Speaking at the IBJ Awards in November, TBA managing director, David Trueman, acknowledged the important role played by the company’s early customers. “In the beginning, they bet on us when we had nothing but an idea. We were bright and we were innovative, but we didn’t have anything. They took a chance. At times it felt like we were evangelists preaching to the industry, and now it finally feels like everybody’s on board with digitalisation.”
Receiving the 2023 Special Achievement Award was the culmination of over 20 years of hard work, innovation and constant striving for improvement, in an industry often ‘late to the party’ in terms of embracing new technology to streamline and improve processes at bulk cargo ports and terminals. Unlike the container terminal environment, where a terminal operating system (TOS) is a standard prerequisite, the bulk cargo sector is so operationally diverse that a single system was not considered feasible and so ports and terminals remained reliant on manual processes. Where digital systems were present, they would be separate from one another, with data being transferred from one system to another. Operations, management, finance and planning stakeholders had no central hub of information, no ‘single source of truth’, making it difficult – often impossible – to obtain real-time operational information.
Regrettably, this is still the case for many bulk ports and terminals around the world – and TBA continues to evangelise the benefits of a bulk TOS to new customers every year – but there is now wide recognition by the industry that a centralised, consolidated, integrated TOS has huge operational advantages. Adopting a TOS can unlock increased efficiencies, allow for greater automation, and make growth aspirations far more feasible.
TBA’s bulk and general cargo TOS, CommTrac, is now in use in over 40 installations, managing numerous operations throughout the UK, as well as those as far flung as India, Mozambique, Australia, Canada and South Africa, for customers including Associated British Ports, Peel Ports and APMT.
Early beginnings
CommTrac is a sophisticated and hugely scalable product, but it started life as a bespoke inventory management solution developed for a single grain terminal in the UK. Founded in 1976 as a specialist instrument engineering company, DB Controls was commissioned to develop the system for Peel Ports, then known as Mersey Docks and Harbour Company, in Liverpool, UK.
The project primarily involved the installation of a SCADA electrical and control system at nine new grain silos, and this was the first time that the company had experienced any form of digitisation within their operation. The project was a success and directly inspired the development of what would ultimately become CommTrac. As Trueman recalls: “The customer explained that all their inventory management was being done on paper. They saw how the SCADA system we had installed was managing the plant and collecting data, alongside their weighing system, which was also digital. And they asked how difficult it would be to build an inventory management system in the middle?”
And so, the DB Controls team started development of a bespoke solution for the customer. “We lost money on the project because we didn’t know how long the system was going to take to build, but nevertheless we built it. And it worked perfectly!”.
As soon as the system was up and running, it began to attract the attention of other players in the industry. Tilbury Docks faced similar challenges at their grain terminal on the Thames and were interested to explore how the system could be adopted for their use. Meanwhile Mersey Docks had developed a new animal feed store and wanted to expand the system to manage this too. At this point, DB Controls realised that they had something special on their hands. “This very bespoke system we created to meet the requirements of a single terminal was now managing three terminals, and we thought, why stop there?”
The first version of the software was called MOATS - Management Operations And Tracking System. “Our focus at that time was on providing inventory management with a strong influence on traceability of the cargo,” said Trueman. “In the food sector, people were already doing traceability, but we were probably the first to bring it to the raw materials sector.” This focus on traceability proved timely as European legislation was also introduced at this time giving the feature even more relevance.
The launch and development of CommTrac
Following the huge success of these projects and recognising the potential of the software as a commodity tracking system with applications for a wide range of operations, DB Controls made the decision to shift their focus and formed a new subsidiary called DBIS. Thus began two years of intensive development and establishing a fully formed product: CommTrac.
As more and more ports and terminals started to become aware of CommTrac, it provided the opportunity for the product to further evolve to meet additional requirements. Associated British Ports (ABP) enquired if CommTrac could be adopted for use with coal applications. Until this point, CommTrac had only been used to manage grain and feed operations, but the directors saw an opportunity to diversify, especially as there were no other competitors offering their services to the coal sector. This decision paid off as, in 2005, ABP commissioned installation at their Humber International Terminal.
In additional to the bulk sector, CommTrac was increasingly being used for general cargo operations. In another example of the business’s appetite to diversify and meet the needs of a wider user base, a new version of CommTrac was developed. This new version made CommTrac even more versatile and an attractive proposition to customers involved in the transportation of unitised cargo, from break bulk to project cargo. “In bulk, the way that you manage traceability follows a particular logic,” explains Trueman. “There’s a methodology that we developed that was very effective, but you can’t use that for general cargo; it doesn’t work.”
