Intelligent stacking as way out of congested yards?
Container terminals are struggling with the ever-increasing volumes, and are therefore searching for solutions to increase throughput capacity without expanding their physical footprint. One way is changing the stacking system itself. Another way is to increase yard density, however this typically leads to a productivity decline when exceeding certain occupancy rates. The question is whether we can avoid this decline by increasing the intelligence of the grounding algorithms? Or do we need additional housekeeping for grooming up the yard? Traditional stack strategies allow for up to 60-65% operational yard density, but here we are looking for achieving 85% and still working at acceptable productivity levels. In this paper, we present an approach how to develop stacking strategies that can cope with higher densities without productivity losses. We have prototyped the algorithms in a simulation environment, and tried them out over a long period of time to be able to assess the long-term effects. We show that principles coming from automated stacking systems, as implemented in Rotterdam and Hamburg – so-called controlled random stacking - , can also be applied in more traditional facilities, such as RTG terminals.
Introduction
Pursuit for intensifying yard operations
As container volumes keep increasing, new container terminals are being built and other terminals – in particular those that cannot easily extend their area – aim at increasing the density of the stacking yard. One way is to go for yard handling systems that can put through more containers per square meter, however this is a costly approach for existing facilities; equipment has to be sold or written off, during the transition the terminal has to work half-speed, and cannot handle the regular volume. Therefore, we suggest another approach: higher density stacking without changing the yard handling system in a physical way. We propose to apply stacking rules that can cope with higher densities without a performance decline. Typically, terminals experience problems with stacking containers at operational occupancy rates of 50% or more.
The question is what rules should be applied to accommodate more volume through the same facility, without losing performance. An important issue here is the availability and quality of information about the container flow. Typically, information is late, lacking, or of bad quality. Besides, the information changes over time. This puts one requirement on the set of rules: they have to cope with changing or missing information.
Furthermore, nothing comes for free. It may be that the new set of rules, requires more equipment to be as effective. However, as volumes are going up, costs may also go up in absolute sense, as long as the cost per move stays at the same level, it should be acceptable to the terminal, which forms our second requirement.
Finally, the service level at waterside (serving the vessel) and landside (serving road trucks and possibly trains) should remain at least at the same level.
Subject of our exercise
As most container terminals world-wide are using rubber tyred gantries in combination with terminal trucks, we have chosen to apply our stacking strategies to these type of terminals. Typically, the layout of such terminals looks like shown in Figure 1. Behind the berth, there are a number of blocks going into the depth of the terminal. Along the quay wall, these blocks form so-called lanes.
Figure 1: Generic layout for RTG terminal: blocks of containers parallel to the quay, with driving lanes between the blocks for trucks or prime movers.
In principle there are two types of terminals: transshipment terminals and import-export terminals (Saanen, 2004). The first type mainly moves containers from seagoing vessel to seagoing vessel, whereas import-export terminals move containers from seagoing vessels to hinterland transportation modes, such as barge, trains and trucks. The issues are only partly comparable between the two types of terminals, however, no terminal is strictly the one type nor the other, although there are more and more terminals that are almost 100% transshipment. Examples are Tanjung Pelepas, Singapore, Salalah, Port Said, Gioia Tauro, Malta Freeport, and Algeciras. All of these ports have transshipment rates over 90%. Then, there are many terminals that hardly perform transshipment (typically below 15%), especially in the United States, in England, and at the European continent. However, some of them (for instance Rotterdam and Antwerp) have a high barge share as part of the hinterland transportation modal split. These ports have excellent inland waterway connections deep into the continent. The container flow in those terminals show more characteristics of transshipment terminals than “real” import-export terminals, because the volume over the quay wall is much higher than handled through gate or rail terminal.
In the reflection, we will discuss what the consequences of these differences are for our conclusions with regard to stacking rules. In the remainder, we will focus on transshipment terminals, as they provide (relatively speaking) the best information about where a container is going. The latter is caused by the extent to which the transportation is organized: hinterland transportation is a poorly organized, with scattered processes, many different suppliers, often one-man companies, whereas the sea transportation is more and more in hands of a couple of large shipping lines. Although not perfect at all, the information about seagoing containers is acceptable in terms of availability and quality.
Methodology of assessment of the stacking rules
In this paper, we try to assess the impact of yard operating rules, as well as we try to define a set of rules that will increase stacking capacity without increase in costs per move, and without a performance decline.
As containers are staying between a couple of hours until a couple of months on the terminal, the consequences of yard operating rules affect the process over a long period of time. Furthermore, the situation at any given moment is subject to dynamic effects. Vessels being delayed, trucks arriving without pre-notice, information coming in late, volumes that vary from vessel to vessel, etc.
These circumstances made us choose for applying simulation as way to assess the qualities of the yard operating rules. This approach (Saanen, 2004) has proven to be well suited for the analysis of these kinds of complex systems. Therefore, we have developed a terminal simulation model, containing all operations between the waterfront, and the gate. The waterside transportation is by means of tractor trailers, the landside operation is direct, which means that the RTGs handle the road trucks directly.
