Samskip adopts Autostore TOS for seamless integration in their Reykjavik terminal
Background
Founded in 1990 Samskip is a global logistics company with turnover of around €680 million and offices in 35 countries. They operate cargo transportation services by land, sea, rail and air, delivering cost efficient, reliable and environmentally sustainable solutions.
Samskip’s activities focus primarily on: European multimodal transport; North Atlantic integrated logistics (between Iceland, the Faroe Islands, UK and mainland Europe); worldwide temperature controlled & ambient cargo forwarding and logistics; plus European break bulk and project cargo movement.
The search for a solution at Vogabakki Terminal
In 2018, the operations team at Samskip’s Vogabakki Terminal at Reykjavik in Iceland began planning the replacement of the legacy container terminal management system. The objective was to replace the proprietary finance and cargo management system, developed in the late 90’s, with a modern alternative.
The upgrade, through modernised software solutions, would see Vogabakki’s operations transition from a largely manually controlled container terminal to an environment with an efficient layer of automation that would:
- Transform the efficiency of import/export operations.
- Enable the terminal to make step-changes in growth.
- Interface seamlessly to Samskip’s DORIS shipping system and TruckCom.
The key performance metrics for the project were defined as:
- Consistent, stable and error-free operation.
- Cargo discharge and container throughputs.
- Crane performance.
- Gate operation (in/out).
- Vessel and truck dwell times.
The secondary objective was to create a future-proof terminal software management platform that would deliver straightforward terminal optimisation in the future.
- Key to delivering this is the ability to measure live operations in real-time and where necessary, be able to trouble-shoot and solve any issues quickly and effectively.
The selection of Autostore TOS
Re-engineering container terminal management from the ground-up is a major undertaking. It’s an operational-critical decision and relies on selecting the right platform, with the right support and the right futureproofing.
Samskip selected TBA Group’s Autostore TOS against the following criteria:
- A proven international track record within container terminals.
- Strong operational footprint in Europe and a partnership-led ethos.
- Leading level of support and value-added development in areas like automation and optimisation.
- Exceptional gate management and OCR-ready software solutions.
- Modular expansion capabilities into areas such as vessel loading, planning optimisation and vessel planning consultancy services.
- Innovative touchscreen field apps on ruggedised handheld devices for reach stacker drivers and terminal truck operators.
What are the benefits of Autostore TOS
Samskip’s legacy system meant day-to-day terminal operation required a high level of manual work. For instance, the input strategy for container moves required two to three people to key in stack locations for the reach stacker to execute each move.
Autostore TOS now enables the Samskip team at Vogabakki to:
- Automate container input strategies and equipment dispatch.
- Automate gate control and vehicle booking.
- Seamlessly integrate daily operation to the terminal’s order system for accurate stacking on discharge.
- Receive EDI pre-notification of container cargo manifests ahead of ship arrival and cargo discharge, storage and transhipment.
- Gain a full picture of operations across the terminal yard.
- Plan pre-despatch location management for late or changed truck arrivals that enables operations to flex in line with daily demand.
In short, Autostore TOS is transforming the ability of Samskip to:
- Plan for changes in terminal demand, with full and seamless integration with existing business systems.
- Design new, stream-lined working processes that deliver smoother operation, enhanced throughput and performance while requiring fewer people.
- Manage the flow of reefer containers during the cycle between vessel, quay and warehouse.
TBA Group’s significant investment in optimisation and automation consultancy and solutions also gives Samskip a very strong platform to evolve terminal operations organically, responsively and dynamically.
What do Samskip’s users think?
The response from the operational team at Vogabakki has been very positive:
- The new yard management capability has transformed daily oversight and control of operations.
- Power-users are now able to model scenarios and develop continuously improving processes based on the advanced capabilities of Autostore TOS.
“Autostore TOS has made operational life for us a great deal easier. Productivity has increased for both people and our assets level. We now have a real-time picture of throughput, performance and operation that gives us the platform we want to grow the business and adopt the automation technologies we need, when we need them"
Gudmundur Ingvarsson, IT Manager for Samskip’s Vogabakki Terminal
- Value added service module: Management flow of reefer containers including cleaning, repair and inspection activities.
- Vessel planning module: Quickly and easily create ready-to-go container discharge/loading lists based on vessel profiles and manifests.
- EDI module: Sends and receives maritime messages in industry standard format
- Equipment dispatch module: Ensures the right assets are in the right place with the right instructions.
- Reporting module: Delivering oversight of operations against all key
performance indicators in real-time. - Vehicle booking module: Schedule container receipt and dispatch at the gatehouse to suit terminal operating hours or capacity - day-to-day or week-to-week.
- Autostore TOS Mobile field apps: Vehicle-mounted and handheld for operational staff.
