Terminal Automation: Key Questions Answered
Since the early nineties, terminal operators have been working on robotising the equipment at their facilities. With the recent openings of the new facilities at Maasvlakte 2, robotisation in the container industry has reached its all-time high. What are the implications for the sector? Should we expect others to follow quickly, or will developments come to a (temporary) halt? What are the social impacts of ongoing robotisation? What are the technologies available? Has integration reached a level of maturity, or are the projects still “state-of-the-art” in the worst sense?
Many questions can be raised concerning container terminal robotisation. In this article, at least some of them will be answered, but not before briefly paying attention to a much more widely spread form of automation: process automation. This category of automation includes technologies that typically replace clerical labour: identification, inspection, registration, and similar tasks. The most common application is gate automation, where truck and container, and increasingly damage and seal presence, are automatically identified and registered. Also quite common are position detection systems (PDS), which assist the terminal operator in locating containers and equipment. Both types of technologies have been successfully implemented and are offered by a broad range of vendors.
How is it possible that there are still so many questions concerning robotisation? At first sight, robotisation seems much more attractive to implement: it replaces heavy, dangerous and repetitive work, where many clerical functions are much lighter. So more reason to implement robots... Yet, terminal operations can be characterised by their dynamic (read: unpredictable, badly planned, erratic) nature. This is caused on the one hand by the poor information basis underlying terminal operations. It remains remarkable how much container information changes when the container has arrived at the facility. On the other hand, it is caused by the way processes at the terminal are linked to each other. The latter has consequences for the impact of a disturbance (of any kind) in one process for other linked processes. This issue will return later, when the importance and complexity of integration is discussed. In the next sections, an answer is sought to answer the questions raised.
Implications for the Sector
With a few exceptions, the current automated terminals are a success, in terms of performance and financially. They generally offer a reliably high service level even at high density. Best examples are CTA (HHLA) in Hamburg and Euromax (HPH) in Rotterdam. This means that other terminals face increasing competition when one of their competitors introduces automation, or develops a new terminal in the same range.
A good example is the semi-automated DP World terminal in London (London Gateway). It offers a high service level and high capacity close to the hinterland. It is expected that it will impact terminals such as Thamesport, Tilbury and Felixstowe, its main competitors, on the middle to long term.
Simulation of automated quay crane operation, second cat at Automated Guided Vehicle with Lift.
A similar impact, or even greater, can be expected from the fully automated terminal in the Port of Los Angeles/Long Beach, being developed by OOCL. The terminal will introduce a substantial new chunk of capacity in a highly competitive market. The capabilities of the terminal in terms of handling speed and capacity are (by far) the highest in the port. Its cost base will be substantially lower than any other terminal on the West Coast of the United States. So impact is imminent and guaranteed.
Simulation of Automated Guided Vehicles with lift and automated stacking crane, stack quayside.
What Is Next?
APMT and RWG in Rotterdam have taken a bold step forward, substantially extending the degree of robotisation: remotely controlled quay cranes, fully automated horizontal transportation (battery driven, with automated battery exchange station), fully automated stacking cranes, including fully automated truck handling (only incident handling by a remote operator), as well as automated transport to the rail terminal in the case of APM.
We should not expect any further steps soon, other than more of the same. Development that needs to be taken very seriously is the automation of straddle carriers, and of rubber-tired gantries (RTGs). The automation of the first does not require large investments in civil infrastructure to enable the automation. Replacement of the fleet of machines, or even automation of the existing machines is required, and the additional communication infrastructure is quite limited. The second is the automation of RTGs. As RTG yards have trucks amidst them over the roads, robotisation is tricky from various perspectives, with safety and liability as most important aspects. Several terminals are working on remotely controlled RTGs, but a large scale terminal has not yet gone into operation. Avoiding conflicts between the road trucks and the remotely controlled RTGs remains a safety risk. For now, we foresee that it will be limited to automated working inside the stack, and full remote control during the truck handling as well as during the movement along the stack.
Social Impact?
When discussing automation, we cannot go beyond the social question. The direct impact on dock workers is obvious and painful. Here, a broad and long-term perspective has to be taken. First of all, the jobs that are being replaced can be characterised as hazardous, repetitive and isolated. They are (partially) being replaced with office jobs, with no risk, and in a more social environment. Instead of spending a number of hours alone in a machine, people are in an office together, carrying out these tasks together.
Besides, new jobs are being created. Jobs that require a higher education or more training. Jobs that are in general more attractive to the future workforce.
