Comparison of three automated stacking alternatives by means of simulation
One of the answers to the ever-increasing transhipment volumes is increasing the yard density. As we have seen in the recent past, there are multiple solutions. One of them is the manned RTG. An alternative is the Rail Mounted Gantry crane (RMG). However, when selecting an RMG, what is the best configuration? So far, we have seen the automated RMGs at ECT (Rotterdam) – 6 wide, one RMG at a stack module –, at CTA (Hamburg) – 10 wide, two RMGs at a stack module, able to pass each other. Recently, there are several terminals considering automated RMGs. Here, we put one of the considered designs for the new Euromax Terminal in Rotterdam at stage – 10 wide, not able to pass each other. All three concepts aim at the same: high density, high productivity for both waterside and landside, and low cost (both labour and maintenance). Three concepts aiming at the same goal, but they are still so different? In this paper we will compare the three concepts on their efficiency in terms of productivity, flexibility, area utilisation, and cost to come to a verdict: what is the best automated RMG concept yet existing?
1 Introduction
1.1 Pursuit for intensifying yard operations
As container volumes keep increasing, new container terminals are being built and other terminals – in particular those that cannot easily extend their area – aim at increasing the density of the stacking yard. Especially terminals with low density stacking systems (straddle carriers or a wheeled stack), have the opportunity to put more volume through with the same area of land. After all, straddle carrier operations typically have densities around 500-600 TEU/ha, where RTG operations achieve 900 - 1,100 TEU/ha and RMG operations can achieve over 1,200 TEU/ha. This means that without acquiring additional land, a terminal can put through twice as much volume through an RMG terminal. Of course, this also depends on the available quay length and the vessel productivities – otherwise, the berth may become the bottleneck – but in general this is true.
Besides, RMG operations lend themselves very well for yard automation, which is interesting from a cost perspective. ECT in Rotterdam and CTA in Hamburg (but also Thamesport), are two examples of yard automation in Europe, that prove the feasibility of the concept. And more will follow. One of the terminals planning to develop an automated RMG yard is the new Euromax terminal in Rotterdam.
1.2 Solutions for high density yard cranes
Having these three terminals mentioned, one questions remains unanswered: although all three terminals are quite similar – in terms of the containers flow: all of them are large import/export terminals, in terms of the size: all of them aim at volumes over 1 million containers per year, in terms of terminal depth: all use around 500 meters of depth, in terms of the waterside transportation system: all of them use AGVs, in terms of the modal split: all of them have both a large share of truck and barge, and in cost structure: all of them operate in a high labour cost environment – the selected design of the RMG yard is quite different.
Starting with the oldest design: at ECT the RMGs are 6 wide, and have a varying height (oldest are 1 over 2 high, newest are 1 over 4 high). The length of the stack modules varies between 28 and 42 TEU. A single RMG operates the stack modules and serves both waterside (interchange with AGVs) and landside (interchange with SCs). The RMG is capable of 4 m/s gantry speed. The stack module width is 23.7 m.
The CTA design is quite different: on each stack module there are two RMGs, one 10 wide, 1 over 4 high, the other one 14 wide and 1 over 5 high. The length of the stack module is 44 TEU. At the waterside, the RMGs interchange with AGVs, at the landside with road trucks and terminal chassis. The small RMG is capable of a gantry speed of 4.0 m/s, the large one 3.5 m/s. The stack module width is 42.5 m.
Figure 1: Cross section of the RMGs at CTA (Source: Koch, 2002).
As the Euromax terminal is still being designed, we put one of the possible designs on stage: one with two similar RMGs on a single stack module, each 10 wide. The stack module width is 36 m. Both RMGs are 1 over 4. At the waterside, the RMGs interchange with AGVs, at the landside with road trucks and terminal chassis. The RMGs are capable of a gantry speed of 4.0 m/s.
1.3 Methodology of assessment of the three yard crane concepts
In this paper, we try to assess the three alternative RMG designs on their merits. Therefore, we have developed a terminal simulation model, containing all operations between the waterfront, the gate, and the rail terminal. The waterside transportation is by means of AGVs, the landside operation is direct, which means that the RMGs handle the road trucks and rail chassis directly under the RMG. This deviates from the ECT concept, but makes the comparison between the three yard cranes easier.
The comparison we present in this paper consists of three parts. First we present the results form a comparison of the productivity by means of dynamic simulation of one isolated stack module (with one or two RMGs). Each module is of the same size and gets the exact same set of moves to be executed. Only the crane configuration is different.