Outline of the paper
The outline of this paper is as follows. First, we will review literature with regard to yard operating rules and high density stacking. Secondly, we will elaborate on the yard operating rules in the reference case and in the alternative case, as suggested by us. Then, we will discuss the used simulation model and the experimental set-up. Subsequently, we will discuss the results of the simulation experiments. Finally, we will discuss the other relevant aspects and come to a conclusion.
Literature review: high density stacking
A broad range of research has been done on container terminal stack yard operations, in order to improve efficiency. Though, little has been published in scientific literature on stacking problems. A main reason may be that the practical problems are quite complex and do not easily allow for analytical results which are relevant for practice.
Stacking problems can be dealt with in two ways: simplified analytical calculations or detailed simulation studies. The first gives insight into the relationships between the various parameters on a more abstract level. The second can go in much more detail, with the negative by-effect that it is time consuming and only few people really understand its ins and outs. No comprehensive stacking theory exists today, and a good stack design not only depends on local space conditions but also on the information characteristics of the ingoing an outgoing flow of containers which may vary from place to place. Examples of both approaches are given below.
Sculli and Hui (1988) were among the first to develop yardsticks for the relation between stacking height, utilization (or storage space needed) and reshuffles by applying a comprehensive simulation study. Taleb-Ibrahimi et al. (1993) discuss this relation for export containers both at a long-term scale as well as operationally. They discuss dynamic strategies which store early arriving containers in a rough pile, until a certain date, after which all containers for a ship are put in a dedicated storage area (usually close to the berthing place of the ship). The procedures developed calculate the storage space needed as function of the stacking height. De Castilho and Daganzo (1993) continue these studies with the stacking of import containers. They consider two strategies, one which keeps stacks of the same size versus one which segregates the containers on arrival time. A slightly more detailed discussion resulting in tables and yardsticks (looking at stacking blocks with bays of similar sized containers served gantry cranes), both analytically and by simulation was given by Kim (1997). Kim and Kim (1998) extended these studies by also taking the number of stacking cranes into account. They developed a simple cost model for optimizing this number using analytical approximations for the various performance measures. Kozan and Preston (1999) provide a model where storage strategies and container handling schedules are determined in order to minimize berthing time. Therefore they want to minimise the sum of setup times, where setup time is described as the time necessary to remove the containers on top of the desired container.
In case the stowage plan is available some time before the sailing, the containers in the export stack may be re-marshalled. This results in an “ideal” stack and thus, less handling work during the loading operation of the vessel. Kim and Bae (1998) describe a two stage approach in order to minimize the number of containers to be moved and to do so in the shortest possible travelling distance. Although such a re-marshalling approach seems very attractive, it is not often possible to do so. As already mentioned, the stowage plan is only known shortly before the loading operation. Moreover, building up this “ideal” stack also requires additional storage space which may not be available.
Segregating space allocation strategies of import containers was studied by Kim and Kim (1999). In segregation strategies, stacking newly arrived containers on top of earlier arrived containers is not allowed. Spaces are thus allocated for each arriving vessel. They study cases with constant, cyclic and varying arrivals of vessels.
An empirical statistical analysis of the actual performance at a Taiwanese container terminal was provided by Chen et al. (2000). The number of shift moves was related to the storage density, the volume of containers loaded and the volume of containers discharged both for stacking crane blocks and straddle carrier blocks.
Decision rules using weight groups for locating export container were derived and validated through dynamic programming by Kim et al. (2000). Weight is a useful criterion since heavy containers are usually stored deep in a ship.
Stacking policies for automated container terminals are investigated by Duinkerken et al. (2001), who use a detailed simulation model that not only models the stack, but also the quay transport in an automated container terminal. They also apply categories, but in a much more simplified way than we do in this paper.
The results for the straddle carrier operated stacks are not always relevant for the stacks with automated stacking cranes, as reserving space is more complex. Though few focus on assessing different automated container terminal design concepts on behalf of their stack yard design. Below, we present a brief overview.
Yard operating rules
Generic choices when designing a yard operating strategy
Although container terminals are different in their appearance, container flows and the information around the physical flow can be described in similar terms for any terminal. Therefore, we have defined a set of generic rules that apply for RTG terminals, but certainly also apply for different types of handling systems.
The following conceptual choices have to be made:
- Dedication of areas versus no dedication. With dedication is meant that a specific area is meant for specific type of containers. For instance an area for import containers, or an area for containers for vessel XYZ with port of discharge NY. No dedication means that beforehand no specific areas – apart from the distinction between reefer, MT and dry – are reserved. Of course, no dedication does not mean that the rules within the TOS software (e.g. allocation filters) cannot contain preferences for import containers close to the gate, in the contrary.
- Consolidation versus dispersion. With consolidation is meant that all containers of a specific type (the degree of specification can be varied, from service, downto vessel, downto vessel-PoD specific) have to go to the same area. In the most extreme alternative, all containers for one voyage go to one (large) area. Dispersion is principally the opposite: one tries to distribute containers of the same kind as much as possible over the yard.
- Housekeeping versus immediate final grounding. At the moment, many containers are discharged to a certain location and moved afterwards to the final location from which the container is loaded onto the vessel. This in order to increase productivity. However, these housekeeping moves are additional moves that are not strictly necessary. Therefore, an alternative that avoids housekeeping as much as possible would principally reduce the number of moves, and therefore the cost. The other side is that it may require more equipment (yard handling and transportation equipment) during the productive operation (discharge / loading).