Share this
You May Also Like
These Related Stories
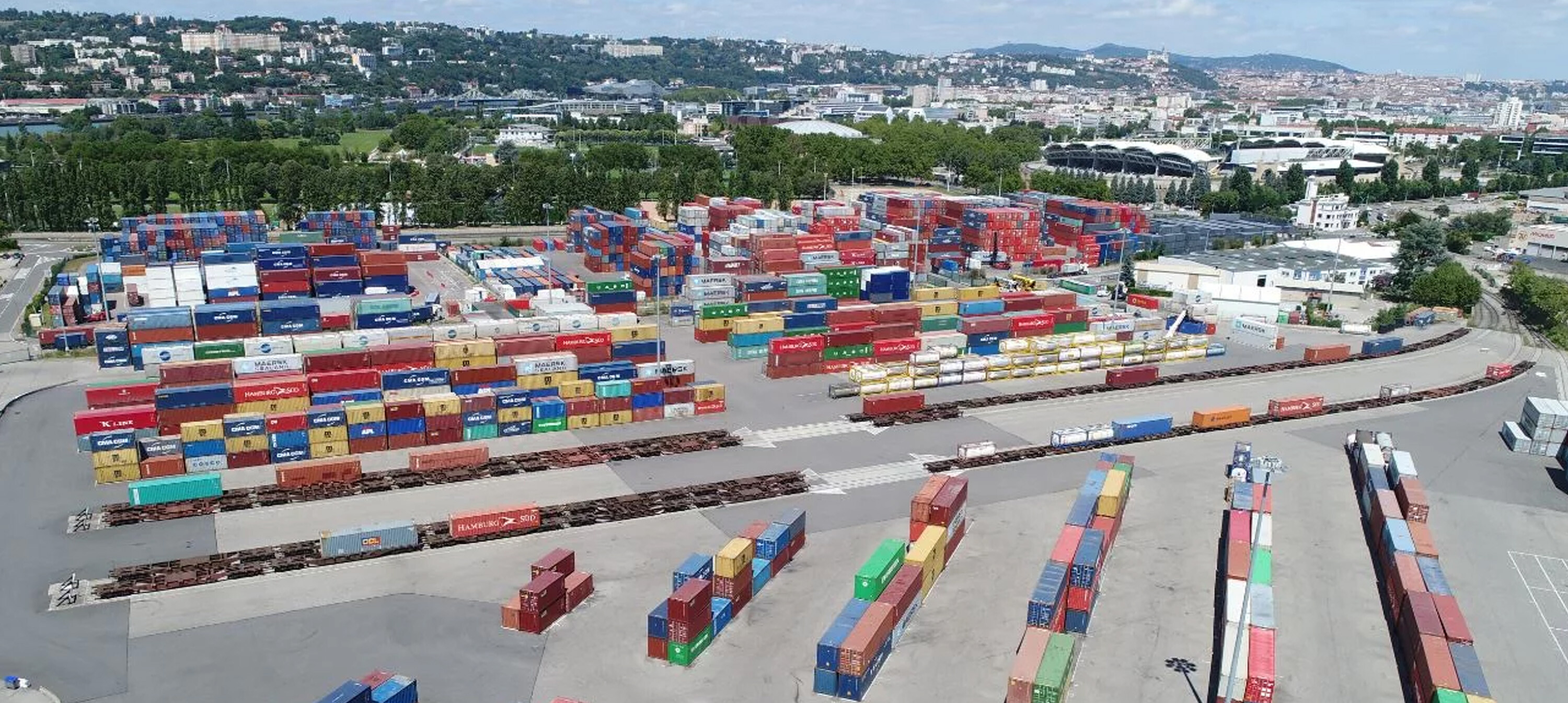
Autostore TOS provides increased efficiency at Lyon Terminal, France
