The design and assessment of next generation automated container terminals
One of the answers to the ever-increasing transhipment volumes that are required within the same timeframe at the quays of the world's large container ports, is the automation of the processes. However, until now ECT in Rotterdam and HHLA (CTA) in Hamburg are still the only two stevedores that have fully automated the transport from quay to stack as well as the stacking operations. Both operators have chosen to apply RMGs in combination with AGVs. However, a new automated concept is about to be introduced: the automated lifting vehicle (ALV). In this paper a comparison by means of simulation and cost modelling is made between the operational productivity of an AGV-RMG and an ALVRMG terminal. We will show the pro’s and con’s of each concept and assess the dynamic behaviour in a detailed simulation model. Furthermore, we will compare the two automated concepts with a manually operated shuttle carrier (a 1 over 1 straddle carrier, in essence). The results show that for cost reasons, the ALV should not be preferred over AGVs, although you less vehicles to achieve the same quay crane productivity. Furthermore, ALVs are not yet to be considered as proven technology, which is for most terminals an important criterion to assess the project risk.
Introduction
Since 1991 container terminal robotisation has become the new way of designing terminals with a capacity exceeding 1 mio TEU, providing a cost-efficient alternative for traditional straddle carrier or RTG-TT operations. Although robotisation means that one has to cope with start-up problems – the newly built container terminal in Hamburg (CTA) is a good example – terminal operators cannot longer ignore the benefits of automation, simply because the benefits are making the difference between success and failure.
Until now we have seen two types of robotisation; first the automation of the yard by means of rail mounted gantries (RMGs) and secondly the automation of the horizontal transportation by means of automated guided vehicles (AGVs). Although cost-efficient, the combination of RMGs and AGVs is not considered to be flexible nor highly productive. However, these considerations are not supported by facts, or simulation results. Much is expected from automated straddle carriers, either 1 over 1 or 1 over 0. These automated lifting vehicles (ALV) have the same characteristics as straddle carriers concerning transportation, but do not fulfil the stacking functionality. The stacking is done by RMGs, which leads to a much denser stack than possible with straddle carriers.
The question that will be answered in this paper is whether high expectations regarding ALVs can be justified or not, and we point out the differences and similarities between its main competitor, the AGV. Hereby, we dare to question the general understanding that AGVs cannot be productive. As a benchmark for automation we take the manned shuttle carrier as a reference.
Figure 1: Example layout (true-to-scale) with perpendicular stack modules, operated by dual RMGs and a horizontal transportation performed by either AGVs, ALVs or manned SCs.
The analysis we present in this paper consists of three parts. First we present the results form a comparison of the productivity by means of dynamic simulation. Then, we present the costs of the three alternatives for the horizontal transportation system, and finally we combine the productivity and cost results with a number of other aspects in a multi-criteria analysis.
We take here a fantasy terminal configuration that is, however, representative for the operations in a number of ports in the Le Havre – Hamburg range. The terminal should be capable to handle 2,400,000 containers per year when fully extended. The percentage transhipment is low (<10%) and there is a huge amount of rail moves.
Quantitative comparison
Characteristics of the operation at a robotised terminal
During corridor chat, robotised terminals are labelled “underperforming”. Of course, it is generally accepted that the operational costs are significantly lower, but the perceived lack of waterside productivity, together with a high project risk and an inflexible operation, lead to aversion to automation. Then, there are also the unions, which oppose against the reduction of jobs.
Regarding the current state-of-the-art of robotised terminals, two questions arise: First, what are the key measures that have been taken to get the robotised terminal at a similar productivity level as there manned equivalents? Secondly, we question the perception that robotised terminals are underperforming in comparison with terminals that face similar conditions, such as the calling pattern, the demands from the shipping lines, the labour conditions. We will first deal with the first question, because there are reasons that the productivity at the current robotised terminal is lower than aimed for, or actually attainable.
Improvement measures to robotised terminals
The terminals at ECT (17 QCs, 77 stacks, 150 AGVs) are the example of a robotised terminal. The recent successor at Altenwerder is in principle a similar concept. Both terminals have carried (CTA during the design phase, ECT during the operation) through a number of productivity improving measures to overcome the initial pitfalls of the ECT concept. What are the pitfalls that should be avoided whenever possible? In the following table, we summarise a number of these improvement measures, as they have been tackled in recent improvement projects at ECT and within the terminal design at CTA.
