the real AGV system and the simulation was carried out. This test – highly recommendable by the way for any operator implementing an automated system – had a duration of at least 4 hours (even 8 at Rotterdam World Gateway) and did not deviate more than 5% from the simulation that determined the number of vehicles required to achieve the target performance. The result in both cases was more than satisfactory: the deviations were well within the tolerances, which means that our model of Lift-AGVs and its control system is very close to reality.
For the ALV system this is lesser the case, hence we had to design the control logic ourselves. Meanwhile, TPS also developed and tested an ALV, of which the specifications could be used. The remainder of this article focuses on the comparison itself. First, we discuss the principle pros and cons of each of the systems (AGV, Lift-AGV and ALV) in a combined qualitative and quantitative way. Subsequently, we discuss some quantitative results from a recent comparison study. Finally, we conclude the picture with a cost comparison.
Qualitative comparison
In the qualitative comparison, we focus on a number of different aspects:
- Apron size
- Wheel load
- Energy consumption
- Maintenance
- Interaction with the QC
- Interaction with the ARMG
- Travel performance (speed, acceleration, deceleration)
- Technical complexity (breakdown risk, recovery, flexibility)
Apron size
The apron size is important as it determines how much real estate is required for a certain terminal throughput. In the cross sections below, two possible high density and high performance layouts are shown. There is little difference between the three systems (see the layouts of ALV and AGV in Figure 1). The fact that we chose to show layouts with four highways with ALVs and six with AGVs, is not because the fifth and sixth highways do not benefit the ALV system; they do. However, we reckon it takes too much (expensive) space, hence the performance impact (limited to 1-2 bx/h) we take for granted.
Figure 1: A typical cross section of a high density, high performance ALV apron
In the back reach of the quay crane four transfer lanes can be installed. All transfer lanes are also used as drive through lanes which means that picking up or dropping a container with an ALV occupies a drive through lane. Due to the driving patterns of ALV neighbouring lanes can be affected when entering transfer points. In contrast to this, in the AGV concept transfer lanes and drive through lanes are separated and can be used independently. In a typical back reach, four transfer lanes and two to three drive through lanes can be realised.
Some argue that the ‘parallel buffer’ (the space where vehicles can wait until approaching the lanes in the back reach of the quay crane) is not required in case of ALVs. We completely disagree with that solution, when it concerns large terminals that require high performance. It may work when there are only three to four cranes at max on a vessel, but as soon as it exceeds that, a waiting area is required. More so because the ALV cannot always enter in case the quay crane (QC) is accessing the interchange zone. Actually, the AGV can access the transfer zones more frequently, as it can wait under the QC, where the ALV cannot.
Figure 2: A typical cross section of a high density, high performance lift AGV apron
Wheel load
The deadweight of the vehicle, the maximum pay load and the number of wheels determine the maximum wheel loads, which is an important factor in the pavement design. In the below table, the static values (dynamic influences for ALV will be higher due to higher center of gravity) for various types of vehicles are shown:
Figure 3: Vehicle weights and wheel pressures
Two things can be seen in Figure 3: the wheel loads of an AGV and ALV are almost the same, where the maximum pay load of the ALV is 20 tonnes (t) less. This is an issue with twin containers above 50t, which is typically 5-10% of the twin pairs. They have to be delivered in singles, reducing the productivity of the ALV substantially. This can already be observed in many straddle facilities that have twin-lift QCs, and single lift straddles: during twin-lift operation, the QC is waiting for the straddles, despite the – in the end – higher QC productivity (as it lifts two containers per cycle).
Energy consumption
Fuel (or energy) consumption is an important cost factor when a machine operator is taken out of the equation. Obviously, a heavier machine consumes more fuel, especially in an operation where there is a lot of starting and stopping, as acceleration consumes most power. In addition, there is the need for lifting (Lift-AGV) and hoisting (ALV) that requires additional energy. Apart from the demand, there is the possibility to run the machines completely by battery; increasing the energy efficiency quite dramatically and resulting in a real zero-emission when purchasing green energy. In a linear fashion this also affects the CO2 emissions, which are two (diesel-electric) to ten (batteryelectric) times less between a Battery AGV and a diesel electric ALV. The Lift-AGV hovers somewhere in the middle, being heavier, and having to lift the containers at the interchange with the stacking crane (ARMG).
Figure 4: Fuel consumption and emission data (diesel at 1 Euro per liter, and energy at 0.15 Euro per kWh)
Maintenance
Maintenance practices worldwide vary tremendously and solid comparative data is hard to get. Not least because maintenance cost are measured quite differently. Typically, one should consider the labour hours involved, the spare parts required, as well as the wearing materials such as tyres and lubricants.