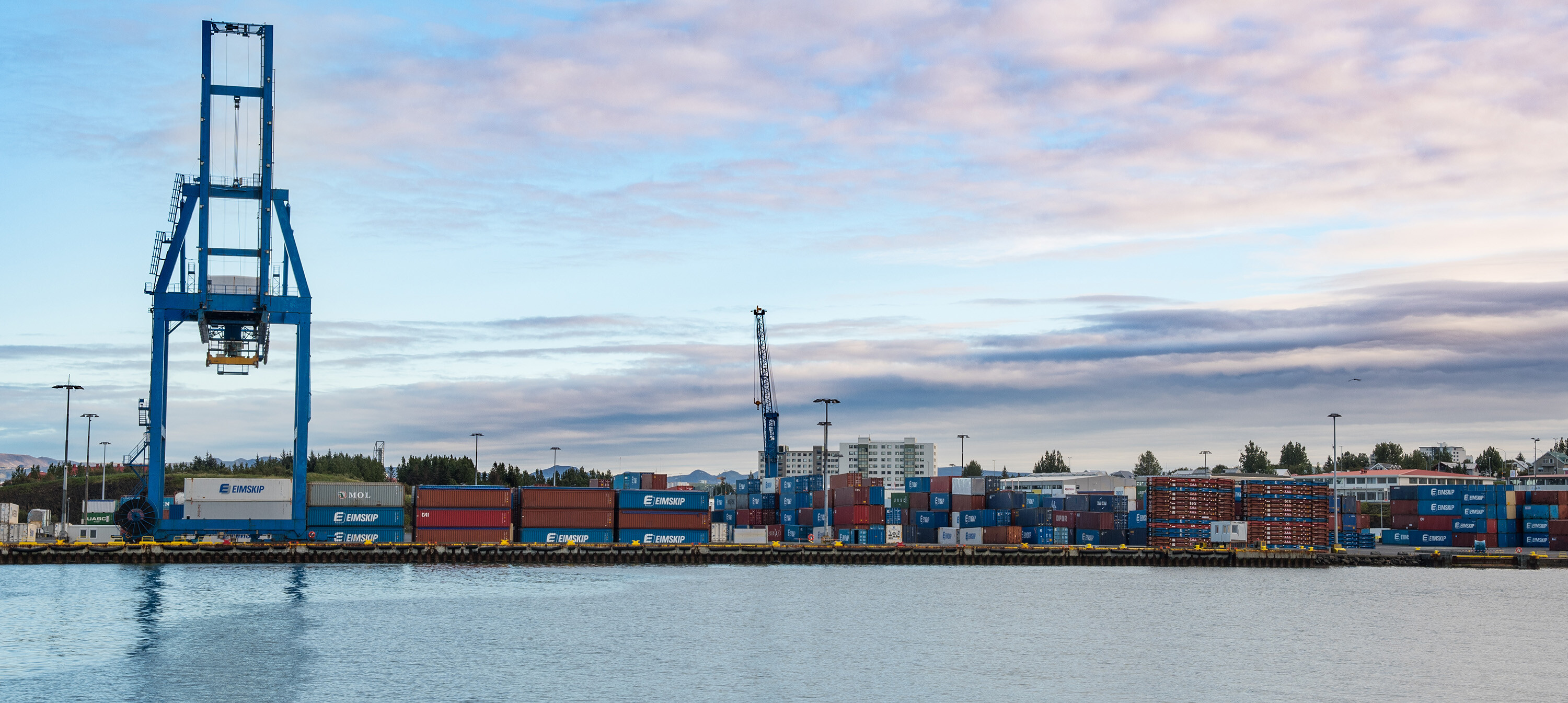
Eimskip automate and streamline their processes with Autostore TOS
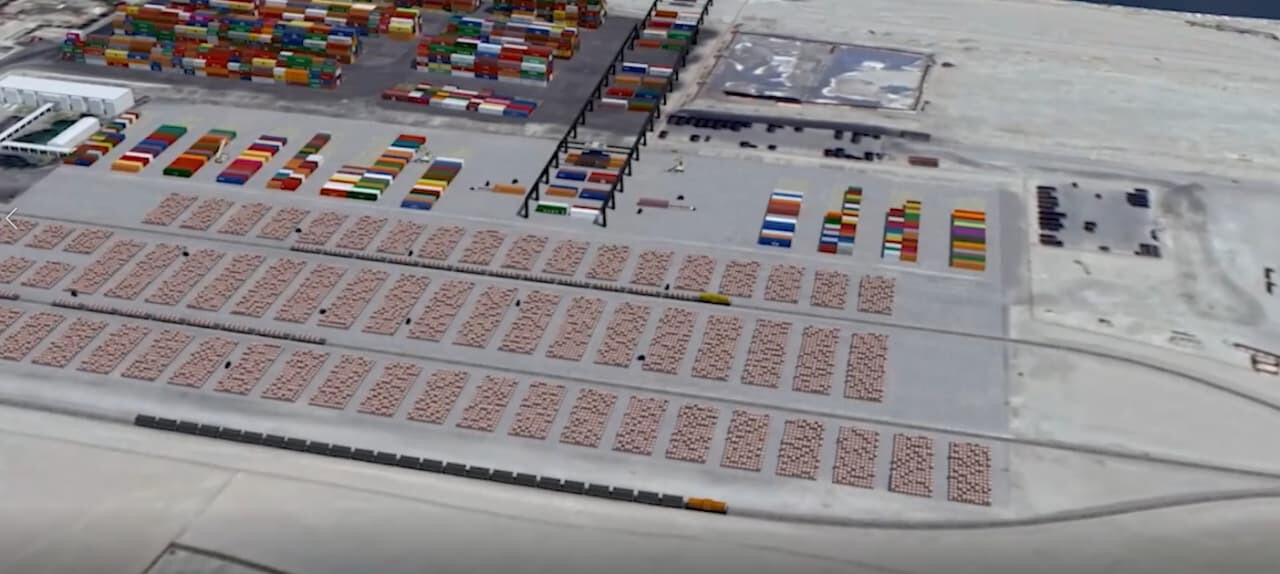