Robotisation: mixture of automation and human control
Robotised systems are in the contrary to manually operated systems well predictable in their behaviour. Machines can reproduce tasks with the preciseness of a Swiss watch, whereas humans tend to vary their behaviour. However, the currently realised automated terminals show a mixture of automated tasks and manually operated tasks. The quay crane driver, the reefer man, or the truck driver serving the rail terminal, are examples of interactions between automated and manual operations. This is one of the reasons that even the operation at an automated terminal is less predictable than one would expect.
Quality of information
A second reason for the occurrence of stochastic behaviour is the lack of quality of the information available. Information about load lists, container weight, PoD, et cetera. This information changes until the container is loaded onto the vessel. Due to these changes, the processes are not as deterministic as one would like.
Table 1: differences ECT and CTA
Equipment failure
The final reason for disturbances is the way fleets of automated vehicles, such as AGVs or ALVs, are controlled is not according to a pre-planning, which means that the real-time interaction affect the reliability of the execution of moves. Also influencing the behaviour of the automated vehicles is the failure rate; not only mechanical failure but software failures as well. These disturbances disrupt the operation and demand for quick intervention.
Figure 2: Visualisation from the (simulated) control system of the collision manager. The green rectangles are the transfer locations; above the transfer points at the RMG, below the transfer points at the QC. The red rectangles are the space reserved for each AGV. The black rectangles are the AGVs. The difference between the two pictures is the curve-behaviour of the AGVs; the above picture shows optimised space reservation behaviour, below the standard behaviour that causes more interference between AGVs.
The (mis)perception of underperformance
Most traditional operators and shipping lines point at the robotised terminals and address them as underperforming. This perception originates from the initial start-up problems that robotised terminal have; more than manually operated terminals. However, it is our opinion – given the actual numbers in the range Le Havre – Hamburg – that after the start-up phase is more perception than fact, that the automated terminal perform less than there manually operated competitors. All numbers of gross quay crane productivity vary between 22 and 30 containers per hour. Of course, the magnificent productivities that are registered in Asia and the US are not met, but they are not met anywhere in Europe! Furthermore, when benchmarking those productivities (gross often above 40 containers per hour) the specific local conditions have to be accounted for. Smaller terminals, lower berth occupancy, no acceptance of late arrivals, gate closing times during the night; all circumstances that enable terminals to prepare for the upcoming operation. In most terminals in Europe, these conditions are not met.
Therefore, one should be careful in writing robotisation off because of the perceived inability to deliver appropriate service. When the conditions are right, the information is at a sufficient level, robotised terminal may even perform better than their manned equivalents, because the cost of preparation (i.e. housekeeping) is so much lower, and therefore, more easily done. Therefore, under similar conditions, three alternative systems will be compared by means of simulation.
Modelling the operation at a robotised terminal
The first step of our quantitative analysis consists of dynamic simulation of the three waterside handling systems. In order to analyse these systems in detail, we reckon that a simulation model is required that contains a fair depiction of the process control system, since it affects the performance of the transportation system and the yard handling system. It also deals with the stochastics mentioned earlier; by means of planning and real-time re-planning, taking the latest information into consideration. We state that any automated system can be made or broken by its process control system.
The following rules should at least be considered when comparing a system with AGVs and ALVs to express the different characteristics of the vehicles:
- Order planning (to estimate the handshake moments at RMG and QC).
- Job assignment (which vehicle or crane will perform which transportation or stacking job?).
- Transfer point management (assignment interchange points at the QC and RMG to AGVs or ALVs).
- The transfer protocol at the transfer points: interference between RMG and ALV/SC (traffic lights!) and between QC and ALV/SC. Also the landside transfer protocol (managed by remote operators) is relevant for the waterside operation.
- Sequence control (managing the sequence of containers under the QC).
- Collision and deadlock avoidance (making sure that the vehicles do not collide; AGVs use less space than ALVs).