In general, one can say that the less moving parts, the less maintenance, and as a consequence, the battery AGV is very low on maintenance, followed by the Lift-AGV. Most maintenance – and easily five times as much per running hour – is the ALV. A hoisting mechanism, a spreader that locks and unlocks all the time, a heavier vehicle, a powerful diesel drivetrain and difficult accessibility of components: these are all factors that make it maintenance intensive. If we would have to rank them, the following table results:
Interaction with the QC
An area of much confusion and misunderstanding is the interaction with the QC. It is obvious to everyone that the AGV and Lift-AGV have a linked interchange with the crane, where ALV has an unlinked interchange with the crane. This inevitably means that the QC should never wait for the AGV, and in most cases the AGV has to wait for the crane (as it is supposed to be). Most operators think that the ALV never has to wait for the crane or vice versa, which is a misconception. When the QC is going to be at the transfer point, the ALV cannot always enter (it depends on the transfer point arrangement, but the access is certainly limited). The other way around is also true: in some cases the QC cannot enter because the ALV is at the transfer area. As a result, both QC and ALV lose time during this interchange process.
Moreover, the picking up and dropping off of the container takes a substantial amount of time. Whereas crane and AGV will find each other blindly, the ALV has to search for the container, which is inherently slow (in practice we measured here interchange times of 60-120s, whereas the handshake crane-AGV typically takes in the range of 15-30s).
Another complicating factor is access to the QC. As vessels are getting wider, the crane density on a vessel is increasing (sometimes to up to six to eight cranes). This leads to large clusters where access is limited (see Figure 5). AGVs are 3 metres wide, ALVs just over 5 metres, requiring lanes of 4 metres and 7 metres wide to drive on, respectively. Furthermore, the ALV needs to align before it drives over the container, where the AGV is not slowed down by containers standing on the ground. Driving over other containers (standing on transfer points of neighbouring cranes) seems so convenient, but takes place at very low speed (typically less than 5 km/h), blocking access of the QC to those transfer zones.
Figure 5: Access with AGVs to a dense cluster of 5 QCs.
As a consequence, we observe waiting times and the need for queueing also for ALVs, before entering the transfer zones, which requires space. This becomes worse in case a QC is operating in tandem 40, or quad 20, mode. Since ALVs cannot access two adjacent transfer lanes simultaneously (due to the limited spacing a dual hoist or tandem spreader can achieve between containers), the ALVs have to pick-up the containers individually. As the duration of two consecutive pick-up moves exceeds the cycle duration of the QC, the only way is to use at least four interchange lanes. As can be seen in above figure, this becomes quite complicated, if not impossible in case of large clusters. On the contrary, with AGVs side by side access is quite easily realised, especially because the solutions existing today, already cater for two adjacent transfer lanes per QC.
A last remark plays a role in areas with swell: the vessel may move along the quay, causing the transfer point to move (up to 50 centimetres left and right). If a container is already placed by the ALV, the QC needs to gantry (at very low speed) to fetch the misplaced container, which will considerably reduce the crane productivity. AGVs, waiting for their turn, will follow the crane automatically, as such not influencing the STS productivity.
Interaction with the ARMG
At the stacking crane (automated rail mounted gantry, or ARMG), the decoupling (interchange) is less cumbersome, especially for the ALV. The interchange zone consists of nicely aligned lanes, typically offering up to 16/20 TGS space, even usable two high. The interference between ARMG and ALV is less (due to the lower productivity of the ARMG compared to the QC: an ARMG accesses the interchange zone 10-15 times per hour, the QC three times more), and can be controlled by the ECS in an easy way, as both are serving the QC.
Here we can then observe the largest benefit of ALV over AGV and to a lesser degree over the Lift-AGV. The Lift-AGV also allows for decoupling through the rack, but this buffer has less capacity, and there are still containers (such as tank containers) that cannot be transferred through the rack. When we analyse the duration of a typical AGV cycle, we see that the AGV waits at the ARMG transfer point to be served in the range of 35-45% (of the entire cycle) under peak conditions (meaning also the ARMG’s are under pressure). Lift-AGVs and ALVs only spend approximately 5% at the ARMG transfer point, which immediately explains the benefit of Lift-AGVs over AGVs.
