Analysing the stockyard: one of the basic elements of a dry bulk terminal
Whether it is an export or import terminal, a stockyard is one of the basic elements of a dry bulk terminal where a variety of handling equipment is deployed; in addition, it is often a strategic stock and it is always a crucial component in the overall terminal logistic performance.
Following arrival at the terminal, bulk cargoes are usually held in storage before delivery either by vessels, barges, trains, trucks or conveyors. Two main activities take place at a storage area; one is to stack the commodities and the second to reclaim them. Hence, for a stockyard analysis, various factors need to be taken into account, such as:
- the material properties of the commodities handled at the terminal;
- the strength of the ground conditions;
- equipment limitations (e.g. outreach and height of machines, capacity);
- availability of storage space (land);
- the ‘peak’ demand (operational and seasonal);
- the technology deployed; and
- environmental concerns.
INFLUENCING FACTORS FOR STOCKYARD DESIGN
Physical factors
- Material properties
Bulk material properties determine the behaviour of the material during handling and storage. Parameters such as internal friction and wall friction are essential to design or choose a suitable silo or hopper for storage.
The inherent material properties influence the choice of storage options. Open storage options are common for materials like coal, aggregates, and iron ores. Materials such as grain, sugar, cement, and wood pellets are often stored with enclosed storage systems. Certain commonly used storage methods may not work for all bulk materials. For instance, compaction is a common practice in coal handling to minimize the risk of self-heating in a stockpile. However, if applying compacting to the storage piles of solid biomass, it only stimulates self-heating furthermore.
For a hopper, the cone angle is affected by the wall friction angle and the effective angle of internal friction. Subsequently, the cone angle affects the minimum opening of the hopper and its discharging capacity.
- Equipment characteristics and stacking method
The equipment that should be considered for a stockyard analysis study is not limited to the actual storage choices (e.g. an open storage area or enclosed silos); transshipment equipment such as stackers and reclaimers ought to be taken into consideration as well. These transshipment facilities can also provide extra services such as blending, mixing and homogenization. Such considerations are:
- types of equipment for open or enclosed storage: not all equipment suits both storage types; some will be used only for open storage (e.g. boom type bucket-wheel reclaimers) and other types are for enclosed storage only (e.g. screw stacker-reclaimers). Some equipment can be used for both open and enclosed storage, such as slewing luffing stackers, drum-type reclaimers, and circular portal stacker-reclaimers.
- capacity of required storage and the applied handling equipment types and numbers: the logistical performance of a stockyard is often influenced by the transhipment equipment deployed for stacking and reclaiming; however, the capacity limitation of the actual storage can also affect the capacity of the handling equipment deployed.
- the equipment width and height differs from open storage and enclosed storage, affecting the stockpile dimensions: for instance, for a large-scale bulk terminal it is common to have stockpiles 60–90m wide, and around 15–18m high. For an enclosed storage, the stockpile height depends on equipment and building restrictions (e.g. silos, domes, stackers, and reclaimers).
- Land availability and ground conditions
Equipment dimensions and stacking method affect the required storage land size and consequently the related costs. They are a starting point when looking at greenfield developments. For brownfield development or expansions, the availability and condition of land will often restrict the choices available for an optimum stockpile arrangement.
Soil conditions influence the density of the storage which often relates to the utilization of storage area. Although the bulk material properties are the most important factors, the equipment characteristics, the stacking method, and the strength of the soil are to be considered for storage land size estimation.
Financial factors
In the terminal design, the total investment required for the facility often overrides other design factors. A more holistic approach is required where the choice of the stacking method depends on the bulk material properties and the availability of surface area. A lower CAPEX alternative can often result in a higher OPEX operation, which then has to be burdened over the entire lifecycle. To realize a better ROI or a faster payback period, the CAPEX and OPEX should be balanced. A qualitative and quantitative multi criteria analysis (including cost per tonne and initial investment) should be used to compare the feasible options. terminal storage stock level is zero, under static situation the required storage capacity is related to the ratio of size differences of two types of supply ships. At the same annual throughput, if the size of barges, trains and trucks stays the same, the larger vessels size will cause longer average material storage time. However, the vessel size effect is more influential than the impact from the size of barges, trains and trucks.
Social factors
Because of various activities at a bulk terminal (e.g. loading/unloading operations), a series of environmental impacts need to be taken into account for their influence on local communities and ecosystems. Noise and dust are of major concerns, and as a result bulk terminals are under increasing pressure from legislation because of sustainability guidelines and the increasing awareness for the environment.