Finally, the competitive edge of automated ports exceeds that of non-automated ones. As many ports are typically serving the same hinterland, the increase in capacity and efficiency makes the ports more attractive, leading to more volume (in the longer term), or if they do not increase automisation to lesser volume. So not embracing new technology may lead to an obsolete port, and a larger loss of jobs (also in the businesses related to the port).
Technologies Available?
These days, we are surrounded by technology. The same types of technology that enable the automation and robotisation that can be observed in ports. Communication and location determination is thought to be easy, yet we tend to forget that a cell phone regularly has no reception, and that GPS is regularly off by more than just a few metres. The batteries in even the newest devices do not last for more than a day, and the automated cruise controls in cars can only be used as driver’s support.
The precision, durability and reliability required for fully automated operations are still expensive and not yet common off-the-shelf. Although it relies on the same type of technologies, the scale is much bigger (an AGV battery is about five times that of the largest electric car battery, the one of the Tesla S), the intensity is much higher (the equipment easily runs more than 5000 hours per year and then for ten to twenty years. Compare that to a road truck: it would mean a mileage of 3 to 4 million kilometres) hence the requirements for durability are much, much higher.
Finally, it really needs to be automated. There is no driver to correct the robot’s behaviour in unforeseen circumstances. Of course, circumstances vary a lot less than on the public road, yet, the last ten per cent of automation proves to be the hardest, mainly because of integration.
Maasvlakte 2 in final stage, all container terminals automated.
Integration across Technologies?