The second part of the comparison comprises a dynamic simulation of an entire terminal operation, where the only difference is the three alternative yard crane designs. The available surface is similar in all three cases, i.e. a quay length of 300m and a terminal depth (excluding space for gate and on dock rail of 500m. The quay cranes are common single hoist quay gantry cranes, the horizontal transportation is by means of AGVs. The three yard crane designs will be tested under two different operational scenarios, one stress test, where waterside and landside operation are both at their peak level and an operational scenario where there is a heavy waterside operation and a quiet landside operation. These two operations are specified in section 0. The third part of the comparison concerns other aspects related to the yard crane design: throughput capacity (mainly determined by the attainable yard density), costs (investment and operational), and flexibility of the concept (for instance in case of break-down situations).
1.4 Outline of the paper
The outline of this paper is as follows. First, we will review literature with regard to yard crane design and high density stacking. Secondly, we will elaborate on the three alternative yard crane designs, especially focussing on the control software that operates the one or two cranes on a single stack module, and the software that determines which stack module will handle which move. Secondly, we will discuss the results of the simulation experiments for all scenarios. Subsequently we will discuss the other relevant aspects when assessing the alternative yard crane designs.
2 Literature review: high density stacking
A broad range of research has been done on container terminal stack yard operations, in order to improve efficiency. Though few focus on assessing different automated container terminal design concepts on behalf of their stack yard design. Below, we present a brief overview.
Chin-I. Liu et al. have developed a simulation model to simulate all operations of an automated container terminal (ACT) in order to compare 4 different concepts by means of performance and costs. The concepts issued are a terminal where AGVs used in combination with stack yards served by one RMG, a terminal where a linear motor conveyance system is combined with stack yards served by one RMG, a terminal where AGVs used in combination with an overhead grid rail system fop stacking and a terminal where AGVs used in combination with a stack and storage system with a rack structure. They found the AGV-RMG concept to be the most cost effective.
Kim et al. suggest operational rules for crane dispatching and container allocation for automated container yards with crossover RMGs.
Kozan provides a comparison of analytical and simulation planning models of container terminals. He uses simulation to observe the effects of changing values for critical parameters and compares the results of the analytical and simulation approach.
Kozan and Preston provide a model where storage strategies and container handling schedules are determined in order to minimize berthing time. Therefore they want to minimise the sum of setup times, where setup time described as the time necessary to remove the containers on top of the desired container.
Meersmans and Wagelmans investigated the scheduling problem of handling equipment in an automated container terminal. They used a beam search algorithm and proposed a way of using it in a dynamic setting. Results were compared with results of rules for dispatching, adjusted for this particular environment in order to avoid deadlocks. They found better performance for the beam search algorithm with the results of the beam search algorithm in the static environment as a benchmark.
Kim and Kim discuss the problem of routing yard-side equipment by introducing heuristic algorithms to determine a pick-up schedule, minimizing the container handling time. However, containers are transferred at the side of the block and not at transfer points on the end, which makes a great difference to travel times of the yard cranes.
Vis provides a model and solving heuristic where empty travel distance is minimized for stack yards operations. An extensive literature overview is given. We have not found any comparisons between the three different RMG designs in the studied literature, although we have found many leads for implementing our RMG control rules, especially in the case of more than one RMG on a stack module.
3 The three alternative yard crane designs
3.1 The first: single RMG
As already stated earlier, at ECT the stack modules are 6 wide and
equipped with one RMG per stack module. In the comparison
made here, the following configuration has been used:
- 12 stack modules 40 TEU long (260m), 6 containers wide, with on both sides an interchange zone (each 30m), for interchange with trucks at the landside and for interchange with AGVs at the waterside. The waterside interchange zone contains 4 transfer points for AGVs; the landside interchange zone contains 4 transfer points for road trucks or rail chassis.
- RMGs 4.0 m/s gantry speed, 1.0 m/s trolley speed, hoist speed 0.5 - 1.0 m/s (load dependent). Simultaneous gantry and trolley movements. Dead times between movements: 2 seconds. Positioning time on a truck: 30 seconds, positioning time on an AGV 10 seconds.
- The RMG control divides the priority between landside and waterside moves based on their due time. The due time of a truck (landside) is 10 minutes after arrival at the interchange zone. The due time of an export move (load move to the quay crane) is based on the planned timeline of the quay cranes (QC) and the planned driving time of an AGV from that interchange zone to the particular QC The timeline is based on a delivery each 80 seconds. Import moves are due 15 minutes after arrival at the interchange zone.