Due to these potential threats to the environment and the society, each country in the world has its own environmental regulations that terminal operators and port authorities need to follow. In general, prior to any terminal construction/expansion or port development, an Environmental Impact Analysis (EIA) and increasingly it has become a normal practice to provide the findings of impacts listed in a Environmental Impact Statement (EIS) or equivalent as required by local authorities.
Consequently, bulk terminals nowadays put more focus on both the equipment and handling methods in order to have environmental friendly operations.
Technology
Utilization of software can radically improve stockyard utilization. Planning tools can allow the user to forecast space requirements and prioritize the area clearing to create sufficient space for forthcoming deliveries. Terminal Operating System (TOS) or Terminal Management System (TMS) software can also create prioritization rules to empty specific areas and use bulk density and angle of repose algorithms to allow the user to better understand the capacity of the yard. COMMTRAC from TBA is one such system available in the market.
STORAGE DESIGN
The performance of the terminal is limited to the least performing element in the overall terminal facility. The design of the terminal should cater to handling of the peak loads with regards to storage space and choice of equipment.
Required premises and initial static analysis
The first step is to collect relevant premises for both the initial static analysis and the dynamic analysis with a simulation model. In addition to the bulk material properties and the equipment characteristics, information regarding the number of material types, the stacking method and the logistic flows are also necessary for the stockyard study.
Usually each bulk material needs to be stored separately; hence under the same annual throughput, the more types of materials the larger the storage area will be. If further separation is required (e.g. certified as sustainable biomass materials), it also impact storage demand such as higher required storage land area and higher energy consumptions.
The impact brought from the sizes and the actual arrivals of vessels, barge, trains and trucks are related to the incoming and outgoing logistic flows. An import dry bulk terminal can be used to demonstrate the influence from the effects of size and arrivals. If initially the terminal storage stock level is zero, under static situation the required storage capacity is related to the ratio of size differences of two types of supply ships. At the same annual throughput, if the size of barges, trains and trucks stays the same, the larger vessels size will cause longer average material storage time. However, the vessel size effect is more influential than the impact from the size of barges, trains and trucks.
- Dynamic analysis using simulation modelling approach
The initial analyses regarding the premises are conducted based on static situations where only the average values (e.g. arrival rate, transport mode size) are taken into account. Any kind of incident such as stoppage due to weather condition (e.g. rain), machine breakdowns, and seasonal influences of bulk material availability are not included in the theoretical calculations.
To analyse the effect of time dependent processes, it is necessary to test the performance of the stockyard under various stochastic situations (e.g. the arrival pattern of vessels, influence of constraints/stoppages). This kind of dynamic analyses can only be performed with simulation models that capture the dynamic operations at a dry bulk terminal.
Typically there are more parameters that need to be used as input in addition to the premises used for the initial analyses: equipment efficiency (technical productivity v.s. achieved operational productivity), stoppages (e.g. rainfall, equipment breakdown, scheduled maintenance, hatch changing, shift changing), number of berths, mixture of the transport mode (e.g. vessel mix), seasonal influence, process times (e.g. sampling and weighing).
Furthermore, the arrival patterns of the transport modes are rather important because in reality the arrivals do not completely comply with the schedules. Often the arrivals can be assumed to follow a certain arrival distribution (e.g. uniform distribution, exponential distribution). When the stochastic effects are taken into account, 50% of the required storage capacity is not enough as a safety stock level. Irregular arrivals also may lead to higher storage time; and together with the higher storage capacity the overall costs (including both CAPEX and OPEX).
CASE STUDY
One of the key objectives for a grain terminal was to determine the actual storage capacity required for the planned expansion. The current situation made it difficult to estimate as the logistics environment led to a lot of down-time and inefficient use of the storage space. The terminal was facing with situations where the storage was either near empty or at times completely occupied. Determining the accurate storage capacity was crucial as related investment costs (acquiring land, storage warehouses) were dependent on the success of the project. A dynamic approach using simulation based modelling was applied in meeting the objective.
The base case scenario indicated a peak storage capacity of approximately 90,000 tonnes. This scenario was then tested again with various sensitivities based on local constraints due to weather conditions and logistics environment. It was evident that higher limits for the constraints would raise the peak storage requirement, the simulation analysis allowed to identify these limits as indicated in figure below. From additional rainfall to delays to barges and vessels, the peak storage requirement indicated was in the range of 100,000 tonnes to 150,000 tonnes. The terminal operator was able to determine a optimum storage capacity for a terminal expansion based on the critical investment limit for the projects feasibility, commercial requirements for adequate capacity, and control of the logistics flow.