As well as broadening the appeal of the system, the development team took this opportunity to address the architecture and methodology of the software. Instead of a traditional desktop Windows application, a web-based platform was instead adopted. While this software as a service (SaaS) approach is now a very common approach to software development, at the time it was less so, especially in the industry. However, this decision gave CommTrac incredibly solid foundations for further development in years to come.
Adopting a web-based platform further paid off with the ease with which CommTrac could be accessible via mobile devices. Following the introduction of the iPhone in 2007, smartphones have achieved near ubiquity and their application within a bulk terminal environment is obvious to anyone with direct experience of these sites. Interacting with a traditional desktop computer, or even a laptop, is often impractical, and one of the reasons why resorting to paper-based record-keeping remained so prevalent.
The smartphone changes that. On-the-ground employees can use an accessible mobile solution, giving them timely access to information and allowing them to easily document their actions. This can enhance both their personal efficiency and that of the entire operational process. The CommTrac mobile application, introduced in 2016, was designed to prioritise simplicity, ease of use with minimal touchscreen interactions, and wide compatibility with different mobile operating systems and hardware. Key operational areas such as event logging, cargo tallying and scanning cargo barcodes are all perfect use cases for a mobile-based application.
Industry recognition
Last year’s IBJ Special Achievement Award wasn’t the first time the system has been recognised by the industry. The first award was received back in 2004 in the form of the ‘Award for Innovation’ from the US Grain Elevator and Processing Society who recognised the advancement of traceability made available by CommTrac.
In recognition of the system’s impact on the sector, CommTrac went on to win six IBJ Awards, the first in 2010. These have included the 2014 IT Solutions Award for their work with early adopter Peel Ports; the Technology Innovation Award in 2014 in recognition of their work with ABP; and another IT Solution Award in 2018 to celebrate the achievements of the Multi-Site Enterprise Suite.
“While the awards we’ve received over the years are a fantastic opportunity for us to celebrate our team’s achievements,” said Trueman, “the most meaningful recognition for me is the long-standing relationships with have with our customers and the extremely low rate of lost customers. The fact that we are still working with the likes of Peel Ports and ABP over 20 years is testament to the quality of the product, service and the people.”
Acquisition & joining the Konecranes family
As the organisation evolved it became clear that the original founders of the engineering company had been outgrown by their organisation and DBIS was acquired by Demag Cranes to supplement their existing software capabilities residing in the TBA organisation based in Delft, The Netherlands. In 2017 Demag (by then part of Terex) was acquired by Konecranes who have performed the role of parent Company in a way which allows the entrepreneurial spirit of “DBIS” to flourish, whilst satisfying the ever-growing need for corporate compliance and financial governance required to satisfy the needs of our blue-chip customer base.
Looking to the future
As the needs of TBA’s customers evolve, so does the product that supports their operations. “We have a live roadmap which is organic and constantly changing to address the needs of our growing customer base,” said Trueman. The roadmap is influenced by the needs of both longstanding and new customers and how the software can help them be effective in their own businesses. But the development team is also proactive, implementing new features inspired by the latest technology and industry trends. “Meeting and exceeding our customers’ expectations is what motivates us to drive things forward, as well as keeping us ahead of the game. We’re embracing new technologies and looking at how they can be used to further automate some of the decision-making processes and more complex planning features.”
To ensure that they stay focused on the challenges that matter most to their user base, TBA’s CommTrac team ensures that they give their customers every opportunity to provide feedback and suggest how the software can develop. The most effective form of this collaborative approach is the TBA User Group Conference (UGC), the first of which was held in 2012. “The UGC is an incredibly useful and important way to hear directly from our users. The feedback and ideas that have been generated from these events have proved indispensable, and I’m really looking forward to our next UGC 2024 in April.”
When considering the source of CommTrac’s success, Trueman puts it down to not only the outstanding TBA employees who have contributed to the product’s development, but also points to the very origins of the company. “If you’re an engineering company then you don’t understand how to produce software. And if you’re a software company you don’t understand the real-world processes or what’s really important to the customer. The fact that we are an engineering company and a software company means that we transcend those two disciplines and that gives us a deep understanding of what our customer’s needs really are, sometimes before they realise it themselves!”