Figure 6: Lift AGVs entering the racks
If we compare the size of the ARMG interchange, we also see clear differences. In case of a nine wide stack (a typical average value), we see five AGV transfer lanes, four racks plus one direct interchange lane, or four independent transfer lanes for ALVs which are four TEU deep. The total decoupling possibilities hence range from 0 (AGV), to eight TEU (Lift-AGV) to 16 TEU (ALV). The larger buffer of the ALVs has another benefit, as has the rack interchange to a lesser extent: it improves peak productivity of theARMG’s by 10-15%, and by 5-10% in case of the Lift-AGV. So for a proper comparison between transportation systems, this is also a factor.
Travel performance (speed, acceleration and deceleration)
At equal waterside productivity, every horizontal transportation system has to deliver the same number of movements per hour. This means that the traffic – except for the space occupation of an individual vehicle – is equal as well, regardless of the amount of vehicles in operation. More important is the actual space consumption of an individual vehicle while driving. This is in the first place determined by the size of the vehicle, but also by the speed and the achievable acceleration/deceleration.
Figure 7: AGVs waiting for each other
Automated vehicles drive according to the ‘brick-wall’ concept, reserving space ahead of them equal to their braking distance extended with safety distance needed to compensate for reaction time. So the faster they drive, the more space is being reserved (with increases quadratically with speed increase). The actual deceleration helps to decrease the space consumption. This is one of the reasons why faster driving does not necessarily result in a higher vehicle productivity. Moreover, the speed in curves is also limited, and the vehicles need to decelerate to this lower speed before entering the curve – as such posing a blockage to succeeding vehicles on the same path. Compare it to normal traffic: if you follow a car that has to take a turn, it slows down before doing so, causing a ripple effect behind him.
Figure 8: Kinematics of vehicle types (Source: TPS)
Summary pro’s and con’s
Within the preceding sections we discussed various aspects of the options for automated horizontal transportation. In summary, we have listed the system, as well as a benchmark in the form of manual shuttle carriers (see Figure 10).
Performance and cost comparison
A single performance comparison between the systems in question cannot be made. Various terminals pose different circumstances, and therefore different results. Especially the type of QCs, the number of ARMG’s in relation to the number of QCs, as well as the overall targeted performance level determine to a great extend how large the fleet of vehicles needs to be to achieve the targeted performance levels.
Figure 9: Performance and cost comparison (note: labour @50 Euro / h, 1.5 men per machine hour, fuel at 1 Euro / l, electricity at 0.15 Euro / kWh).
However, if we have to provide a rule of thumb to compare the system, comparing results from at least 15 different terminal simulations across the world, the following ratio results (note that prices may vary based on commercial conditions; they should be treated as indicative):
Figure 10: Overview of qualitative KPI's;(here green = best, orange = middle, and red = worst)
In Figure 9, we see that the most productive vehicle is the manual shuttle carrier, which is proven in several highly productive ARMG-shuttle carrier operations. The ALV, due to restrictions in traffic, and at the QC, performs significantly less well, hence to achieve the same productivity level, more vehicles are required. The lack of decoupling of the Lift-AGV, requires an additional 0.5 vehicle per QC, despite other advantages in traffic compared to the ALV. The AGV system is least productive (per vehicle), mainly due to the coupling at ARMG and QC, which costs about 50% of its theoretical performance.
The picture changes however when we combine the performance figures with the financials. We decided to quantify this as a CAPEX per QC and a yearly OPEX per QC (for the vehicle system). Here we can observe that in a developed country (with high labour costs, here assumed at 50 Euro per hour), the manned system is much more expensive than the automated systems. Already within the first year, the additional CAPEX for any of the automated systems is earned back.
This leaves us with the comparison between the automated systems: here the lowest CAPEX and OPEX are achieved by the battery Lift-AGV, not in the least because of the much lower OPEX (the benefit of the fully electric drive and hence lesser maintenance, as well as the energy consumption being much lower) outperformance both the battery AGV and the ALV.
Conclusion
In our view, momentarily the battery driven Lift-AGV provides the best value for money and can present zero-emission at reasonable investments. The attractive performance of manual shuttle carriers in some terminals is no guarantee that an ALV will show the same high productivity. As can be seen from our simulations, there is a substantial decrease in vehicle performance to be expected when modifying manual shuttle carrier system into an automated ALV system.
From a total cost of ownership point of view the Lift-AGV may prove to be he most attractive concept. However some operators prefer simplicity and lower infrastructural investments that an AGV brings. The somewhat larger fleet of vehicles (in an AGV system) has the advantage of less risk from breakdowns and the replacement of vehicles (at the end of their lifetime) will come much later in time. After all, ECT, CTA and Euromax are proving to be very successful terminals, with reliably high performance levels.
