Our Approach to Machinery Safety & Obsolescence
This article is based on a presentation our Automation & Controls Systems Team Leader, Ruben Fernandez, gave at our User Group Conference in April 2024.
In the rapidly evolving landscape of industrial automation, ensuring machinery safety and managing the obsolescence of electronic equipment are critical challenges. This article outlines the principles and strategies for maintaining safety in machinery operations and addresses the issue of electronic and electrical equipment obsolescence. We present a comprehensive approach to safety within TBA and discuss the implications of outdated technology on industrial processes.
Principles of Safety at TBA
- Common Sense: The cornerstone of our safety philosophy is the application of common sense. If an operation seems hazardous, it likely is, and appropriate precautions should be taken.
- Risk Re-evaluation: Safety standards evolve over time. Practices that were deemed safe decades ago may no longer be adequate. Continuous re-evaluation of risks is essential to maintain safety standards in line with current regulations and technologies.
- Application of the Basics: A fundamental approach to risk assessment is critical. This involves not rushing through processes and ensuring a thorough understanding of the basics before proceeding.
- User Collaboration: Engaging closely with machine operators, who have firsthand experience with equipment, ensures that safety protocols are both practical and effective. Documentation and user feedback are pivotal in maintaining safety.
- Legislative Compliance: Adhering to regulations such as the Health and Safety at Work Act of 1974 is not only a legal obligation but a moral one to ensure the well-being of all employees.
Importance of Safety
The primary goal of machinery safety is to ensure that all personnel return home safely and to prevent equipment damage due to malfunctions. Compliance with safety regulations is also crucial to avoid penalties from regulatory bodies and to maintain operational integrity.
Modifying Existing Machinery
When modifying existing machinery, particularly if changes are substantial (e.g., adding automatic controls to a manual system), it is imperative to comply with current regulations.
Risk Assessment
A robust risk assessment is fundamental to safety management. It involves identifying potential hazards and implementing control measures to mitigate these risks. This process is similar to everyday risk evaluations, such as assessing whether it is safe to cross a road. The primary goal is to eliminate hazards where possible and reduce their impact through various control measures.
Hazard Mitigation Strategies
- Elimination: Removing hazards entirely, such as replacing a dangerous hoist with a safer conveyor system, is the most effective way to ensure safety.
- Reduction: Reducing the severity of potential accidents, such as slowing down machinery in high-risk areas, minimizes the impact of hazards.
- Isolation: Restricting access to hazardous areas, such as fencing off dangerous machinery, helps to prevent accidents.
- Functional Safety Devices: Implementing reliable safety devices, such as emergency stop buttons and safety relays, ensures machinery can be safely controlled under various conditions.
Reliability of Safety Systems
Safety devices are highly reliable to prevent dangerous failures. For instance, a safety relay that prevents machinery from moving in the event of a failure is crucial for maintaining a safe operating environment. The reliability of safety systems is often quantified by standards such as ISO 13849 and IEC 61508, which provide performance levels (PL) and safety integrity levels (SIL) respectively.
Recognising Obsolescence
Electronic equipment becomes obsolete when it can no longer be supported by manufacturers or integrated with current technologies. Signs of obsolescence include:
- Discontinued support and parts availability.
- The need for outdated software or operating systems.
- Rising costs for spare parts due to limited supply.
- The inability to integrate with modern network protocols.
Examples of obsolescence:
- Siemens S5: Siemens has phased out support for its S5 series PLCs, making it challenging for users to maintain and repair these systems. Companies are encouraged to upgrade to newer models to ensure continued support and functionality.
- Rockwell Automation: The discontinuation of the SLC 500 series highlights the need for industries to plan for upgrades to avoid reliance on obsolete technology.
Planning for Upgrades
Transitioning from one family of equipment to another is not straightforward and requires careful planning. It is crucial to start early to ensure that systems remain supported and operationally viable. Upgrading within the same family is usually simpler and less disruptive than switching to a completely new technology.
Conclusion
Ensuring machinery safety and managing the obsolescence of electronic equipment are fundamental to maintaining a safe and efficient industrial environment. By adhering to safety principles, continuously evaluating risks, and proactively managing technology lifecycles, companies can protect their employees and assets while remaining compliant with regulatory standards.