- Discharge or loading optimised grounding. Without considering the possibility of intermediary housekeeping, a grounding location can be sought based on the optimal location from a discharge perspective or from a loading perspective. Especially the distance to the QC is here relevant. The compromise in between is considering both.
The first: traditional stacking an RTG operation
When analyzing stacking strategies applied at RTG terminals, we need to make a distinction between transshipment terminals and import-export operations. As said earlier, we will focus on the first. So what is said here may or may not apply for import-export operations.
In a transshipment operation the available information is for 50% of the containers better than in an import-export terminal, because most containers (if not all) are seagoing after arriving at the terminal. The information about where they go and with which ship is known upon arrival to a certain extent – however practice still shows that during the container dwell in the yard 30-40% of the information changes. This makes is possible to locate containers of similar destination (vessel voyage destination) close together in the yard in order to increase the speed of the loading operation, i.e. choice one is consolidation. This can be done in real-time (building in a preference to stack containers next to a similar one, or on top of a same one), or ahead (during the planning process see also section 4.1.1). To our knowledge most terminals plan this ahead by allocation areas to specific containers, i.e. they apply a dedication strategy. With regard to the third choice, terminals tend to apply either a mixture between immediate grounding and housekeeping. The degree to which they are able to either one, depends on the quality of information, the timeliness of information, and the amount of equipment available and the cost of labor. The cheaper the labor, the more the focus will be on housekeeping, as the cost are low, and the productivity during vessel operation is higher. The final choice is of lesser importance in the case housekeeping is inexpensive; if not, it depends on the density of the operation whether discharging or loading is favored.
Typical stacking strategy in an (automated) RMG operation
An operation in an (semi-) automated terminal can be quite different from an operation in a terminal where there is manning on the machines. In the latter case, movements need to be minimized as much as possible, simply because the majority of the costs (50 – 70% in North-West Europe and the United States) is labour related. In an automated terminal, however, moves within the yard for instance, can be executed without interference of labour. Therefore, a basic element in the stacking strategy for these types of terminals is housekeeping, i.e. preparing the yard for upcoming operations.
A second rule in these kind of operations is a results of the fact that always all RMGs are available (except when they are broken down or being maintained of course). In an RTG operation, one tries to reduce the RTG in operation as much as possible. Therefore, the load needs to be consolidated as much as possible to avoid the RTGs driving around. As all RMGs are in operation in an automated operation, all locations in the yard are accessible at any time. Therefore, cargo can be distributed over the yard, in order to distribute the workload over as many machines (RMGs) as possible. So no consolidation, but rather spreading out the load in order maximize the number of RMGs serving a quay crane.
Figure 2: Example of an RMG terminal with perpendicular stack module equipped with one or two (as depicted) RMGs per module
A third rule is related to the fact that the RMGs tend to be fast in the gantry direction, much faster than RTGs. Therefore, one can put the containers in any position in the stack module perpendicular to the quay. Of course, there should be a tendency to the waterside end for export containers, and a tendency to the landside for import containers (gate and rail), but traveling one container position further in the stack (6.5m) takes about 2 seconds. So traveling the entire block (varying typically between 30 and 50 TEU, equaling 200 – 300m) takes a maxim of 75 seconds or so. Therefore, not to a high degree determining the performance of the RMGs. This means that one can be flexible in positioning the containers in the yard.
A final rule (but this list is not exhaustive) concerns the importance of workload based grounding and scheduling. Each stack module has to deliver about 10-15 containers per hour at the waterside during a peak operation, and there is only one RMG to perform these moves. In order to smoothen the workload, the actual RMG workload is a very important factor when deciding where a discharge container goes to in realtime.
Operating an RTG yard according to the rules applied in an RMG terminal
When we take the basic principles and constraints within an RTG terminal – especially the need to avoid much gantrying by RTGs – and apply ideas from operating an RMG one can think of the following rules. Important is to bare in mind that all rules have to be seen in relation to each other. It is not a sequential decision process, but it is a multi-factor decision making process.
Rule 1: Apply a multi-factor grounding decision
A container can be grounded at many locations and – in most cases - there is not one single decisive criterion that determines the grounding location. Therefore, the decision is a multi-criteria decision, considering multiple variables. This is typically the way grounding algorithms like available in the most common TOS systems work when configured properly. However, it may be that one or more of the criteria mentioned below cannot be considered yet in common-of-the-shelve TOS systems.
Rule 2: Avoid fixed dedicated areas
Avoid any fixed dedication beforehand. However specify rules that lead to a segregation in the yard. Typically the following rules can be applied:
- Import containers: ground them close to the gate.
- Export containers: ground them close to the berth from which the will be loaded.
- Export containers: ground them based on their time until departure closer or further from the berth.
Figure 3: Attraction factor, grounding locations close to the berth of destination are to be preferred during discharge
Avoid fixed RTG assignments
In order to allow for a maximum flexibility and a maximum RTG utilization – typically RTGs produce less than 10 productive moves where it is feasible to operate above 25 productive moves per hour – RTGs should not be assigned to a specific operation during a shift. It may be that due to the consolidation that has been achieved, an RTG is working during a longer period of time for one QC, or one vessel, but generally speaking there is no dedicated assignment.