- The RMG control tries to equalize the workload over time. When there is significant idle time in between moves, the RMG may perform preparation moves or perform shuffling in advance. This will decrease the duration of productive moves at a later point in time, when the workload is higher.
3.2 Latest development: cross-over RMG
The configuration with cross-over RMGs consists of the following configuration:
- 7 stack modules 40 TEU long (260m), 10 containers wide (module width 42.5m), with on both sides an interchange zone (each 30m), for interchange with trucks at the landside and for interchange with AGVs at the waterside. The waterside interchange zone contains 5 transfer points for AGVs; the landside interchange zone contains 5 transfer points for road trucks or rail chassis. RMGs 4.0 (small) / 3.5 (large) m/s gantry speed, 1.0 m/s trolley speed, hoist speed 1.0 - 1.5 m/s (load dependent). Simultaneous gantry and trolley movements. Dead times between movements: 2 seconds. Positioning time on a truck: 30 seconds, positioning time on an AGV 10 seconds. Both RMGs can serve either side.
- The passing of RMGs is such that the trolley of the large crane has to be in the passing location (see Figure 1). This passing takes place preferably on the fly, without an RMG slow-down.
- The additional lane where AGVs can drive into the stack is not used, as it is also not used (yet) at CTA.
- The RMG control divides the priority between landside and waterside moves based on their due time. The due time of a truck (landside) is 10 minutes after arrival at the interchange zone. The due time of an export move (load move to the quay crane) is based on the planned timeline of the quay cranes (QC) and the planned driving time of an AGV from that interchange zone to the particular QC The timeline is based on a delivery each 80 seconds. Import moves are due 15 minutes after arrival at the interchange zone.
- The RMG control tries to divide the moves over the two RMGs as efficient as possible. Aims here are the minimisation of travel distance of the RMG in combination with the fulfilment of the move due times.
3.3 Future development: twin RMG
The configuration with twin RMGs consists of the following configuration:
- 8 stack modules 40 TEU long (260m), 10 containers wide (module width 36m), with on both sides an interchange zone (each 30m), for interchange with trucks at the landside and for interchange with AGVs at the waterside. The waterside interchange zone contains 4 transfer points for AGVs; the landside interchange zone contains 4 transfer points for road trucks or rail chassis.
- RMGs 4.0 m/s gantry speed, 1.0 m/s trolley speed, hoist speed 1.0 - 1.5 m/s (load dependent). Simultaneous gantry and trolley movements. Dead times between movements: 2 seconds. Positioning time on a truck: 30 seconds, positioning time on an AGV 10 seconds. The landside RMG serves the landside, the waterside RMG serves the waterside. Eventually moves can be split into two partial moves, performed by both RMGs sequentially.
- The RMG control divides the priority between landside and waterside moves based on their due time. The due time of a truck (landside) is 10 minutes after arrival at the interchange zone. The due time of an export move (load move to the quay crane) is based on the planned timeline of the quay cranes (QC) and the planned driving time of an AGV from that interchange zone to the particular QC The timeline is based on a delivery each 80 seconds. Import moves are due 15 minutes after arrival at the interchange zone.
- The RMG control tries to divide the moves over the two RMGs as efficient as possible. Aims here are the minimisation of travel distance of the RMG in combination with the fulfilment of the move due times. The additional constraint here is the limitation to serve one side for each one of the RMGs.
4 Simulation scenarios
4.1 The isolated stack module
To be able to compare the productivity of only the different crane configurations, we first observe one isolated stack module (with one or two RMGs). Isolated means in this case that no further attention is paid to the planning of the other processes happening in the terminal. In this way that planning does not influence the productivity of the RMGs. To be able to make a good comparison of the productivity of the crane configurations, experiments are done with the exact same order list.
For the experiments the following assumptions and decisions have been made:
- The order list used is created according to the known statistics of the distribution of retrieval and storage containers in stack and necessary reshuffle moves.
- Each container retrieved from stack is directly accessible.
- Each container retrieved or stored can be interchanged directly at the interchange zone, where no time is lost at interchanging.
- There is always a new order available when finishing an order, on both landside and waterside.
- The size of the stack and the filling at the start is the same in all cases; this makes an exact same order list possible. Only the RMG configurations differ. The size used is 49 TEU long, 8 containers wide and 4 containers high.
