Encirc operates Europe's largest automated warehouse with Autostore WMS
A platform for future growth
Encirc, a leading-edge manufacturer and filler of glass containers and an integral part of the Vidrala Group, is continuing its long-term collaboration with The TBA Group. The TBA Group is a leading international provider of software and services for ports, terminals and warehouses. The continued partnership will include the implementation of a significant upgrade at Encirc to its Autostore WMS.
Encirc’s Elton plant in Cheshire, UK, houses Europe’s largest automated warehousing facility, which is situated in-between a highly automated glass container production facility and a glass container filling production facility. The automated warehouse is pivotal to the success of Encirc’s 360 supply chain offering.
Encirc & TBA started working together in 2005 with a dedicated team of specialist systems engineers that designed and developed a warehouse management system (WMS) that would enable optimal warehouse operations accounting for and adapting to many complex product flows. After years of continued growth and scaling, Encirc and TBA will work together on this project to modernise the WMS systems, solutions and create a platform for future growth.
Why the upgrade to Autostore WMS V6?
Given the growth in Encirc’s business, Encirc and TBA discussed the need to upgrade the WMS to Version 6 with the emphasis on looking to the future. The business keeps evolving and there was a need for different ideas and solutions that would enable more varied service provision to customers. With the extended functionality within V6, those solutions can be implemented and the outcomes will enable further growth and increased throughput.
Customers are becoming increasingly demanding and the new system will help meet these expectations.
“The growth that we want to generate through our customers is being limited by being on Version 5 and specifically by not having an integrated case picking functionality. We have opportunities to grow through more efficient, automated case picking which also offers the potential of shorter lead times, the more sophisticated and quicker the system is that we have. These kinds of service provisions are what we want to generate through Version 6.”
Mark Williams, Strategic Project Manager at Encirc
The sheer scale of operations is another reason to improve efficiencies. With a current physical capacity of 256,000 pallet spaces, 3 kilometres of conveyors and 24 cranes the operations are complex. Tracking movements and streamlining throughput will increase agility and reaction time to customers. Accurate metrics in the form of dashboards in Version 6 will enable managers to maintain optimal control of their areas and enhance performance. Insight through reporting will not only help improve internal processes but drive progress towards environmental targets as well. As a logistics business, scrutiny falls on the carbon footprint of operations and it’s important to understand the exact impact of the business on the environment.
“It’s something we need to look at in terms of how much we use, how efficient we are. These are constant demands and they’re for everyone. We have to meet these challenges and V6 is one of the ways of meeting those”
Danny O’ Neill, Warehouse Systems Support Manager at Encirc
To further futureproof Encirc, in the event of warehouses expansion, Version 6 also has multi-warehouse capabilities. As far as benefits directly to the customer, Mark Williams pointed out:
“The benefits they get, particularly customers from beverages, are that we have a system that manages a bonded warehouse, they have trust that we’ve been audited by the HRMC and Autostore is an integral part of providing that control. The system has the ability to adapt to problems within itself and to manage this huge structure safely and efficiently.”
The evolution of relationships
Throughout the collaboration, things have changed an awful lot. From commissioning time with constant change and phone calls back and forth to having face-to-face time with an open agenda, just getting to understand each other’s constraints and complexities. There’s always pressure to deliver especially when production needs demand immediate changes. The foundation has been laid for a good working relationship.
To help new TBA team members understand how mission-critical the system is, a visual representation of the supply chain at Encirc is key in illustrating the effects of system downtime. Stoppages or downtime has a knock-on effect in all the rest of the operation and ultimately to the customer supply. Autostore prevents or minimizes the instances of that happening.
Implementation
The warehouse can’t stop. With the implementation of the new upgrade to Version 6, there’s a strategy in place for commissioning which minimizes the warehouse downtime, which is of utmost importance to Encirc. The amount of planning and cost involved if the warehouse did have to stop for extended periods of commissioning would not be viable. The most important reason Encirc decided to stay with TBA and upgrade to Autostore Version 6, apart from all the obvious feature benefits is:
“The expertise in the TBA team on how the system and our operations work. The business has trust in TBA’s capability to manage the upgrade, as complex as it is. Even in these unprecedented times, the relationships that we have built up have allowed us to do workshops remotely. The detailed knowledge of the people involved meant the project is on track, even in these COVID time”
Mark Williams
In any operation, an upgrade of this magnitude would be challenging, but with careful planning, clear goals and constant communication, the challenges are being met.