Share this
You May Also Like
These Related Stories
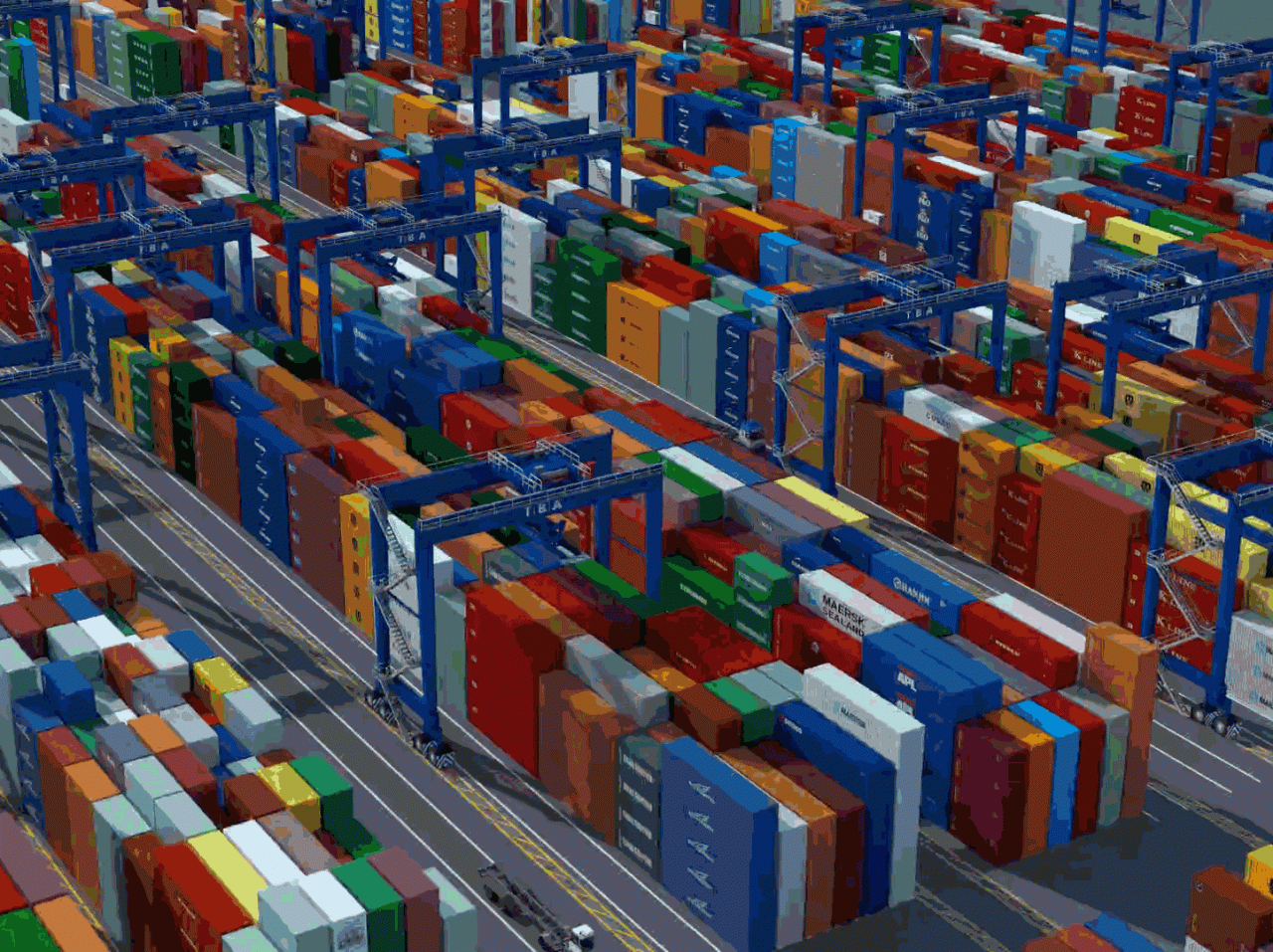
Optimisation as mantra for operational excellence