The experiments will be done with the three earlier mentioned RMG configurations: one RMG, twin RMGs, and cross-over RMGs.
For the RMG control, a standard scenario and a heuristic will be tested. The standard scenario consists of handling the orders in the order of the order list as created. The heuristic however, aims to reduce empty travel distance. For this matter the ‘nearest neighbour’ heuristic is used. Every time when a RMG finishes its order, an order is chosen from the first five orders available in the order list, with its pick up location closest to the current location of the RMG. Five seems a rather small number. But when we take into consideration the normal situation where a stack is functioning within the planning of the complete terminal, we see that the RMG does not have so many options more either. When you try to reach due times according to the load plans of the QCs, not just any order in the order list can be done at any point of time, here with decreasing the set of feasible moves. From that perspective, choosing out of five orders seems a realistic choice. For the twin RMGs the dispatching of loading and unloading orders is done by waterside and landside. Since they cannot crossover, each of them can only serve one of both sides. For the cross-over RMGs we will perform an additional experiment where waterside and landside orders can be dispatched to both cranes. The dispatching in this experiment is done according to the heuristic, since without the heuristic long empty travel distances will occur when travelling all over the stack.
The main output of the simulation consists of the productivity level expressed in orders per hour. Besides this level we are interested in the delays caused by interference of the RMGs in case served by two. A delay is determined by the difference between the realised cycle time and the minimal cycle time needed to execute the order, based on the crane's kinematics. Clearly any delay is unwanted, since terminal planning is based on predictions of cycle times, so delays can undermine this planning. Examples of such delays are with twin RMGs when one RMG has to make space or slow down for the other RMG, in order to avoid collision. Since the cross-over RMG has to move its trolley to the side before it can take over the other RMG, a delay is caused here when this move is not finished before reaching the other RMG.
4.2 The entire terminal
For the entire terminal simulation, we used a model applied and validated in many studies. We refer to Saanen and De Waal (2001). With regard to the model, we refer to Saanen (2004), because it is beyond the scope of this paper to discuss all ins and outs of this comprehensive model here. In brief, it consists of a detailed representation of a terminal control system responsible for planning, scheduling, dispatching, and monitoring, and detailed representation of the equipment system, including the functionality to route AGV, avoid collisions and deadlocks.
In order to make a sound comparison we used two types of scenarios for the entire terminal operation. The first scenario can be classified as a peak scenario, representing an operation that is likely to occur during less than 5% of the time (which means approximately 400 hours per year). The second scenario can be classified as a busy but regular operation. The biggest difference is the balance between the waterside load and the landside load: in the first scenario it is both at capacity; in the second scenario, the waterside operation is at capacity, but the landside operation is quiet.
The two scenarios are defined as follows:
- The peak scenario consists of a demand on the waterside of 4 single hoist deep-sea cranes able to operate at 40 cycles per hour. The landside load – consisting of trucks serving the rail terminal and road trucks – is 80 moves per hour (mph). The stack-filling rate is assumed to be an initial 70%.
- The average scenario consists of a demand on the waterside of 4 single hoist deep-sea cranes able to operate at 40 cycles per hour. The landside load – consisting of trucks serving the rail terminal and road trucks – is 20 moves per hour (mph). The stack-filling rate is assumed to be an initial 70%.
The main output of the simulation consists of the following parameters:
- Waterside productivity level in moves per hour (moves/h).
- Landside service time of trucks on the interchange points in minutes.
- Equipment productivity on water- and landside, respectively of the transportation vehicles in moves per hour (mph), and the RMGs in moves per hour.
- The truck handling time at the stack module, measured from arrival until ready to depart.
All results will be gathered for various amounts of
equipment. More detailed results can be acquired, but are not
relevant for the final decision-making.
5 Results of the simulations experiments
5.1 Results isolated stack module
When we look at the results obtained for the productivity of the different isolated stack modules as presented in Figure 2, we see that the stack module with only one RMG has the lowest productivity. Since the RMG has to do all orders on both sides, this is not surprising. We see the productivity increase with almost 30% when the heuristic is used. The twin RMGs and the cross-over RMGs reach a double as high productivity. Disconnecting the cross-over RMGs from a transfer point doesn't increase the productivity of the stack at all. An even lower productivity is retrieved when doing the orders as put in the order list. An explanation will be opposed for this later in this paragraph.