This will lead to the inability to distinguish between longshoremen (read: waterside operation) and casual workers (read: housekeeping), because those operations will be mixed. As a consequence of the grounding strategy, however, the amount of housekeeping (see rule: avoid housekeeping) will be drastically reduced.
Consolidate in real-time
Consolidate as much as possible. As said, RTGs do not like gantry travel. Therefore, their productivity rises with a smaller gantry travel percentage. The more similar containers are close to each other, the more productive the RTGs will be, and the less RTGs will be needed to achieve certain productivity. Consolidation starts with building piles (or stacks) of exchangeable containers (same size weight class, VVD). Then as the first pile in a bay is full, it is preferred to stack another pile of the same containers in the same bay or very near.
An additional rule may be to stack containers with a high likelihood of VVD changes, or other reasons for rolling (for instance containers to be loaded on feeder going to West-Africa). When these containers are combined to piles, the number of shuffles per rolling decreases, because the rolling containers do not affect the piles with non-rolling containers, and the other containers in the “rolling” pile are anyway likely to roll.
Assign a discharge location as late as possible
Real-time grounding is basically supported by expert decking: a human planner is hardly able to do it without a tremendous effort. Therefore, not earlier than when the container is put on the Terminal Truck, a discharge location should be chosen. This to avoid any fixed dedicated area.
Assign discharge location based on available equipment
A discharge location is only interesting when an RTG is “near”. Although near is a relative notion, it expresses the principle: by selecting the grounding location real-time (see assign discharge location as late as possible), a real-time overview of the RTG positions and actual RTG workload, i.e. all orders that are destined or originating from a specific RTG multiplied by the duration per order in the coming 10-15 minutes, has to be considered. The shorter an RTG has to travel, the better it is.
Separate consolidated areas for different VVD with same time window
Containers with a different VVD, but with a similar time window should be distributed over different blocks to avoid clashing of RTGs or overloaded RTGs during loading. That means that the real-time grounding should consider the time window upon departure of the container as well. As this information is available in the actual berth schedule, this should be possible. Anyway, as consolidation of similar containers is a rule, and distribution of workload over the various RTGs is a rule, this will in principle happen. However, to ensure it principally, this rule should be added to expert decking.
Avoid housekeeping (or ground on the final location)
Avoid housekeeping as much as possible, or try to ground on the final location as much as possible. This rule is clearly different from an operation with automated equipment, where housekeeping is almost for free, and direct grounding sometime impossible because of a lack of RMG capacity. However, here a housekeeping move costs additional labour hours: it requires three equipment moves (two RTG moves, one truck move). As containers can be stacked anywhere (no fixed areas), containers can be grounded distributed over the yard, based on the availability of equipment at that location, or the availability of similar containers in a non-complete pile (see consolidation rule - 3.4.4).
There are two exceptions when housekeeping is to be preferred over immediate final grounding: (1) the situation is when grounding at the final location is impossible because the required productivity cannot be met due to a lack of equipment or (2) when the grounding in a pre-stack location plus a housekeeping move requires less labour hours than immediate final grounding (for instance in the case of twin-lift).
Use remaining shift hours to housekeep containers
As the workload during a shift is never constant, it is likely that most shifts have some left-over labour hours. In those cases, the available labour is not required to obtain the required productivity levels, and therefore can be used for other purposes. The following housekeeping flows may be initiated then:
- Containers from the “long dwell time stacks” that are to be loaded (remaining dwell time <7 days) may be moved to the other stacks, closer to the quay.
- Containers that are positioned far from the berth of destination may be relocated, preferably near containers of the same type that are already standing close to the berth of destination.
- Rollings that will cause shuffles during the loading operation that are known at that point in time.
- Containers that are standing in a pre-stack (see rule on avoiding housekeeping).
- Large contingents of containers for different VVDs that are grounded in a single block. As those containers may lead to clashes of RTGs during loading, these containers are candidates for housekeeping.
Simulation model
Total terminal model
The simulation model that we have used to model the stacking strategies and assess them is a comprehensive model in the sense that all processes taking place between gate and vessel are depicted at a detailed level. Basically, the model consists of two main components: one representing the Terminal Operating System (TOS) and one representing the physical process that takes place at a terminal. The connection between the two is quite similar to the interfaces that are in place in real operations between TOS and equipment, handhelds, and other communication devices (for instance pedestals at gate and truck interchange).
TOS simulation
The first main component is the module in the simulation that takes care of most functionality of a typical TOS, i.e. planning, scheduling, grounding, allocation and dispatching in real-time. That means it comprises the work instructions for each piece of equipment based on the plans that result from information such as load/discharge lists, pre-arrival information, gate arrivals, train schedules, shift schedules, and so on. This information may become available at some point in time, i.e. it becomes available in a realistic way, possibly incomplete, or even incorrect. In principle, at a certain point in time, there is no more information available than the real TOS would have.