If you would like to discuss any of the points raised in this article further, please get in touch.
Share this
You May Also Like
These Related Stories
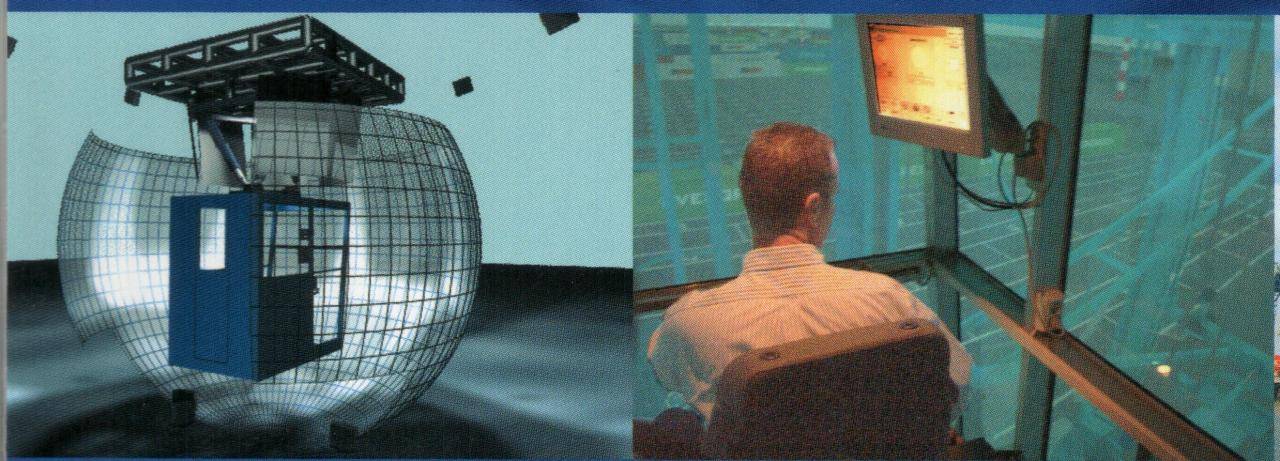