For the stack modules with two RMGs no difference is found between the twin RMGs and the cross-over RMGs. This is rather surprising since the cross-over RMGs are expected to suffer less of long delays caused by interference. For example: an RMG never has to make space for the other RMG by moving far away from its target. However, passing also takes time, because the trolley cannot always move aside at full gantry speed.
Figure 2: Productivity of isolated stack with the different crane configurations
Figure 3 the delay characteristics of both dual crane configurations are shown for one simulation run. They are calculated from a 24 hour simulation run in which over a 1,000 orders are handled in the standard order. They represent the differences we found in general for the behavior of the delays for the two crane configurations.
Figure 3: Properties delays for twin RMGs and crossover RMGs.
What we see is that there is very little difference between the average delays. This explains how it is possible that the same productivity is found for the two different configurations. However we see a big difference in the maximum delay. In general, fewer orders are delayed with the twin RMGs but the standard deviation is higher, so the values of delays are more spread out. In Figure 4, the individual delays are represented in a histogram, which gives us a better insight in their behavior.
From Figure 4 can be seen that for the cross-over RMGs a lot more small delays have been measured then for the twin RMGs. This can be explained by the situation where the trolley movement to the side of the large RMG cannot be done during the gantry movement, so without effecting the gantry movement. But against these high numbers in small delays, few large delays have been measured for the cross-over RMGs. Where cross-over RMGs have been used only 7.3% of the delays are higher than 1 minute, against 23.1% where the twin RMGs have been used. For all orders done this means that 1.9% of all the orders handled by the cross-over RMGs have been delayed by more than 1 minute. For twin RMGs we find a percentage of 3.4 %, so nearly double as high.
Figure 4: Delays measured during a 24 hour simulation run.
As shown earlier, the experiment with the cross-over RMGs that serve both transfer points reached a lower productivity than where serving one transfer point, which is also represented in the average delay and the deviation (see Figure 5).
Figure 5: Results for cross-over RMGs serving both sides.
An explanation for this is many containers are situated close to the transfer point of destination. As long as the two RMGs are carrying out those orders each on one side, hardly any interference appears. But when a RMG is free to carry out an order for the opposite transfer point, interference is inevitable. Especially for the smaller one, that cannot pass the bigger one until it is able to move its trolley to the side, this can lead to a lot of (unnecessary) delay. Furthermore, it happens that one RMG wants to reach the transfer point where the other is picking up or dropping a container. Then, it will have to wait until the other RMG has finished and will move away. Crossing over will not make a difference in this case.
Concluding we have found an equal productivity for both stack modules served by two RMGs. The delays in order handling that appear are on average equal but much more spread out for the twin-RMGs, so less predictable. Letting the cross-over RMGs serve both sides, leads to a lot more interference and so delay. One should keep in mind, that the workload at waterside and landside is almost the same, which decreases the ability to support one side in the case of imbalanced workloads.
5.2 Results entire terminal simulation
The results of the simulation can be categorized in three aspects. First, we have analyzed the achieved waterside productivity level. This is the result of the service towards the four quay gantry crane in operation, each requesting 40 containers per hour on average. Any delay, due to a shortage of AGVs, leads to a productivity loss of the quay cranes. Secondly, we have analyzed the productivity of the RMGs. Of course this is the result of the simultaneous load at water- and landside, but each system handles these loads differently. Finally, we have analyzed the service time of the trucks and chassis at the landside interchange zone, measured from arrival until departure. These three results provide a good overview of how the system performs under undisturbed operational conditions.
5.2.1 Waterside productivity
In Figure 6 and Figure 7, the achieved productivity of the quay cranes (QC) is shown. Two parameters have been varied: first the number of containers to be handled at the landside end of the RMG stacks; secondly, the number of AGVs carrying out the transportation between RMG and QC.
The following behavior can be observed:
- The productivity of the system with single RMGs is clearly lower in all situations, even with the low landside load. The travel distance for the one RMG affects its productivity, and cannot be compensated by the number of stack modules.
- The productivity of the cross-over RMG is equal to or better than that of the twin-RMG, although the system contains one stack modules (2 RMGs) less. This means that even in the scenario with a high landside load (80 containers per hour), the cooperation between the two cross-over RMGs is better than in the case of the twin-RMG. Only in the case of many AGVs - where the AGVs act as driving buffer and the need for multiple simultaneous moves at the waterside is less - the twin-RMG slightly outperforms the cross-over RMG. However, in all cases the difference is limited.
