TBA Group provides valuable insights and optimises operational performance levels at Manzanillo International Terminal
Manzanillo International Terminal (MIT) in Panama – part of SSA Marine – is one of the most important terminals in Latin America in the global cargo movement logistic system. MIT provides connectivity to over 125 countries through its transhipment operations. SSA HQ Seattle in the USA involved TBA Group to perform a “Quick Scan” at MIT in March 2020 to investigate opportunities to further improve operational processes and efficiency at their RTG/ ARMG container terminal. One of the areas for improvement discovered through the Quick Scan concerned the yard strategy and the equipment deployment in the yard.
The approach of TBA Group with the Quick Scan (typically completed within 2 months’ time) is to set up an outline towards a more detailed plan for a terminal’s implementation of the recommended improvement measures from the current situation into a more advanced, efficient, and productive way of working. Oscar Caballero, Terminal Manager at MIT, appreciated the objective, outside view that TBA provided:
“It was a welcome opportunity to have an extra pair of fresh eyes and ears to look at our various operational processes and try to identify rooms for improvement”
MIT took onboard the main improvement recommendations that resulted from the Quick Scan and began working on these straight away. Gabriela Soto Pascual, Head of Optimisation at TBA Group, who was involved from the start says:
"During the process of the project and the onsite workshops, we discovered that there were some flaws in the data, some reports were not based on system generated KPIs but on manual input. The first recommendation was to improve TOS logging and create KPIs from one data source so that the KPIs are aligned for the BI department of MIT. The second recommendation was with regards to the yard strategy and the change of allocations in the yard. And lastly, regarding the operations, there were only minor changes recommended; for instance, develop an updated equipment deployment strategy, enforce cooperation between departments, etc.“
Due to the pandemic that hit worldwide in April, and that took place right after TBA’s onsite visit in March, the terminal’s volumes changed dramatically with regards to the initial (snapshot) situation, and from which the recommendations were based on.
“We applied some of the recommendations by TBA but because of the COVID situation, we couldn’t apply all of the recommendations. We evaluated the improvement suggestions provided by TBA and with our experience, we could select the ones we could do and had to pause the ones which were very too difficult to apply here (referring to the terminal’s situation at that time) because of our (COVID) working conditions.”
Stephanie Smith, Business Performance Manager at MIT
The buy-in from management and staff is critical for the successful delivery of process improvement activities. Gabriela Soto Pascual mentions:
“The workshops held with the operational staff/operators were very insightful and very interactive. And what is good is also about MIT is that they were not scared to hear everything that happens on the ground floor (instead of like what we have encountered with some other terminals, where there could be resistance to some of the findings that we shared). They were open and willing to listen to us and also receptive to the employees’ feedback and suggestions. MIT is a very involved employer with open communications between management and the operational workforce to know what’s going on at their terminal and to empower their employees.”
MIT appreciated the eye-openers that TBA’s Quick Scan brought them, according to Oscar Caballero:
“There’s value in shaking the tree and trying to make people think., Whenever you can take people aside and out of their day-to-day operation and start looking at the issues incrementally, I always think there’s potential value and TBA’s visit helped us with that.” Stephanie Smith affirmed this opinion: ”People could share their thoughts about what was happening at the time at the terminal and it was great to hear about that. And we could adjust some things that were very easy to change but which we couldn’t see because we were so absorbed in the day-to-day operations like certain tools e.g., dashboards that were not used by many people. Because of the information provided by TBA, we created a project to eliminate all those tools that were not that useful for our users and we kept the tools that were useful for the execution of their job. Because of the exercise we did with TBA, people could share the good things and bad things that they thought would impact the productivity or systems and such.”
This is very much in line with what Dr. Yvo Saanen, Commercial Director at TBA Group, has experienced from the many peer projects that TBA has been involved in:
“Some may think that our quick scan will reveal all kind of unknown things, but generally, the knowledge is present in the organisation. We assist in bringing structure, priorities, and separating the measures that truly contribute to the overall objectives and the ones which do not. All based on data, as that is the key in efficient and effective operations: data-driven decision-making. Therefore, all our quick scans start with a thorough and in-depth data analysis. In many cases, we have seen that the findings from those, are a surprise to many.”
Reflecting on the relationship that TBA Group has with MIT and SSA Marine, the VP Operations at MIT, Manuel Pinzon, acknowledges the expertise that TBA has brought to them and values the involvement to support them in their ever-growing ambition to improve the operations in the best way possible:
“TBA Group was recommended by our parent company SSA Marine to help us scrutinise the possibilities to increase our terminal performance and operational efficiency with the Quick Scan. TBA has provided valuable insights at an early stage in finding the areas for improvement and optimisation at our terminal. Their recommendations and the insights, they have brought to us, have proven to be valuable and our team has made it possible to implement some of the recommendations to improving the terminal operations during the COVID situation. I am very satisfied with the outcome and TBA has lived up to their reputation.”