- Dynamic routing - layout management (determining realistic and efficient routes for the vehicles).
- Dual cycling procedures (under the QC).
We developed a simulation model that contains these rules. The entire set of rules is very close to a real implementation in a process control system (PCS).
Besides a valid representation of a PCS, the simulation model had to contain a valid representation of the equipment, i.e. the QCs, the AGVs, the ALVs, and the RMGs. In close co-operation with equipment suppliers, these equipment models were developed and verified. Validation has been done by means of animation (partly 3D, in the case of the RMG) and by means of statistical analysis of the results.
Simulation scenarios
In order to make a sound comparison we used two types of scenarios. The first scenario can be classified as a peak scenario, representing an operation that is likely to occur during less than 5% of the time (which means approximately 400 hours per year). Based on this scenario, we can determine how much equipment is required to meet the productivity requirements. The second scenario can be classified as a busy but regular operation. Based on this scenario, we can determine which type of system performs better. Of course, this can also be determined based on the first scenario, but this is a seldom case; we prefer to assess the quality of the handling system based on the average situation. The two scenarios are defined as follows:
- The peak scenario consists of a demand on the waterside of 17 dual hoist deep-sea cranes and 3 single hoist barge cranes. The landside load – consisting of trucks serving the rail terminal and hauliers – is 455 moves per hour (mph). The stack filling rate is assumed to be an initial 80%. The filling rate, however, will vary throughout the simulation run as a result of the ongoing operation.
- The average scenario consists of a demand on the waterside of 9 dual hoist deep-sea cranes and 4 single hoist barge cranes. The landside load – consisting of trucks serving the rail terminal and hauliers – is 270 moves per hour (mph). The stack-filling rate is assumed to be an initial 70%.
The main output of the simulation consists of the following parameters:
- Waterside productivity level in moves per hour (mph).
- Landside service time of trucks on the interchange points in minutes.
- Equipment productivity on water- and landside, respectively of the transportation vehicles in moves per hour (mph), and the RMGs in mph.
All results will be gathered for various amounts of equipment. More detailed results can be acquired, but are not relevant for the final decision-making.
Results
As is shown in Figure 3 and Figure 4, the productivity of the three systems, manually operated shuttle carriers (SC), ALVs and AGVs reaches almost the same level. However, the productivities are reached with different amounts of equipment, with a slight benefit for the manually operated shuttle carriers in the peak scenario, and a similar benefit for the AGVs in the average scenario. A general rule could be that for the same performance, one needs either 3 shuttle carriers, or 4 ALVs or 5.5 AGVs per QC.
We also found that the dual-RMGs are perfectly capable of serving both the waterside end and landside end with an acceptable service level (average service on the landside 10 minutes). However, to reach a productivity level of approximately 24 (productive) moves per hour per stack module, the RMGs have to co-operate with each other. This means that in busy times on the waterside, the landside RMG has to support the waterside RMG and vice versa. This support consists of bringing export containers closer to the waterside (prepositioning) or executing shuffling moves for the other crane. Furthermore, it appeared to be important that the RMGs have a large enough look-ahead, to be able to cope with peaks. Doing so enables the RMG to execute shuffles in advance, so that the productive move can be performed faster at the time a peak occurs.
Figure 3: Waterside productivity in peak scenario; on the horizontal axis the number of transportation vehicles is depicted; on the vertical axis the realised net QC productivity in bx/h.
Figure 4: Waterside productivity in average scenario
A critical point in all three handling systems is caused by the limited handling capacity of the RMGs. Because they can only serve over the top ends of the stack modules, the handling capacity per stack is limited in comparison with for instance an RTG or straddle carrier operation, in which it is possible to assign more equipment to the same stack to increase the handling capacity. During loading of the vessel (or loading trucks) peaks that exceed the handling capacity occur in the stack-handling load, which causes delay in the vessel loading process. Because principally all QCs can be loaded from a certain stack, this can influence the service to many QCs at the same time. This effect can be reduced by category loading – exchanging containers with similar characteristics – or flexible loading – realtime changes in the vessel stowage plan. These measures can lead to a better spread over the stack modules in time and thus to an improvement of the QC productivity (up to 15%), but heavily depend on the cooperation of shipping lines and captains.