Having said this, what is the functionality incorporated in the simulated TOS? And how is it structured? There are two axes along which the functionality has been structured. The first axis is the time horizon, which means that the simulated TOS distinguishes planning (time horizon 18-24 hours), scheduling and allocation of equipment and manpower (time horizon 1-8 hours) and dispatching and grounding (in real-time). According to our information, this is quite in line with the way terminals control their operation, supported by a typical TOS. Input to the TOS simulation is the following information:
- Pro forma berth schedule, made actual to the latest information available at a certain moment, including also the required service level to vessels, and the number of quay cranes working on the vessel.
- Load lists of vessels, based on the BAPLIE files.
- Discharge lists containing information about the next mode of transportation, the PoD, the container weight, eventually the vessel.
- Gate arrivals (eventually pre-notifications), including container pick-up or delivery information.
- Train arrivals, train load lists.
- Availability of equipment (yard, transportation) and manpower per shift.
Based on this information, the simulated TOS creates the work plans for each point of work during a certain time period (at least a shift ahead). These work instructions include productive and pre-productive moves (also called housekeeping, or gantry moves). Of course, as the work at the landside cannot be planned in detail ahead, an estimate is made based on historical data, i.e. the expected number of moves to be executed during the specific time period. The level of detail of the plans is not very high, i.e. the actual piece of equipment in the yard that will perform the specific move is not yet known. To a certain pool of work, a pool of equipment is allocated, for instance 320 housekeeping moves get 4 yard teams, consisting of each 2 RTGs and 5 trucks throughout an eight hour shift (though not necessarily dedicated to this type of work; RTGs may execute productive moves and housekeeping moves during their shift).
During the execution of the work, work is scheduled in advance. The horizon of scheduling differs quite among various handling systems. The minimum amount of scheduled work is a work queue that ensures timely delivery of a container to a certain point of work, in formula:
Here a delivery cycle is defined as the time needed for a terminal truck to bring one container from the stack to the quay crane and return to the stack. The production cycle is defined as the time needed to load one container from the quay in the ship and for the quay crane to return to its original position. As the delivery cycle time and the production cycle time vary a lot, one needs to create a larger work queue to cope with this behavior. The following formula gives a yardstick:
Typically, the simulated TOS plans one bay in a vessel ahead per Quay Crane (QC), unless this work comprises less orders than necessary to feed the QC for half an hour with the average rate (so somewhere in between 15 and 25 containers as a minimum). With a typical cycle for a truck of 12 to 15 minutes, the minimum would be 12 minutes / 2 minutes (at a rate of 30 cycles per hour) of 6 moves. Considering delays and faster cycle times, typically a ratio of 20 / 1 results, i.e. 20 orders at least.
The final step in the TOS’s work is to decide where a container goes when entering the terminal (water- or landside), i.e. the grounding decision, and then to dispatch a specific order (to bring a container from A to B, or to load or unload a container from or to the stack) to a specific piece of container handling equipment. These so-called work instructions are handed over to the drivers of the equipment via the said interface. Typically, they appear in the radio data terminals within the cabin of the container handling equipment.
Furthermore, the simulated TOS replans and reschedules whenever there is a reason to do so; this can be a break-down, but also a serious delay exceeding a certain threshold.
In certain terminals, there may be some decision freedom for the drivers of RTGs or strads for instance. Instead of receiving individual work instructions, there may be a list of instructions made known to a pool of equipment. It is then up to the driver which job to take from that list. This decision in the simulation is then taken at the execution level, which contains the driver’s decision logic.
Simulation of physical processes
The second main component of the simulation model is the part that represents all physical movements, i.e. of container handling equipment and containers. In case of manned equipment, the behavior of drivers has also been modeled, whereas in automated the software that performs routing, collision avoidance, deadlock avoidance, and velocity control is present as well. In the manned situation, the driver takes care of this. In both cases, manned and unmanned, similar types of logic are required, although the way people drive machines, is more flexible, and therefore more difficult to model.
Figure 4: Flexible routing of driving in case of traffic that is in the way
In the simulation model, we tried to model the behavior as realistic as possible, i.e. to incorporate all separate movements of machines (gantry, trolley, hoist, spreader) as well as the dead times that typically occur, for instance when picking-up a container. Based on extensive measurements at various terminals, observations, and interviews with operational experts, we have come to an equipment model that can be considered to be a valid representation of an average piece of equipment, including an average driver.
Output of the simulation model
The main output of the simulation consists of the following parameters:
- Waterside productivity level in moves per hour (moves/h).
- Landside service time of trucks on the interchange points in minutes.
- Equipment productivity on water- and landside, respectively of the transportation vehicles in moves per hour (mph), and the RTGs in moves per hour.
- The truck handling time at the stack module, measured from arrival until ready to depart.
All results will be gathered for various amounts of equipment. More detailed results can be acquired, but are not relevant for the final decision-making.
Rules implemented in the simulation
Not all rules that we mentioned are already implemented in the simulation model of the RTG terminal. We started with a very simple implementation of the rules that origin from the RMG terminal, being the following:
- Distribute the containers over the yard, but build piles (one groundslot and the containers on top of that) of containers sailing with the same vessel and for the same port of discharge, and of the same weight class.