Share this
You May Also Like
These Related Stories
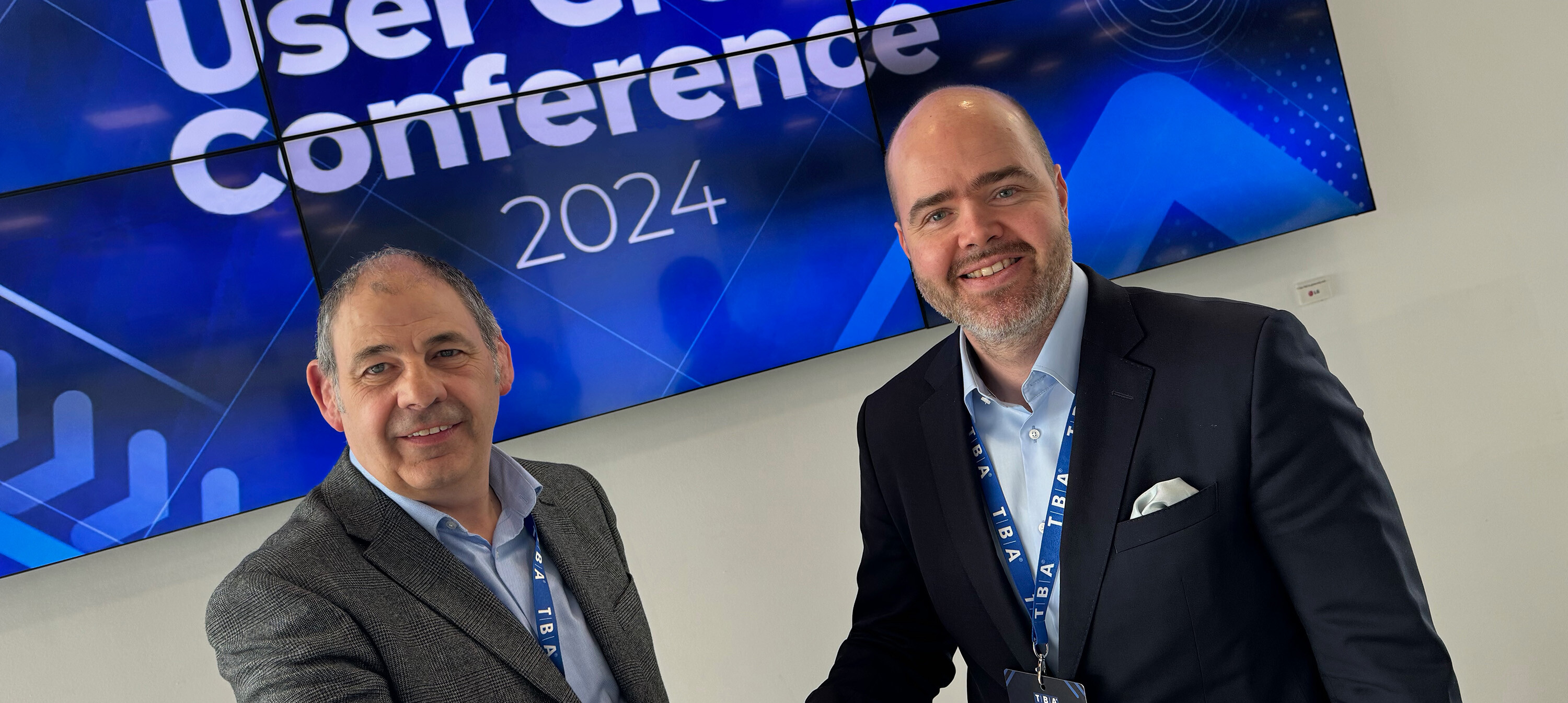
TBA partners with Awake.AI to bring AI-powered vessel ETA times to CommTrac