Figure 6: Net QC productivity with low landside load
Figure 7: Net QC Productivity with high landside load
5.2.2 Yard crane productivity
The RMG productivity is, of course, a direct translation of the waterside and landside productivity pattern. However, some interesting things can be observed. First, the twin-RMG is able to do many pre-positioning moves - those are moves within the stack module, to bring containers in advance closer to the interchange zone of destination - in the case, the landside low is low (on average 5 moves per landside RMG per hour). The cross-over RMG, however, does hardly perform those moves, but they are replaced by productive moves of both RMGs at the waterside (loading landside is for instance 5.1 moves/h, of which 1.3 moves that concern a truck).
Figure 8: RMG productivity with low and high landside load
In all cases, it can be observed that pre-positioning hardly takes place in a scenario with a high workload at the landside. The system is simply too busy to work ahead. However, in practice, the operation is seldom so busy throughout 8 hours. Therefore, usually there will be more time to prepare, even during a busy operation.
5.2.3 Truck service times
With regard to the truck service time, we observe a similar pattern as at the waterside, albeit that the benefit of the cross-over RMG is somewhat bigger than at the waterside. Not only the average is better, also the variation is smaller. 95% of the trucks that are picking-up a container are handled within 7 minutes, whereas this is 16.5 minutes in the case of twin-RMGs. The 95% value of the single RMG is 30 minutes.
Thus, although there are less landside RMGs in the cross-over case, the service times are clearly shorter, which can only be explained by the ability to serve the landside in the peaks - which are very local, in particular when 3 or 4 consecutive trucks need a container from one specific stack module - by both RMGs.
Anyway, both dual RMG systems provide an excellent service level towards the landside traffic, especially when we also consider that the there is no pre-information: the trucks pick a random container.
Figure 9: Truck service time in scenario with low landside load
6 Assessment on other criteria
6.1 Throughput capacity
As can be seen in Figure 10, the storage capacity - being one of the major pillars below the throughput capacity - of the three concepts is quite different. The 6 wide RMG and the cross-over RMG have almost the same storage capacity; the twin RMG achieves approximately 30% more. This also means influences the cost per container, as each RMG can perform more container moves annually.
Figure 10: Storage capacity of yard crane designs
Figure 11: Throughput capacity based on storage capacity
From Figure 12 and Figure 13 can be seen how both storage and handling capacity influence the throughput capacity in the end. The peak requirement is derived from the attainable throughput when the storage capacity is fully utilized. It is calculated as follows: throughput (TEU) / 8760 hours x peak factor (assumed 2.5) / TEU factor (assumed 1.5). This gives the peak waterside requirement in containers per hour. We have assumed that it may happen that the waterside and landside peak occur at the same time. Therefore, we have taken the productivity values of the QC productivity from the scenario with the simultaneous peak (see section 5).
The storage capacity is both in the case of the designs with two RMGs the bottleneck, the handling capacity is the bottleneck in the case of a stack module with one RMG. The differences are, although the same area is being occupied significant (+45% for the twin RMG alternative compared to the single RMG alternative).
Figure 12: Throughput capacity based on handling capacity and storage capacity
6.2 Flexibility
The system with the highest flexibility is the design with the cross-over RMGs. As both RMGs can reach each interchange zone and each container in the stack module in almost all cases ‘ it may happen that the large crane has a break-down with the spreader lowered, and then the small crane cannot pass ‘ the effect of break-down is minimized. Furthermore, this design offers the most opportunities to cope with an imbalance between waterside load and landside load.
The design with the twin RMG offers always the fallback of the second RMG, which can ‘ after moving the other RMG to the maintenance position ‘ also operate on both sides and reach each container in the stack module. However, in case of a break-down, it will take some time to move the broken-down crane in the maintenance position. Besides, during regular operation, there will be more interference between the two cranes, and the system is less able to balance the workload ‘ although via pre-positioning moves the second crane is able to reduce the workload of the first crane.
The design with one crane has clearly the least flexibility. At ECT a rescue crane is available for major breakdowns. This crane replaces the broken-down crane. Furthermore, the crane is less able to cope with simultaneous peaks at waterside and landside, as we have seen in the performance analysis.