- Consolidate real-time by having similar containers attracting each other, which means that piles for the same vessel, for the same port of discharge are likely to be close, Groups of containers for the same service & POD are consolidated and dispersed simultaneously: several locations (stack bays generally speaking) in the yard are used where containers of the same service and POD are grounded together. By doing so, more than one RTG can execute the vessel loading orders – which are likely to be loaded in one vessel bay and hence have to be executed in a small time window – simultaneously. The orders of each RTG will originate from one or a couple of close bays.
- Use the actual workload of the RTG when deciding where to ground a container.
- Use the actual (or better: expected future) position of the RTGs when deciding where to ground a container. If an RTG is near (or approaching) one of the locations where containers of a specific service & POD are stacked, then this area gets priority for grounding. When a new location for containers of a certain service & POD is to be used, then an available location close to an RTG is selected.
- Use expected dwell time of container when deciding a grounding location for the container. In case of relative short dwell time: ground the container closer to the quay, else further away from the quay.
- Ground container within range of expected loading vessel when known to reduce truck drive time during loading.
- Ground container close to the quay crane that discharged the container to reduce drive time during discharge.
- Load from the location where the container has been grounded (unless the container has been shuffled).
As a benchmark, we used a fine-tuned strategy especially designed for RTG operation in transshipment mode. Typically the rules as described in section 3.2 are applied.
Results of the simulation experiments
Results simulation of manned RTG terminal
Waterside productivity
The most important performance indicator for a terminal is still the berth and/or the quay crane productivity, although there is a slight increase in interest in performance at the landside. For both analyzed strategies, below figure shows the achieved quay crane productivity on each vessel handled in one week of operation.
Figure 5: Quay crane productivity measured over all vessel handled in one week for two operating strategies.
In the particular week of operation (the peak obviously), the yard occupancy rate is around 85% (there is a difference between the traditional strategy where only 5 high was allowed in the area for discharge containers, and 4 high in the loading area; in the random strategy 5 high was allowed everywhere, herewith decreasing the occupancy rate although the same number of containers was at terminal), measured from the theoretical maximum, i.e. length x width x maximum height. Both strategies deliver an average quay crane performance of approximately 35 containers per hour; the traditional strategy performs about 1 crane move per hour worse over 6 weeks of operation. This means, the vessel turn-around time is almost indifferent to these two yard operating strategies.
Another effect which is worthwhile to investigate is the effect of an increasing occupancy rate. During the 6 weeks of simulated operation, the occupancy rate varied between 70 and 90%, which has an impact on the productivity. In both scenarios, the occupancy rate influences performance in a negative way, but the effect is stronger in the traditional strategy (see Figure 6).
Figure 6: Effect of an increasing occupancy rate on the quay crane performance
A higher density in the yard means that more shuffles must be executed per stack-out move on average. Figure 7 shows the effect of a higher number of shuffles on QC productivity. This effect is close to zero. Reason for this is the fact that RTGs execute a limited number of productive moves per hour and hence have spare time to execute the shuffles in advance. When the actual stack-out move is executed the shuffle has already been processed and causes no delay to the operation.
Figure 7: Relation between the number of shuffles per outbound move and quay crane productivity
A higher yard density has another effect: the RTG gantry time per move increases. With a higher yard density there are less possibilities to ground containers close to RTGs. This results in less optimal grounding slots and more gantrying by the RTGs. The gantrying of RTGs has a direct impact on the productive moves. Trucks have to wait longer to be served and this results in a decrease in QC productivity. See Figure 8.
Figure 8: Relation between RTG gantry time per move and quay crane productivity
The effect of longer RTG gantry time on QC productivity is similar for both scenarios, although traditional stacking can cope with longer gantry times a little better. Figure 9 shows the effect of a higher yard density on RTG gantry time. It is interesting to see that in the scenario with random stacking the RTG gantry time per move doesn’t increase as much as with traditional stacking when yard density increases. This is an important factor that causes a higher QC productivity in the random stacking scenario.
Figure 9: Relation between yard density and RTG gantry time per move
A third rule is related to the fact that the RMGs tend to be fast in the gantry direction, much faster than RTGs.
Figure 10: Number of housekeeping moves performed in traditional strategy
Possibly one of the most important affects of the new strategy is this: the new strategy has a significant positive effect on the man hours needed to operate the terminal. Since no housekeeping moves are required a save on labour cost is possible. Both the number of RTG hours and the number of truck hours decreases.
In both simulation experiments the same numbers of equipment have been available. The RTG working hours per week in the traditional stacking scenario equalled 95 hours (out of 168 in a week), while in the random stacking scenario no more than 66 hours were needed per RTG to execute all orders (-30%).The operational hours per terminal truck also decrease significantly when switching from traditional stacking to random stacking: from 132 to 80 hours per truck (-39%).
Conclusions
Finding new ways to increase the capacity of a terminal is of imminent importance to the container business, as there are limited alternatives. Therefore, the relevance of increasing the yard density without performance loss, should be clear.
One idea to do so is to apply strategies that allow for higher densities, such as random stacking. As less space needs to be reserved, because all locations are in principle available, the space can be better utilized. This can also be done by refining existing strategies.
In this paper we showed the comparison between a refined but still traditional strategy for operating a transshipment RTG terminal with a simple random stacking strategy for this type of terminal.