This brings us to one of the key challenges remaining in port robotisation and automation: integration of pieces of kit, typically supplied by different vendors. Integration is a challenge not only applicable to the port industry: it causes headaches in each and every sector. It worsens in case of fully automated, as humans involved in the process can solve small inconsistencies and improvise when the robot does not behave exactly like it should. Other automated parts are less capable to deal with other’s flaws. They are more like black and white: wrong input means error, and error typically means “Stop”. When many different pieces of automated machinery come together, it easily leads to something to stop, and hence the entire chain of processes to stop.
This makes integration across vendors and technologies a key area in a successful project. Continuous dialogue, joint specification work, early integration testing, and rigorous, rich and dynamic test environments are inevitable.
Standardisation of communication protocols, communication buses, and integrated test environments are the answers to this complex puzzle, and slowly but steadily improve the ease of integration. By no means has the industry reached its limit and every new development causes new challenges.
Inevitable
There is no doubt in our minds, automation and robotisation are the future in container terminals: the advantages simply outweigh the drawbacks by too much to resist. The associated cost, the limited experience in the market, the integration issues, social issues, and many other less important reasons will still cause terminal operators to choose simpler, quicker and more proven solutions. However, in the long run, container terminal operations will be robotised.
This article has been published in SWZ Maritime in January 2016.
Share this
You May Also Like
These Related Stories
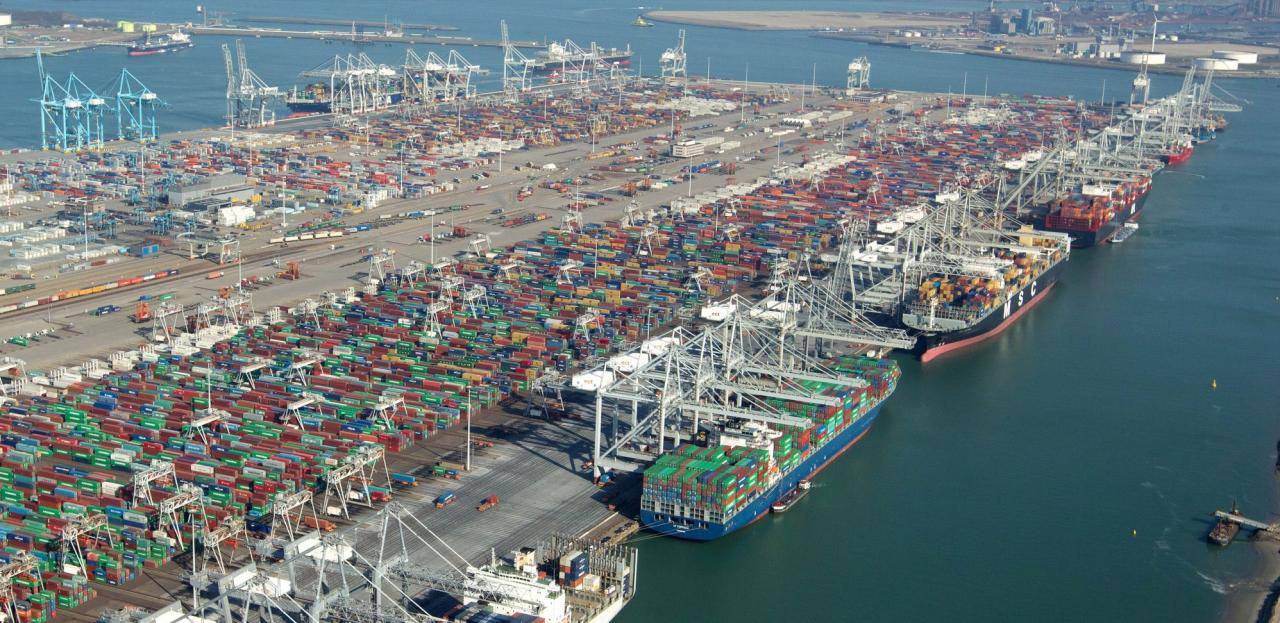
Applying new technologies in an existing automated terminal
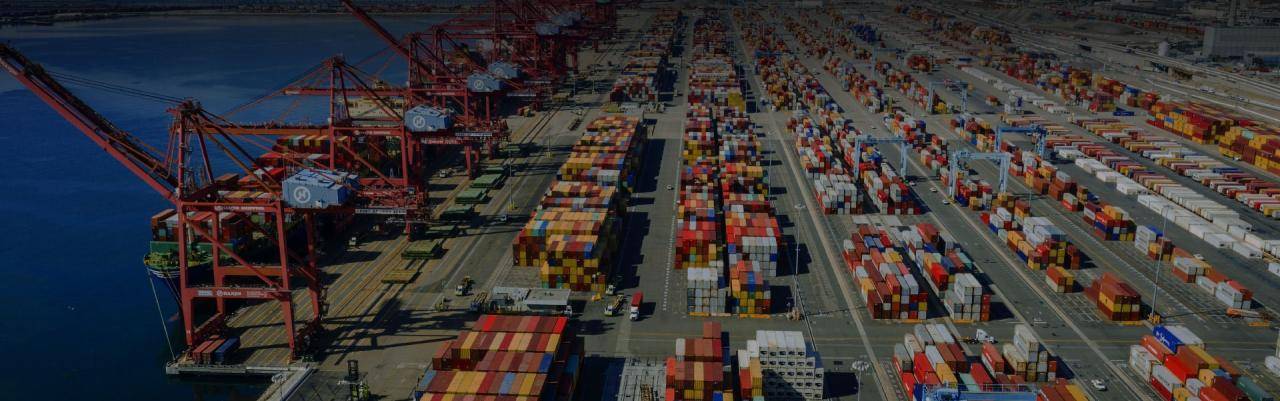
How can simulations help ports and terminals?
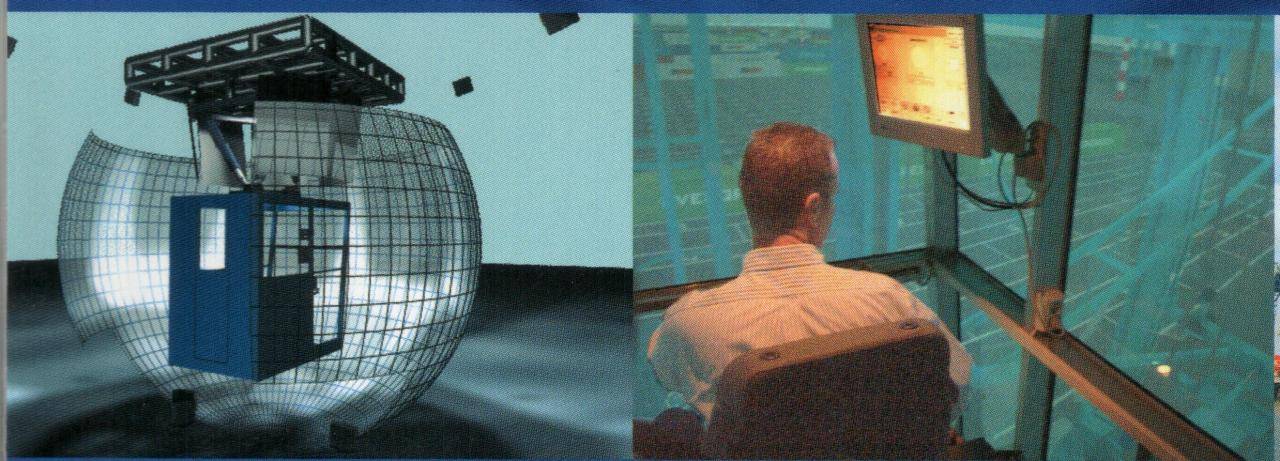