TBA’s Quick Scan methodology aims to explore the potential gains and to create a foundation for further detailed analysis. For more information, please visit https://tba.group/en/services/optimisation
Share this
You May Also Like
These Related Stories
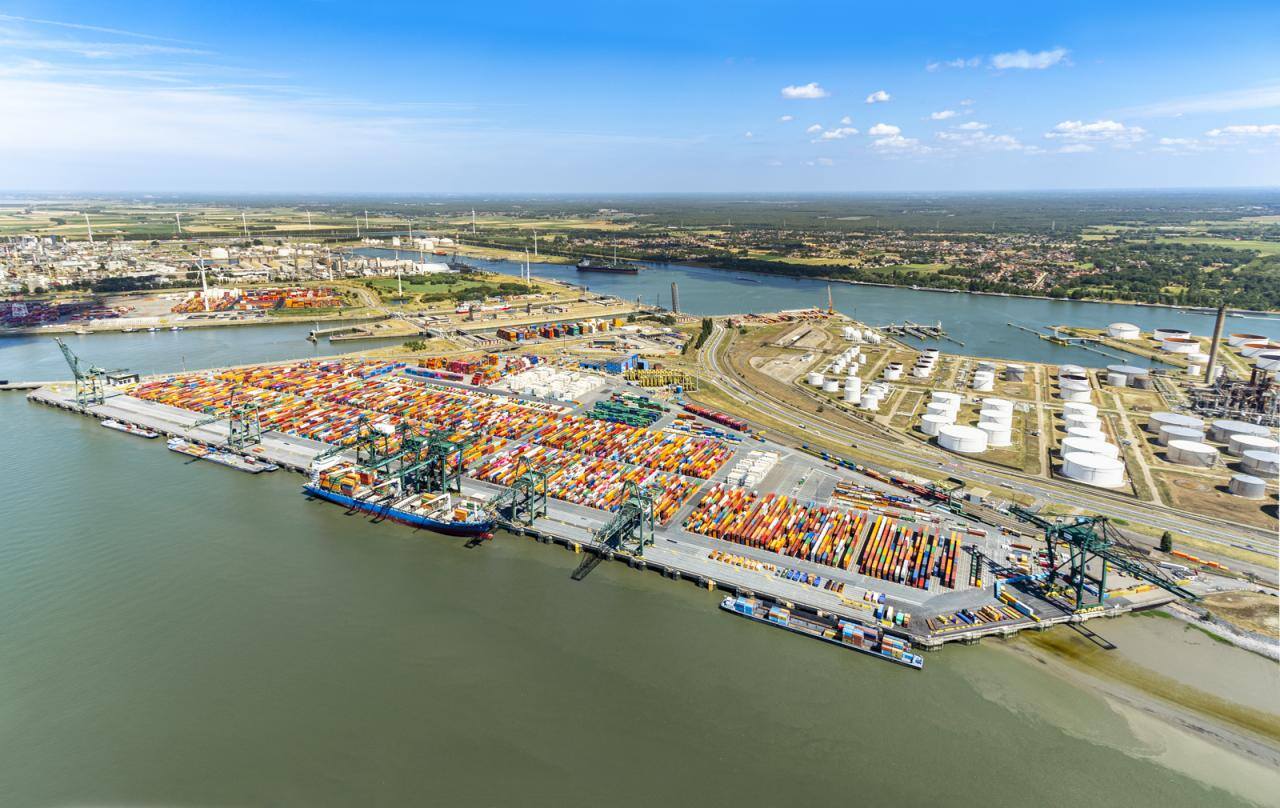
TBA Group wins emulation tender of PSA Antwerp’s Europa Terminal
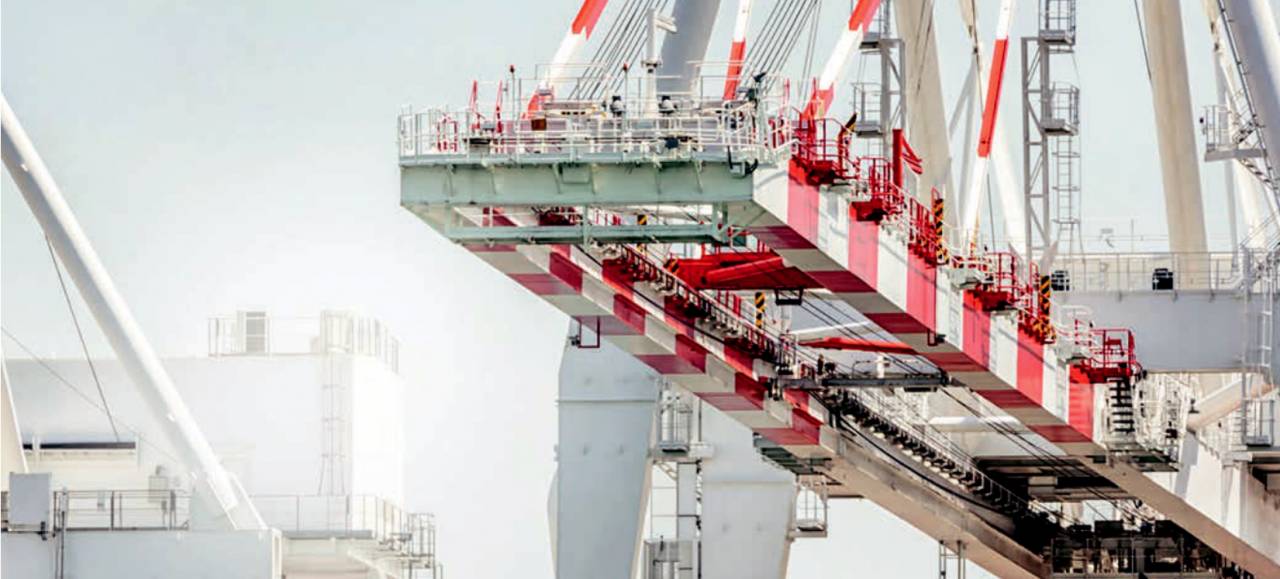
20 years of high-definition simulation in the port industry
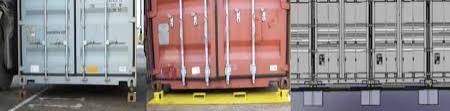