Overall the difference of the two strategies on performance – here we took the main performance indicator for a transshipment terminal, which is quay crane productivity – is small. Over six weeks of operation, the difference in quay crane productivity was 0.7 container lifts per hour. However, there are some interesting relationships to be observed. First, at an increasing yard density, the productivity decreases. This is mainly caused by increased movements of RTGs around the yard. Due to the increased gantry movements, the RTG productivity drops, impacting the quay crane productivity to a high extent.
While the impact of density on the gantry movements of RTGs is higher in the random stacking scenario than in the traditional scenario where consolidation of cargo is done, the overall impact of gantrying on productivity is lower, because the terminal is less sensitive to higher yard density with regard to RTG gantrying.
However, since it proves to be a major factor, the refinement of the random strategy should lie in reducing the gantry movements, by trying to consolidate as much as possible, but without reserving any space. Such can be realized by assigning bonus points to storage locations that are close to storage location where already similar containers are stored. As similar containers are typically loaded at the same time, the RTG will have to move less. However, one should not perform this blindly, as too large contingents of containers may require more than one RTG operating. Then, consolidation at one location leads to RTGs that are hindering each other, which would also lower productivity. Therefore, a next step in our research will be to refine this assignment, taking both effects into account.
This article has been published in Port Technology April 2011.
Literature
- Castilho, D. B. and Daganzo, C. F. (1993), Handling Strategies for Import Containers at Marine Terminals, Transportation Research,l 27B, 151-166.
- Celen, H.P., Slegtenhorst, R.J.W., Van der Ham, R.Th, Nagel, A., Van den Berg, J., De Vos Burchart, R., Evers, J.J.M., Lindeijer, D.G., Dekker, R., Meersmans, P.J.M., De Koster, M.J.M., Van der Meer, R., Carlebur, A.F.C. and Nooijen, F.J.A.M. (1999), FAMAS – NewCon: Phase 1: Starting points, Phase 2: Architecture integrating information system, CTT publicatiereeks 32, ISBN 90-76091-36-6 (in Dutch).
- Cullinane, K. and Khanna, M. (2000), Economies of scale in large containerships: optimal size and geographical implications, Journal of Transport Geography,8,181-195.
- Dekker, R, Voogd, P., Nagy, L. and Meersmans, P.J.M. (2000), FAMAS - Newcon: Long-term stacking experiments for the reference case, TRAIL Communication Series 2000, ISBN 90-5584-038-6.
- Dekker, R., Piersma, N. de Bruin, J. and Van de Vlist, E. (1994), Operations research in action for mainport Rotterdam", TRAIL-studies 94/5, Delft, The Netherlands (in Dutch).
- Duinkerken, M.B., Evers, J.J.M. and Ottjes, J.A. (2001), A simulation model for integrating quay transport and stacking policies in automated terminals. In Proceedings of the 15th European Simulation Multiconference (ESM2001), Prague, ISBN 1-5655-225-3, SCS.
- Kim K.H.(1997), Evaluation of the number of rehandles in container yards, Computers and Industrial Engineering,32, 701-711.
- Kim K.H. and Bae, J.W. (1998), Re-marshalling export containers in port container terminals. Computers and Industrial Engineering,35, 655-658.
- Kim K.H. and Kim H.B. (1999), Segregating space allocation models for container inventor-ies in port container terminals, International Journal of Production Economics,59, 415-423.
- Kim, K. H. Kim (2003), Heuristic Algorithms for Routing Yard-Side Equipment for Minimizing Loading Times in Container Terminals, Naval Research Logistics, 50 (5), 498-514
- Kim, K.H., Park, Y.M. and Ryu, K-R. (2000), Deriving decision rules to locate export containers in container yards. European Journal of Operational Research,124, 89-101.
- Kim, K.Y. and Kim, K.H. (1998), The optimal determination of the space requirement and the number of transfer cranes for import containers. Computers and Industrial Engineering,35, 427-430.
- Kozan, E. and Preston, P. (1999) "Genetic Algorithms to Schedule Container Transfers at Multimodal Terminals", International Transactions in Operational Research, 6.3, 311-329.
- Meermans, P.J.M., Wagelmans, A.P.M. (2001), Dynamic scheduling of handling equipment at automated container terminals, Econometric Institute Reports.
- Meersmans P.J.M. and Dekker, R. (2001), Operations research supports container handling, Report Econometric Institute EI/2001-22, Erasmus University Rotterdam.
- Saanen Y.A. (2004), An approach for designing robotized marine container terminals, Ph.D. these, Delft University of Technology, pp. 325, ISBN 90-5638-129-6
- Sculli D. and Hui C.F. (1988), Three dimensional stacking of containers, Omega16, 585-594.
- Steenken, D, Voß, S. and Stahlbock, R. (2004), Container terminal operation and operations research – a classification and literature review, OR Spektrum26,3-49.
- Taleb-Ibrahimi M, De Castilho, B. and Daganzo C.F.(1993) Storage Space vs Handling in Container Terminals, Transportation Research B,27B, 13-32.
- Vis, I.F.A (2002), Planning and control concepts for material handling systems, Ph. D. thesis, ERIM Ph. D. Series Research in Mangement 14.
- Yun WY, Choi YS (1999) A simulation model for container-terminal operation analysis using an object-oriented approach, International Journal of Production Economics, 59, p. 221-230.