Cost comparison (see table 2)
When productivity and service levels are one side of the picture, then investment cost and operational cost are the other side. Therefore, to complete the comparison, we developed a cost model consisting of the main cost drivers of the waterside transportation systems. Here, we leave the other system components out of the comparison, because they are to a very high degree equal. Of course, there are differences, for instance at the transfer points of QC and RMG, but the related costs are considered minor compared to the operational cost differences. Further examination into these aspects will provide more insight.
The cost comparison is built on three components:
- Personnel cost involved with the manning of the SCs.
- Cost of capital involved with the investment in transportation equipment.
- Cost for maintenance and repair of the vehicles
In table 2, the cost calculation is shown. Note that only the cost involved with the waterside transportation system are included. The costs are calculated per QC. In order to determine the operating hours of the transportation vehicles, we start with the planned annual productivity of the QC, i.e. 100,000 containers. With an assumed gross productivity over the year of 35 containers per hour, this leads to 2,857 operating hours per QC. The number of vehicles required originates from the simulation; we took the required number of vehicles so that in the peak scenario a net productivity of 35 bx/h could be achieved, which means 2.5 manned SC/QC, 4 ALVs per QC and 5 AGVs per QC. These vehicles are assumed to deliver in an average scenario 35 bx/h gross.
Personnel cost SC manning
Since the QCs are served by 2.5 SCs on average 2.5 times as many operating hours for the manned SCs are required, i.e. 7,143. However, due to working shifts, the actual number of hours that the SCs are manned will be higher, approximately 10% higher, leading to the 7,857 SC manning hours per year per QC. For this approximately 7 people are required (based on the assumption of 1,200 working hours per year), which cost around 60,000 Euro in North-Western Europe and at least 100,000 Euro in the United States. This leads to the item “variable cost personnel”. For the unmanned vehicles no people are needed that are not needed in the manned situation, e.g. the process control operators have to be present in both cases.
Cost of capital
The second cost component is the depreciation cost (linear depreciation over the life cycle; i.e. 10% per year) of the investment combined with the average interest (0.5 x common interest level of 8%).
Maintenance and other operational cost
The third component is the cost for maintenance, repair, and other variable costs (mainly fuel). The operation with AGVs is assumed to be cheaper regarding maintenance and repair, because of the absence of a hoisting machine and spreader. Furthermore, the automated operation is assumed to be safer (less accidents) than with a driver.
Results
The three components add up to the total variable costs per QC per year. Divided by the number of container lifts, the cost per container move results. As a result, the AGV is by far the cheapest per container move; even with the high price of an AGV. The ALV is a good second (however, it depends on the actual prices when this vehicle is brought onto the market) with approximately 1 Euro per container move more (for a terminal like this one, this means 2,400,000 Euro on a yearly basis!). The manned SC is by far the most expensive operation, also with European labour costs. In order to reach the cost per container move of an AGV, the labour cost should sink to less than 15,000 Euro per year (12 Euro per hour).
Table 2: Cost comparison of waterside transportation systems
Qualitative comparison
Besides productivity and costs, there are a number of other aspects that should be considered when investing in equipment. These aspects, completed with productivity and costs are presented in table 3. The first aspect is the risk that is inherent to the type of operation. It covers the degree to which the equipment is proven, and the complexity of the process control software. The second aspect is the complexity of the operation, which covers issues like sensitivity for breakdown, redundancy of equipment, degree of decoupling within the operation, and feasibility to transform into manual operation. Other aspects of importance, such as environmental aspects are not taken into consideration because they are assumed to be equal for all waterside transportation systems. Given the specific characteristics of the three concepts, ALV, SC and AGV, we come to the following assessment:
Table 3: MCA of alternatives waterside transportation systems
Cost and investment of the three systems have been discussed already, as is the productivity. Because the cost calculation of performed at a equal productivity level, there are no difference here.