Advice to others considering a Warehouse Management System
This system is flexible, proven and its power lies in its ease of usability and maintenance. Being robust and modular, it is easily scalable for small and medium-sized warehouse management applications, right through to the largest enterprise WMS operations. Understanding what the system does and why is an important part of using it to the fullest extent.
The future looks bright for further development and expansion of the relationship between Encirc and TBA in order to extract maximum benefit of the Autostores WMS solution to meet production and customer needs. A valuable partnership with trust and clear expectation management on both sides has been the key to this success story.
Share this
You May Also Like
These Related Stories
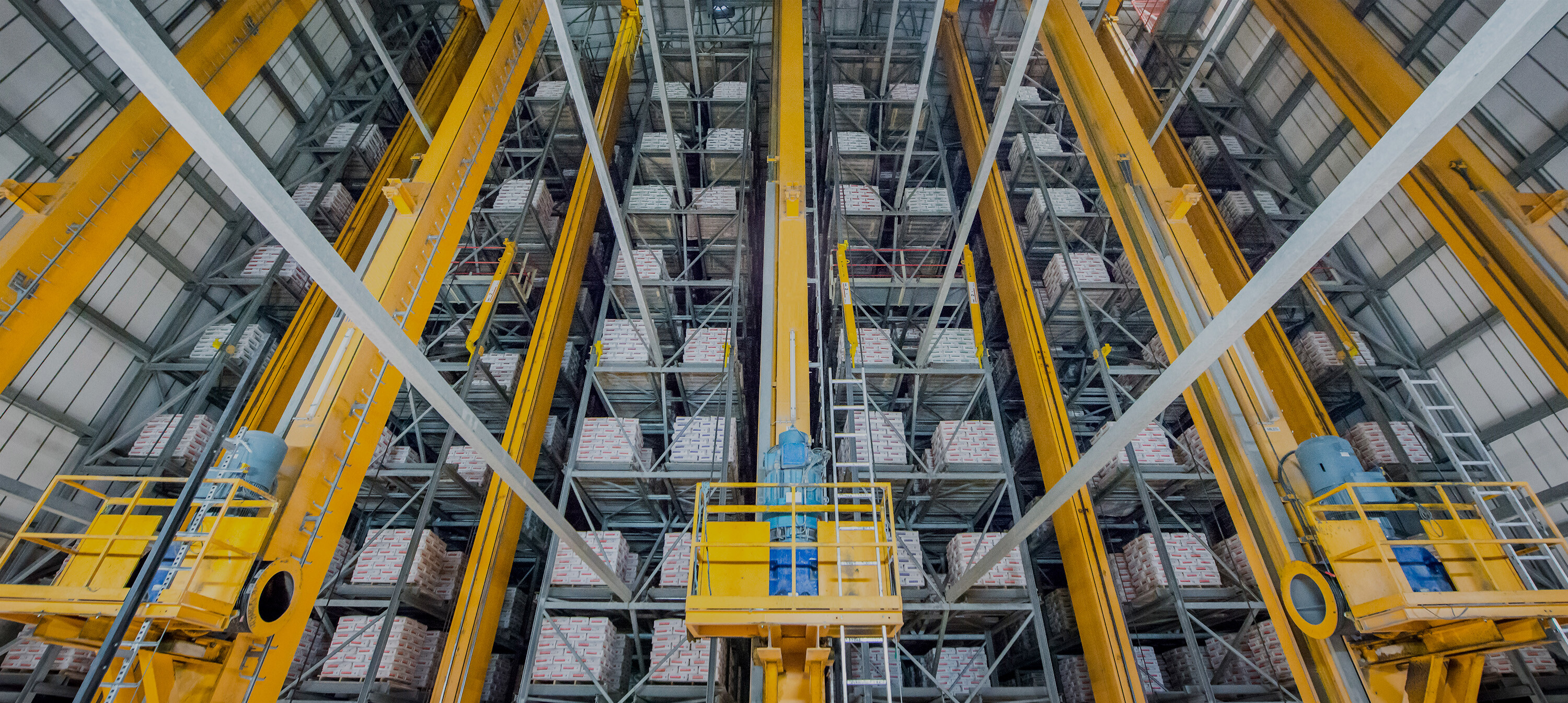
Collaboration and Flexibility for British Gypsum’s Automated Warehouse
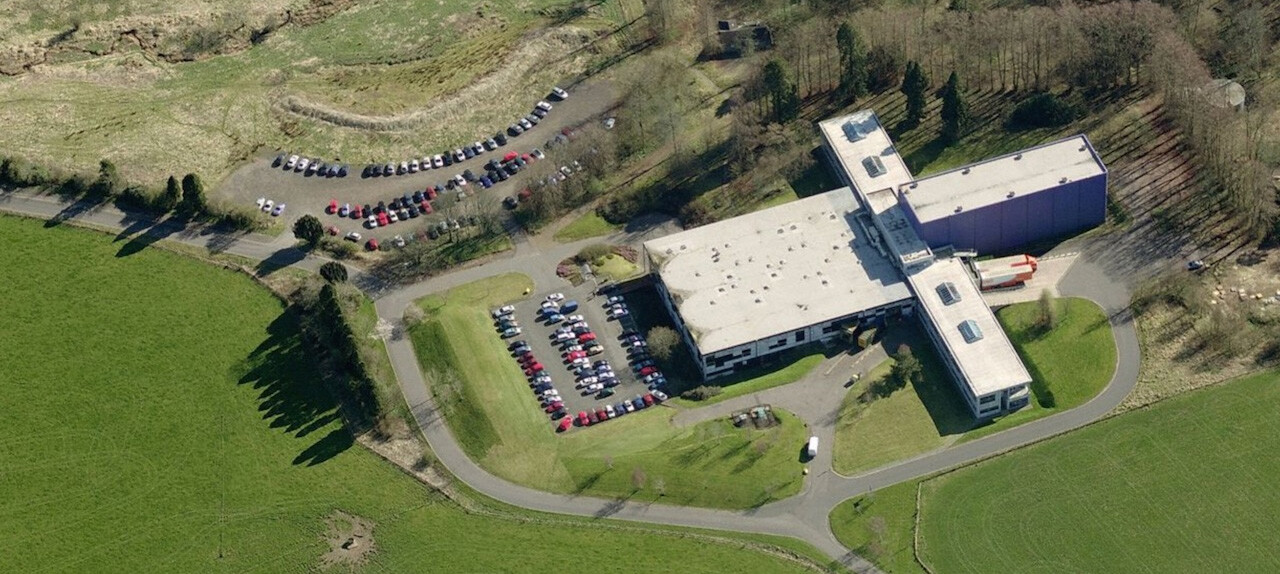
Linn Products modernise their operation with Store Control System
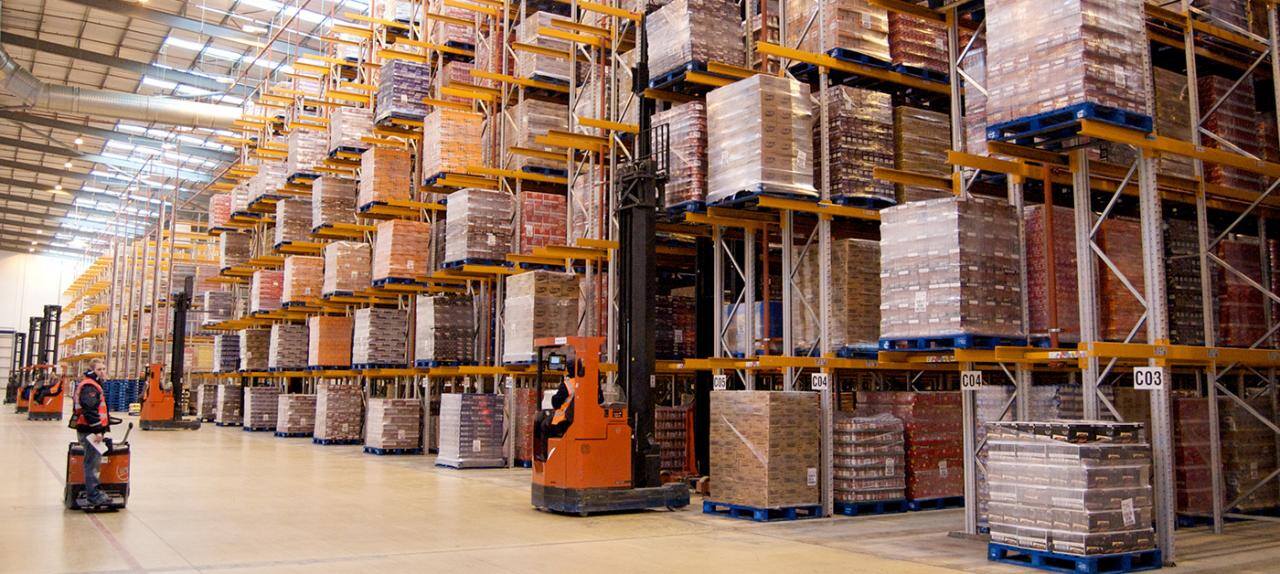