Human Machine Interfaces - the key to productivity?
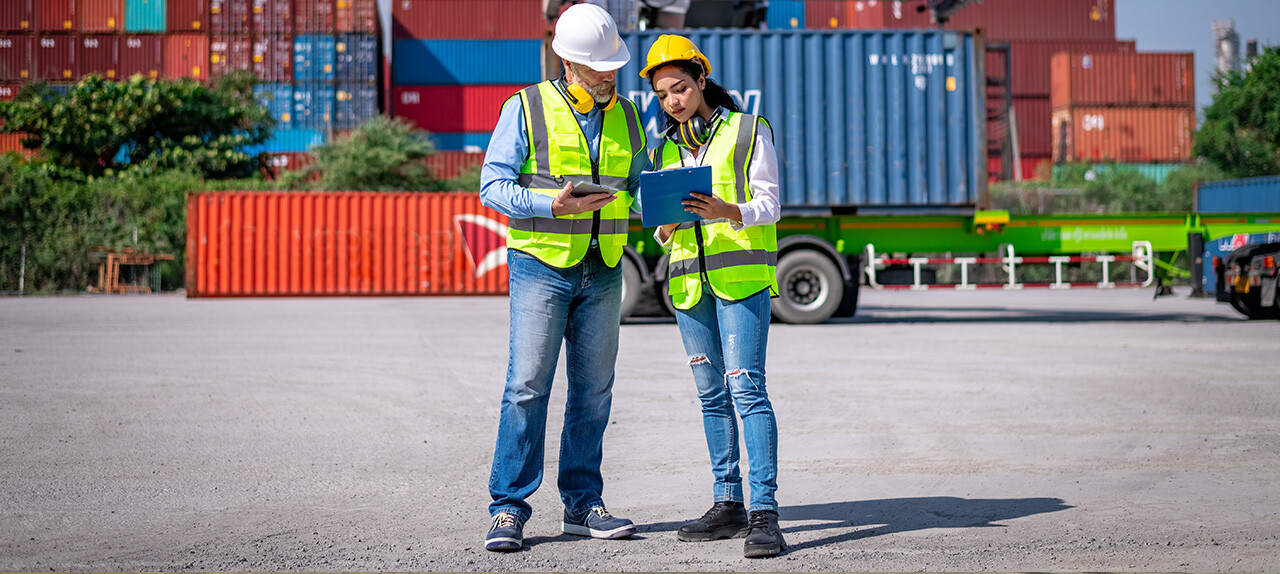
The reach of 'freemium' software
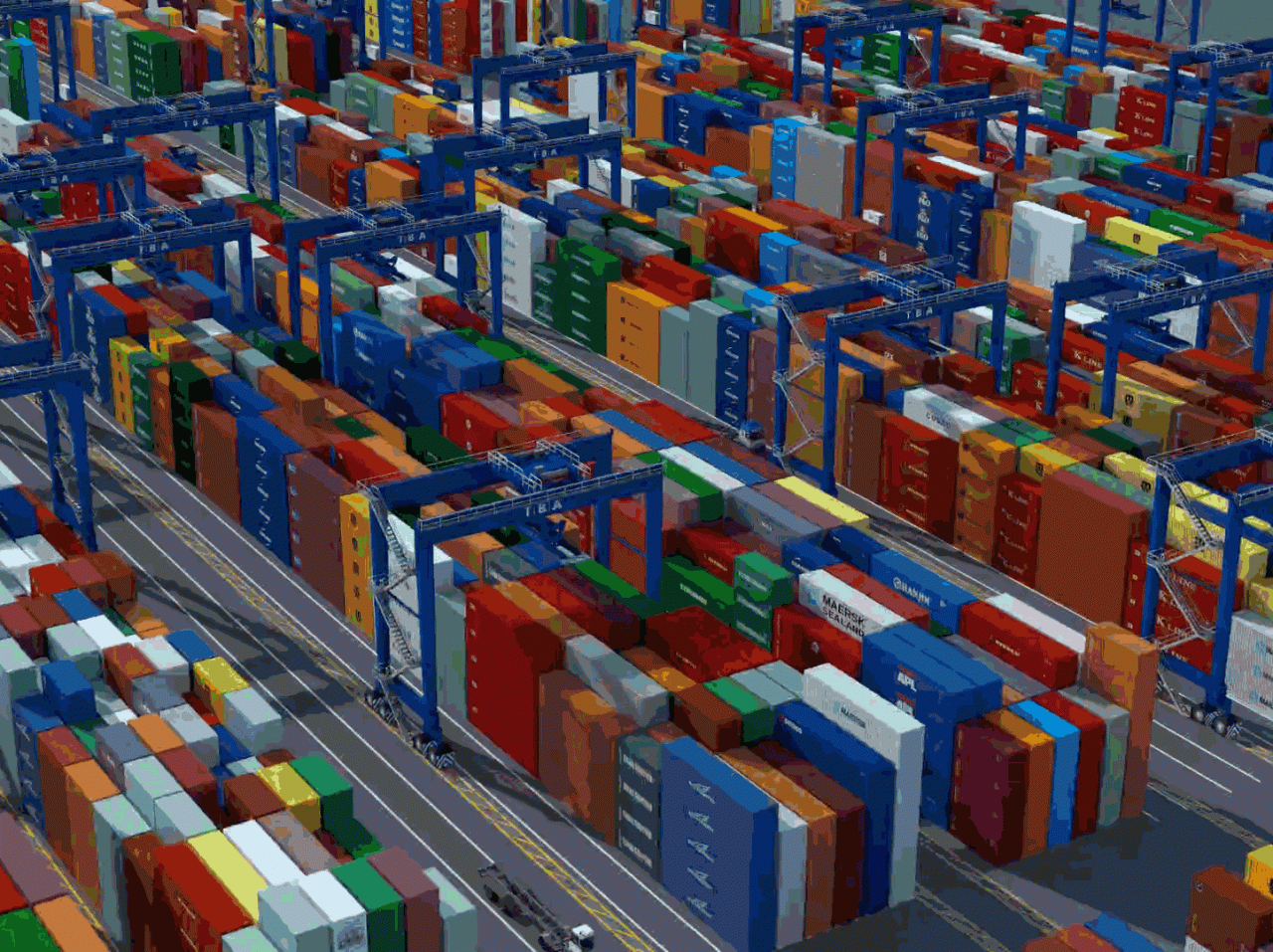