Nowadays, many terminal operators in the bulk industry are starting to understand the importance and make use of a simulation based modelling approach to determine the optimum storage capacity and make operations efficient. Many bulk terminals around the globe are nearing end of lifecycle for the deployed infrastructure and equipment. As a result of which, many terminal expansion projects are at the threshold of adapting to the new requirements of the industry and the yardsticks of performance.
The quantum leap in equipment technology, automation and software adds a whole new dimension in deciding the right equipment/storage arrangement, which otherwise would have been a case of simple transition and/or expansion project. This dynamic approach allows them to make a quantitative analysis of the most feasible options and assists them in making the correct decisions. New terminal development projects are also adopting this approach to set things right from the start and be prepared for future challenges and remain competitive.
This article has been previously published in DCI 2013 and has been updated to reflect to current date. Read the original published article here.
Share this
You May Also Like
These Related Stories
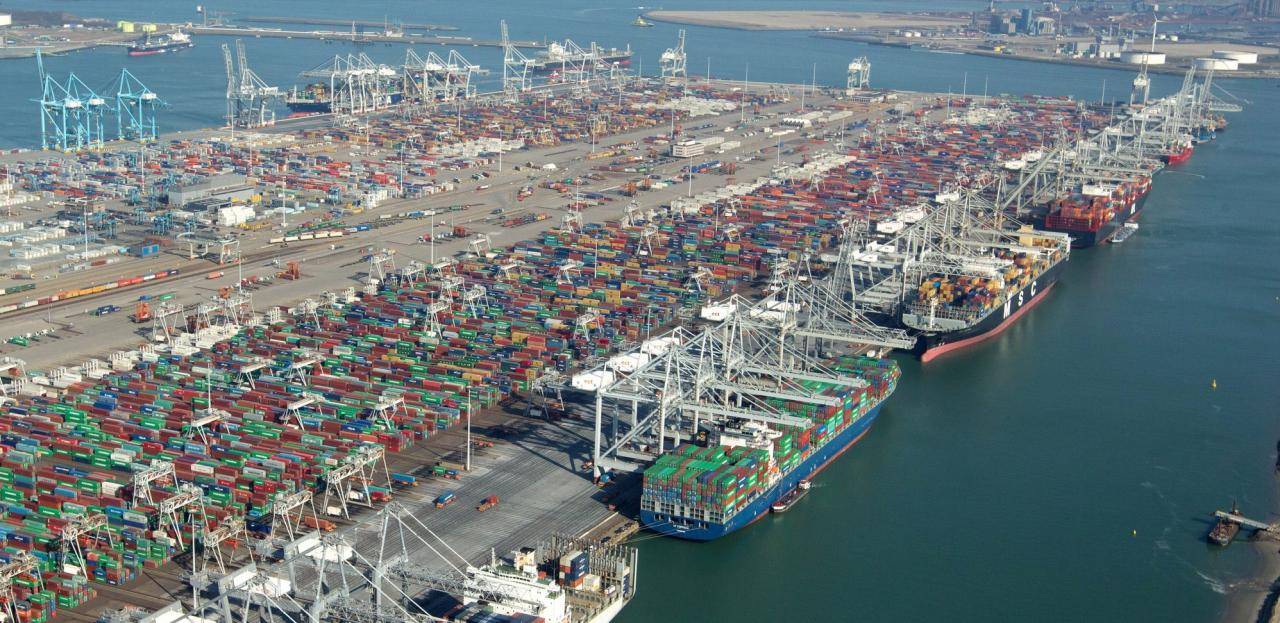
Lean and mean terminal design benefits from advanced modelling
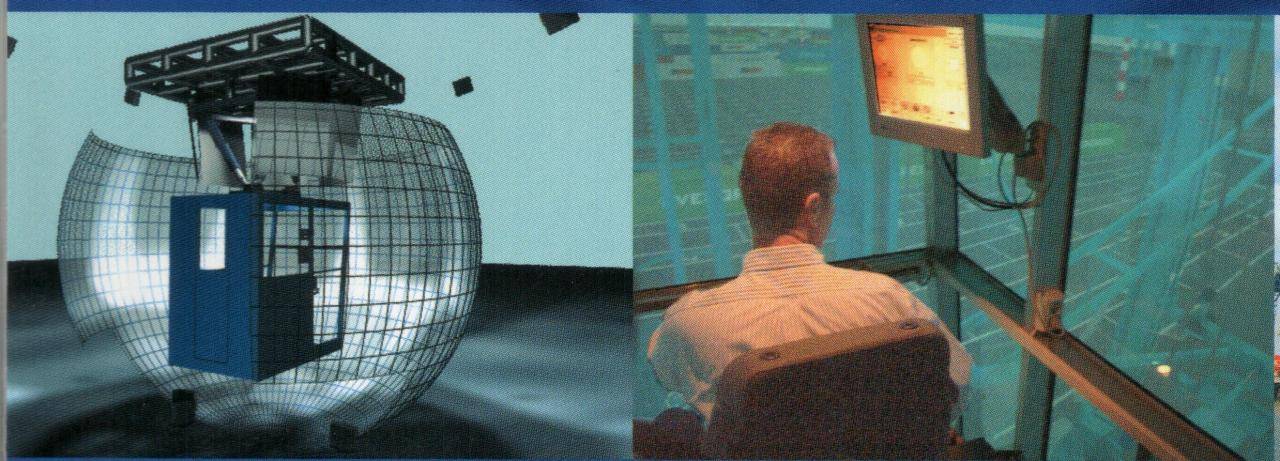
Human Machine Interfaces - the key to productivity?
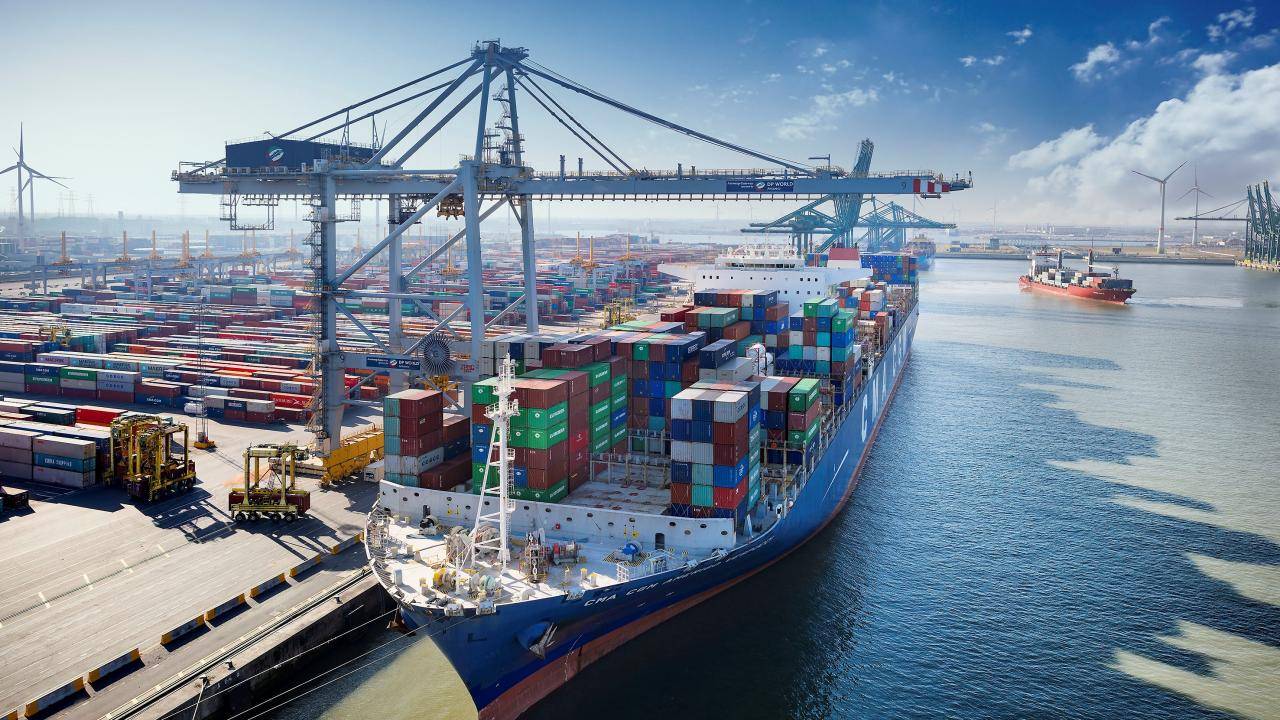