6.3 System complexity
The system complexity is a measurement for the cost of software development, and the risk not to utilize the full potential of the concept, because it is too complicated. This is especially the case with the cross-over RMG: to optimize this concept to its full extent, more analysis and design work has to be done. It is already a lot simpler with a twin-RMG, where basically the distributed waterside/landside can be applied. The single RMG is the simplest system, although not really simple, as the priorities of waterside moves and landside moves have to be assessed carefully.
6.4 Investment costs
The estimated investment costs for tracks and cranes are shown in Figure 13. Note that in the case of the crossover RMG, there are four tracks. The price of the RMG in the cross-over design is the average price of the two cranes. The total investment of the single RMG alternative is much lower than the two others. The single RMG is 20% more expensive than the RMG at ECT, but this is the actual price level plus the safety system for direct truck handling at the landside.
Figure 13: Investment yard crane alternatives
6.5 Operational costs
The operational cost in this comparison only consist of maintenance and electricity costs (assumed operating cost) and interest and depreciation cost (assumed 6% interest). Although the crane designs are quite different, it is assumed that the operating costs are not so different. It may be that the single RMG ‘ traveling more up and down ‘ requires more electricity, where the other cranes are heavier, leading to more maintenance to the track. The capital cost show an interesting picture: because of the higher throughput capacity of the alternatives with two RMGs, the capital costs per move are not much higher than those of a single RMG system.
Figure 14: Operational costs
6.6 Overall qualitative assessment
Summarizing, the qualitative assessment looks as follows:
Figure 15: MCA of alternative yard crane designs
The cross-over RMG has apart from its flexibility, many disadvantages, of which the cost is one. The densest system is created with the twin-RMG, which is very important in times of a scarcity of area. Besides, the twin-RMG does not have real disadvantages, although the system requires a higher investment than the single RMG. This concept has clear disadvantages on behalf of the throughput capacity (overall, it is able to reach 1,500 TEU/m quay, whereas the twin RMG achieves over 2,000 TEU/m quay), and the flexibility: in case of break-down, the single RMG system is quite vulnerable.
7 Conclusions
From our analysis we can conclude that the three RMG designs have some similarities and many differences. The cross-over RMG appears to be the best performing one, although the benefit over the twin-RMG is small, especially with a balanced workload. Overall, the benefit does not seem to outweigh the lesser throughput capacity: the cross-over solution takes away a significant amount of space. Both systems provide an excellent landside service level. Therefore, it should be considered to increase the stacking height of the cross-over RMG, to compensate for the space lost due to the double pair of tracks.
The twin-RMG is most suitable for situations with a balanced workload at water- and landside, i.e. situations where most landside traffic is handled by rail or road. The design requires minimal space, and it is possible to handle simultaneous peaks at water- and landside. In case of break-down, additional provisions have to be taken to allow the remaining RMG to work both sides.
The single RMG solution maybe the least expensive concerning investment, the operational cost are similar. The system provides the least density, and is not able to handle simultaneous peaks at water- and landside. However, the number of stacking modules per berth meter is the highest, giving most parallel hooks at the waterside. Therefore, this concept is suitable for systems with a low landside peak, i.e. terminals with a high share of barges handled at the deep sea quay (like ECT).
In further research it would be interesting to look into solutions where the RMGs interact with shuttle carriers, instead of AGVs, creating a decoupled process, increasing the RMG's efficiency, and decreasing the risk of implementation, as the system is more flexible than a system with AGVs.
This article has been published in Port Technology December 2005.
Literature
- Chin-I. Liu, Hossein Jula and Petros A. Ioannou (2002),Design, simulation, and evaluation of automated container terminals, IEEE Transaction on intelligent transportation systems, vol.3, no.1.
- Kim, K.H., Park, K.T. (2002), A note on a dynamic space allocation method for outbound containers, in: European Journal of Operational Research 148, 92-101.
- Kim K. Y., K. H. Kim (2003), Heuristic Algorithms for Routing Yard-Side Equipment for Minimizing Loading Times in Container Terminals, Naval Research Logistics, 50 (5), 498-514
- Kozan, E. (1997) Comparison of analytical and simulation planning models of seaport
- Kozan, E. and Preston, P. (1999) "Genetic Algorithms to Schedule Container Transfers at Multimodal Terminals", International Transactions in Operational Research, 6.3, 311-329.
- Meermans, P.J.M., Wagelmans, A.P.M. (2001), Dynamic scheduling of handling equipment at automated container terminals, Econometric Institute Reports.
- Saanen Y.A. and A. de Waal (2001), Simulatie PCS Nieuw (in Dutch), report for customer, TBA Nederland.