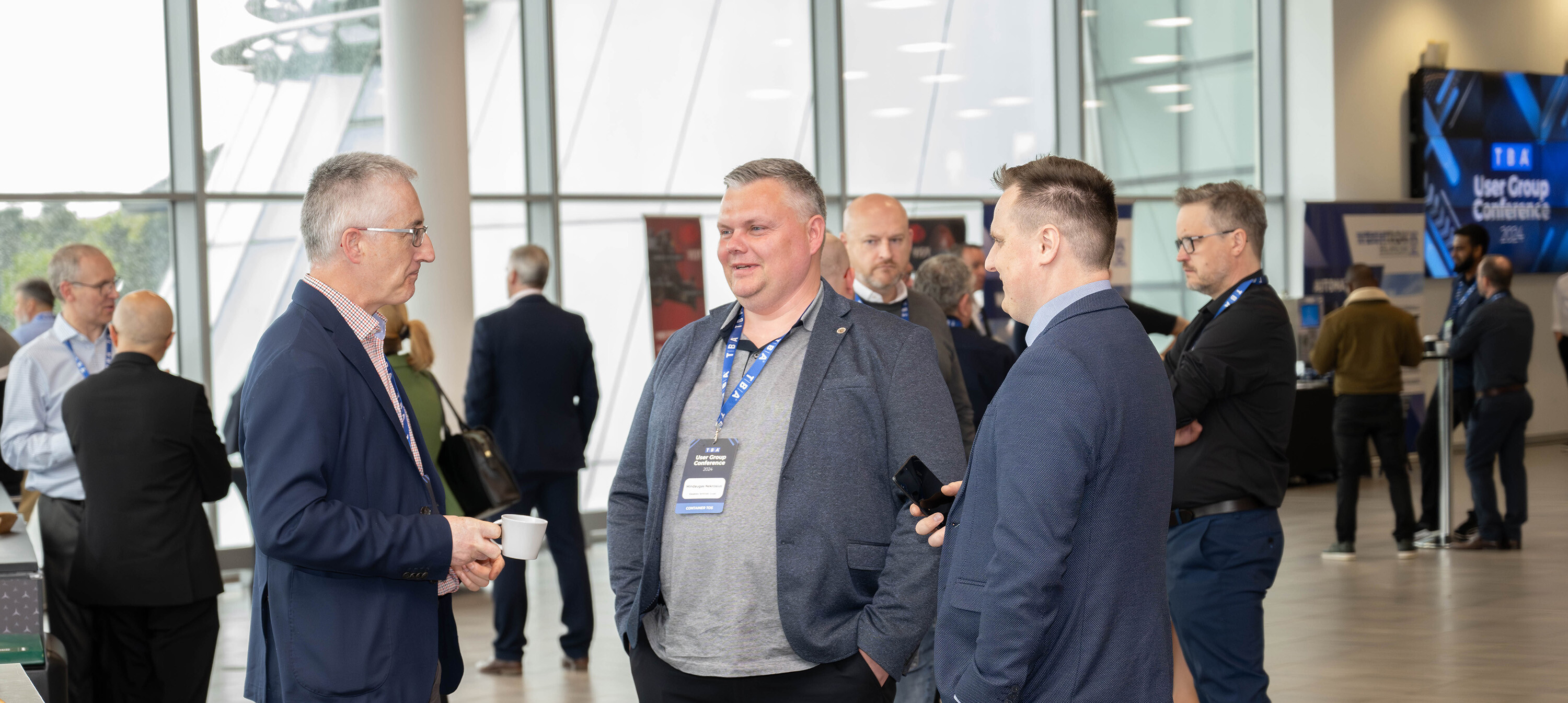
Hugely successful User Group Conference for TBA
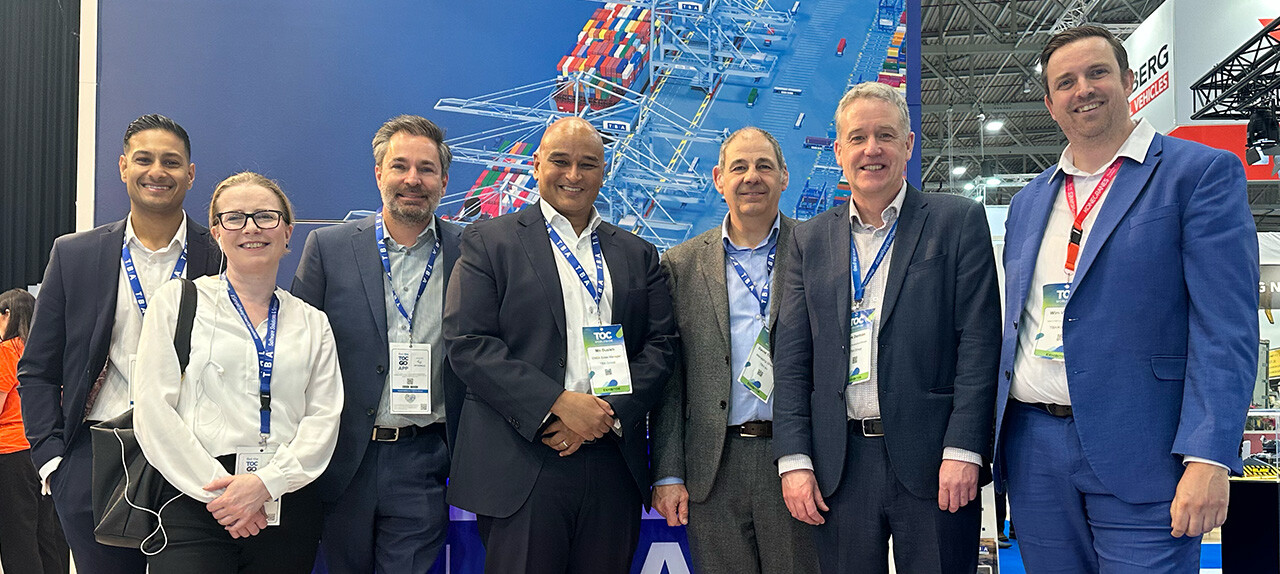