The project risk is a theme of increasing importance, and extremely relevant in the case of automation. First due to the increasing scale of terminals, the financial risk is increasing. Secondly, due to the automation and the tendency to apply RMGs rather than straddles carriers or RTG, increases the investment volume, which increases the risk as well. Thirdly, the dependency on software affects the project risk in a negative way; the commissioning of manually operated terminal is simpler than of an automated terminal, mainly due to software problems. The risk with manned SCs lies in the connection to the automated RMGs; the link between a manual operation and an automated one, can better be avoided and therefore the risk is at a similar level as with the AGV system. This system is proven at ECT and CTA, where most initial complexities have been solved. However, this is not the case for ALVs, which cannot be considered as proven technology. Although there is an operation with automated straddle carriers in Brisbane, this cannot be compared to the dense operations at ECT or CTA. Especially the collision avoidance in this application is too simple for a dense operation. Furthermore, a machine that has to pick-up a container by itself is more difficult to automate than a machine that does not more than drive from A to B, as the AGV does.
Although important, the risk of automation is decreasing because of a number of developments:
- The supplier market of robotised solutions is steady growing with the increased interest for this kind of solution.
- There is more and more experience with the design, realisation and commissioning of robotised terminals.
- The software is increasingly mature, and the big terminal control software providers are now developing components for controlling automated operations as well.
- A simulation based approach, using similar models from initial design to final commissioning increases insight (also for non- experts) and shortens the feedback loop.
The final criterion is addressed as system complexity, covering the flexibility of the operation, he redundancy within the concept, and the sensitivity to disturbances and breakdowns, Here, the manually operated concept is clearly beneficial compared to the automated competitors: due the fact that late-minute changes still can be coped with by the drivers, the flexibility is high and the vulnerability to disturbances of relatively low. Of course, all concepts depend on the service by the RMGs and have no possibility to access containers in the yard themselves. However, during the transportation process, the lifting vehicles can easier take over jobs of vehicles with a failure. The container is put down and taken over by another vehicle. In the case of AGVs, this is not possible.
In conclusion, one can say that each concept has its pro’s and con’s and the final assessment depends on the weight of certain criteria. In most terminals the cost per move and the investment volume are crucial, but aspects such as environmental impact are of increasing importance.
Conclusion
Is the 1 over 1 automated lifting vehicle – or automated shuttle carrier - the productivity bringer when compared to AGVs? No. Nor will it lower the investment costs. This simple answer can be made after a detailed comparison between an RMG-AGV and an RMG-ALV operation. Although the latter combination can do with less equipment because of the decoupling between RMG operation and ALV operation, the cost advantages of AGVs over ALVs compensates the bigger amount of equipment.
In addition, we have to say that the AGV is proven technology, whereas the ALV is not. It is a vehicle more complicated to automate, and certainly more expensive regarding operating costs. Finally, since the spreader is the most vulnerable component, we should try to reduce the number instead of increasing it.
When looking at the state-of-the-art layout with twin RMGs and AGVs, we have to conclude that the system’s potential is hindered by the inflexibility in the operation and the poor information available to the terminal. To utilise this concept’s potential to a maximum, shipping lines should agree with flexible loading and provide terminals with accurate information well in advance. Only then, we see the possibility to increase productivity on a constant basis to numbers in the range of 45 to 50 lifts per hour.
When the two automated concepts are compared to the manned 1 over 1 straddle carrier, the conclusion must be that although the project risk may be higher, the overall cost of the automated alternatives is significantly lower than of the manned alternative. With a difference in cost per move of approximately 3 Euro, the additional investment pays back after 100,000 QC moves. Therefore, our conclusion is that robotisation pays off and is the right concept for the future.