- Saanen Y.A., An approach for designing robotized maritime container terminals, PhD thesis, Delft University of Technology, 2004.
- Vis, I.F.A (2002), Planning and control concepts for material handling systems, Ph. D. thesis, ERIM Ph. D. Series Research in Mangement 14.
Share this
You May Also Like
These Related Stories
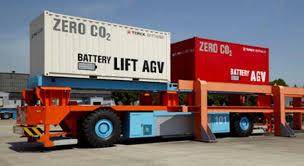
Distributed E-services for road container transport simulation
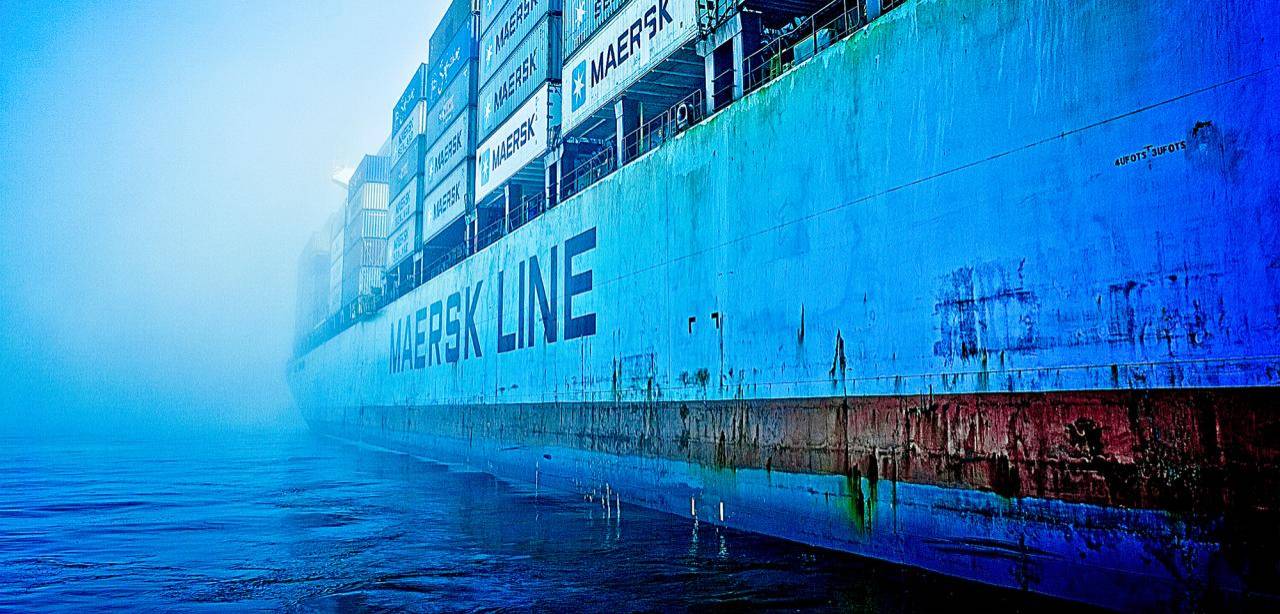
How Simulation Modeling can Support Environmental Initiatives at Container Terminals
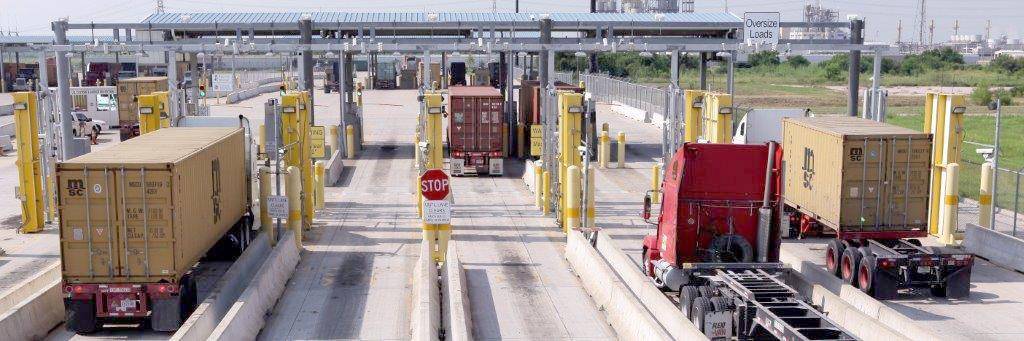