Share this
You May Also Like
These Related Stories
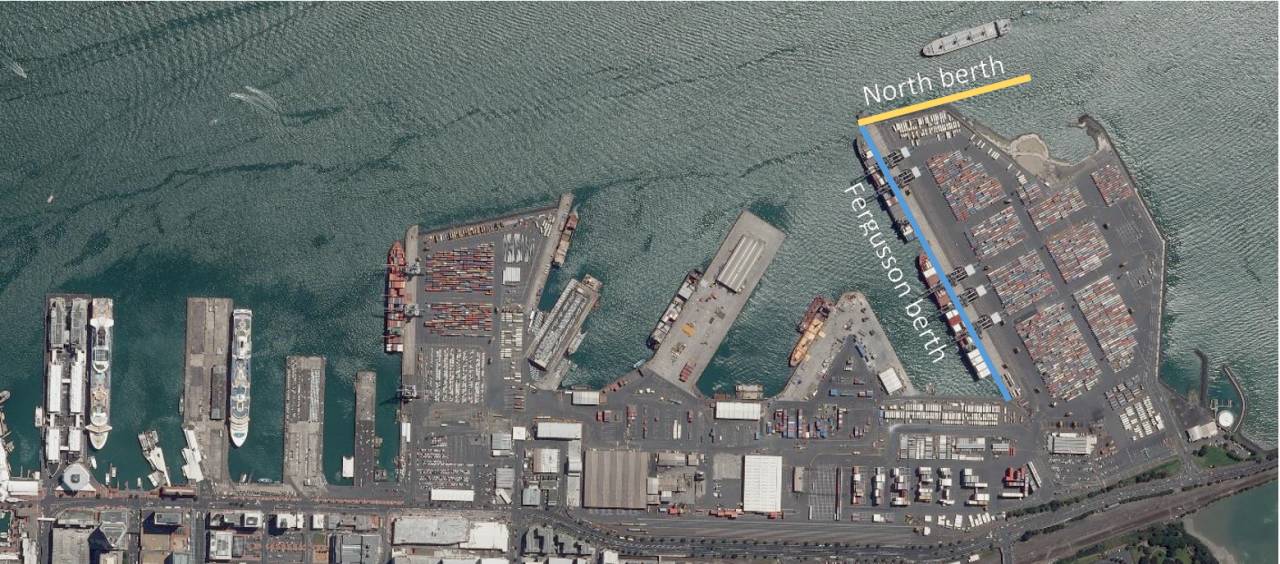
Innovation and process optimization driving success
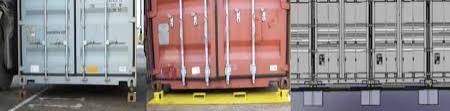
An operations perspective on new twistlock handling in terminals
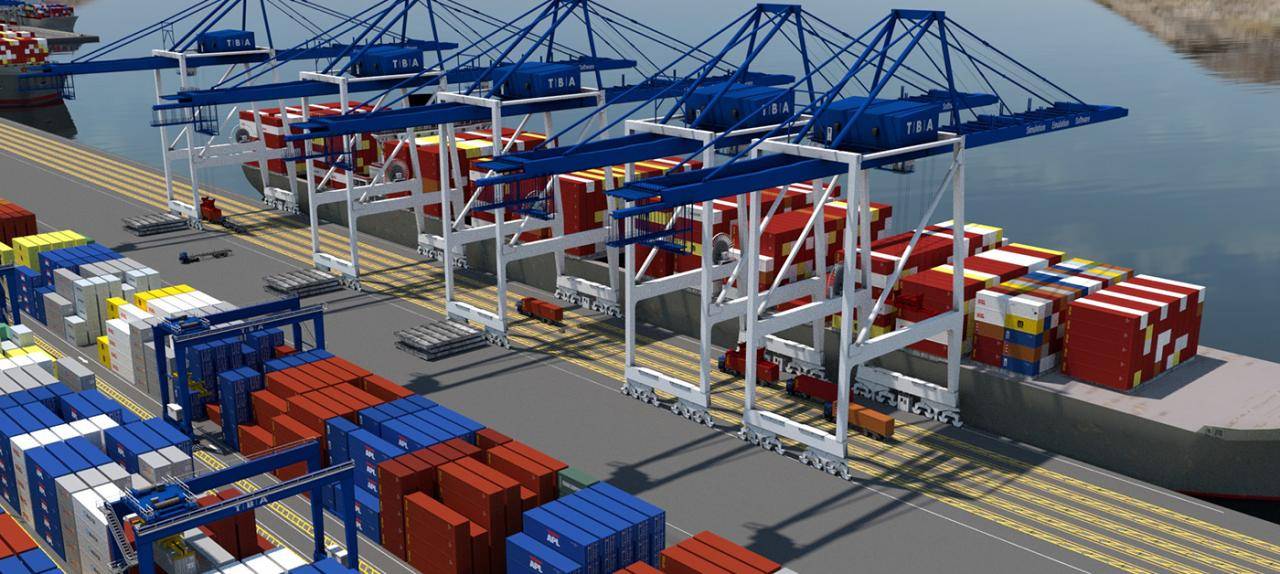