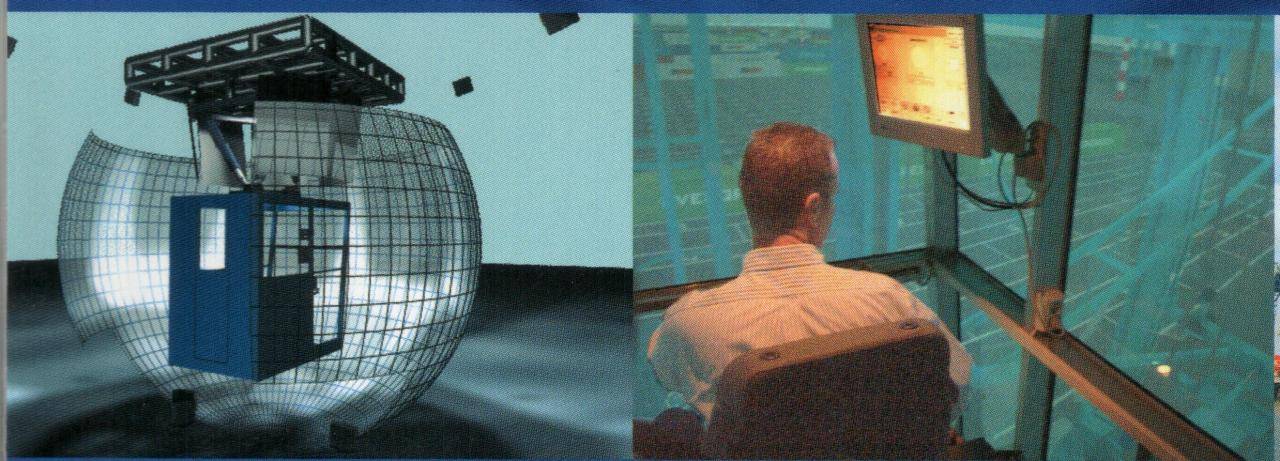
Human Machine Interfaces - the key to productivity?
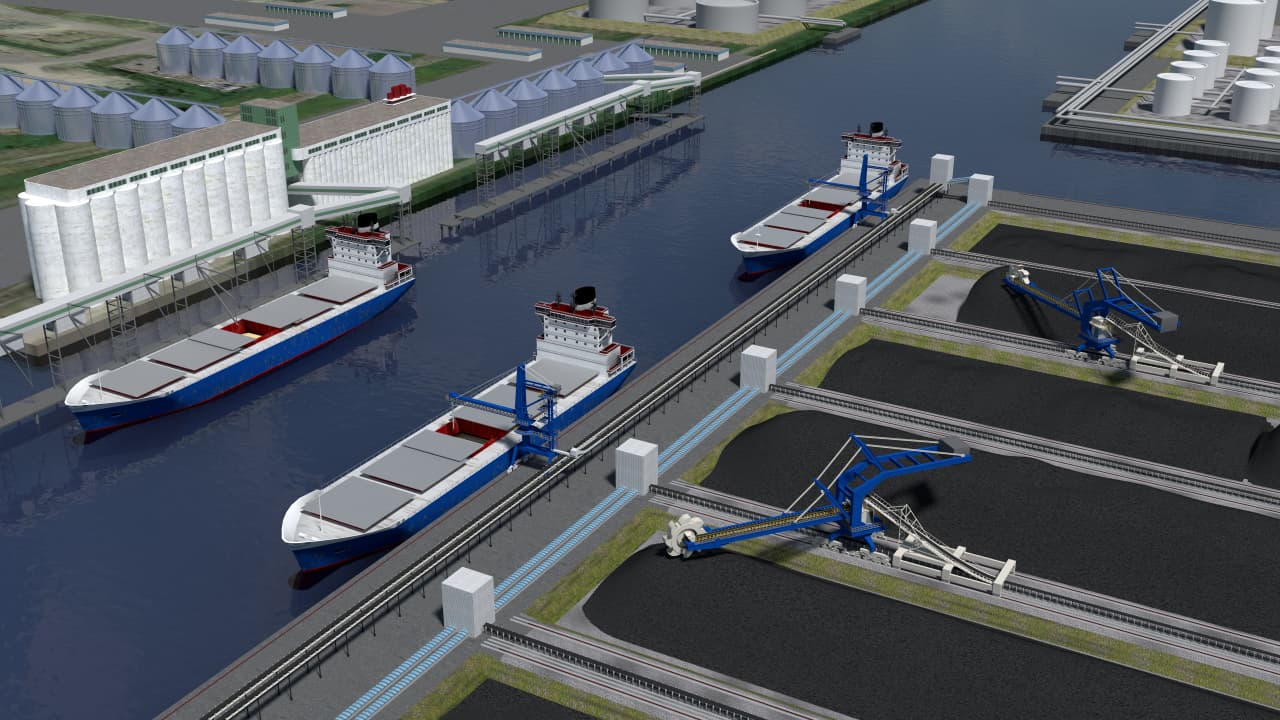