Share this
You May Also Like
These Related Stories
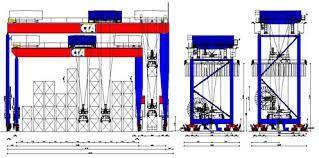
Comparison of three automated stacking alternatives by means of simulation
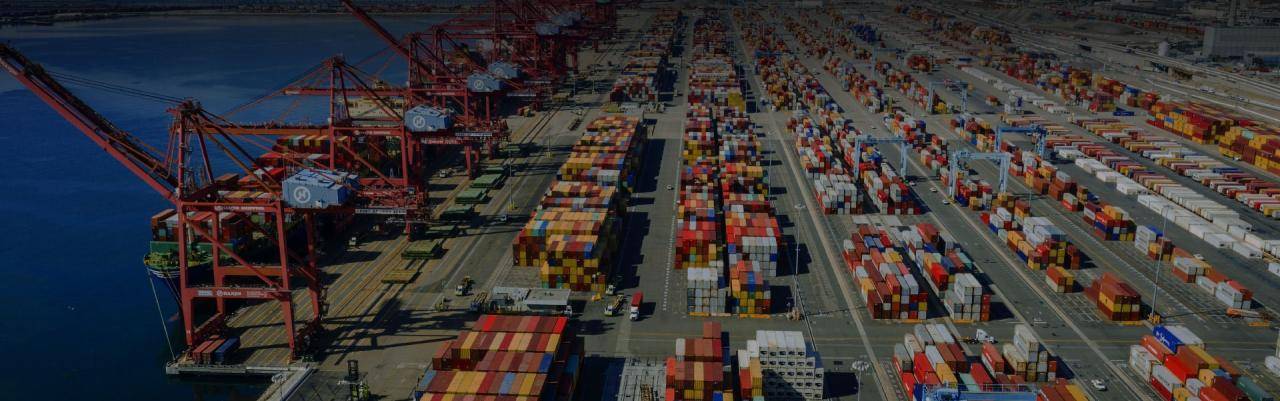
How can simulations help ports and terminals?
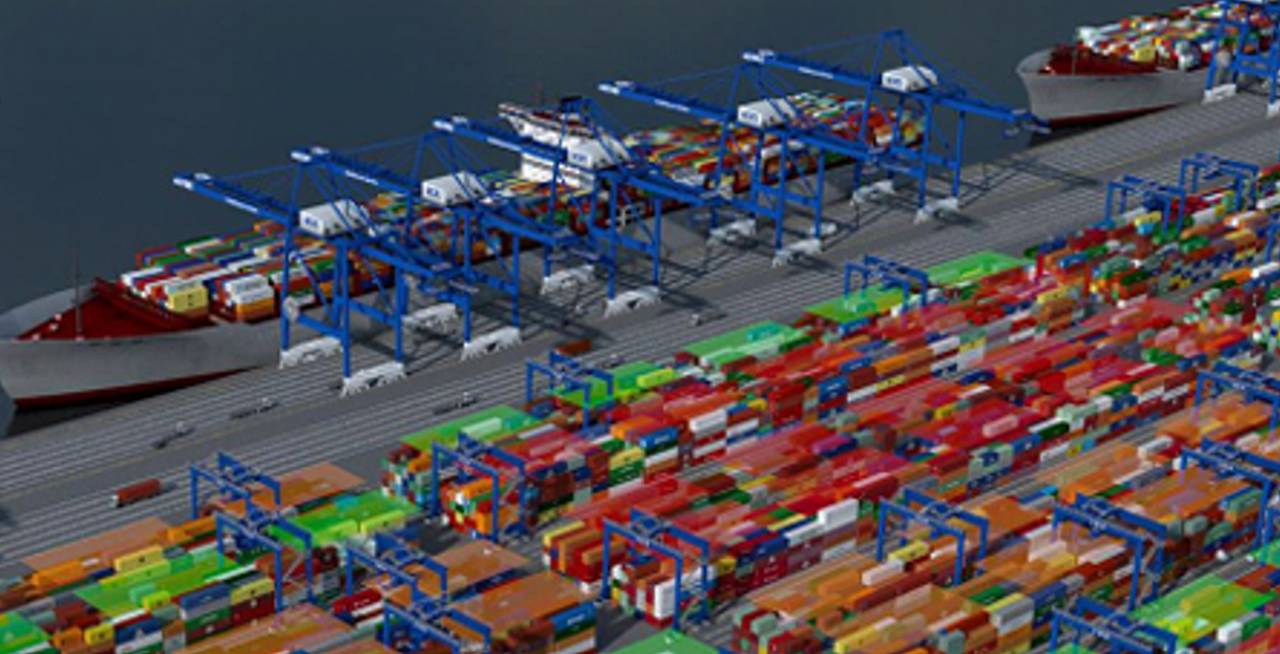